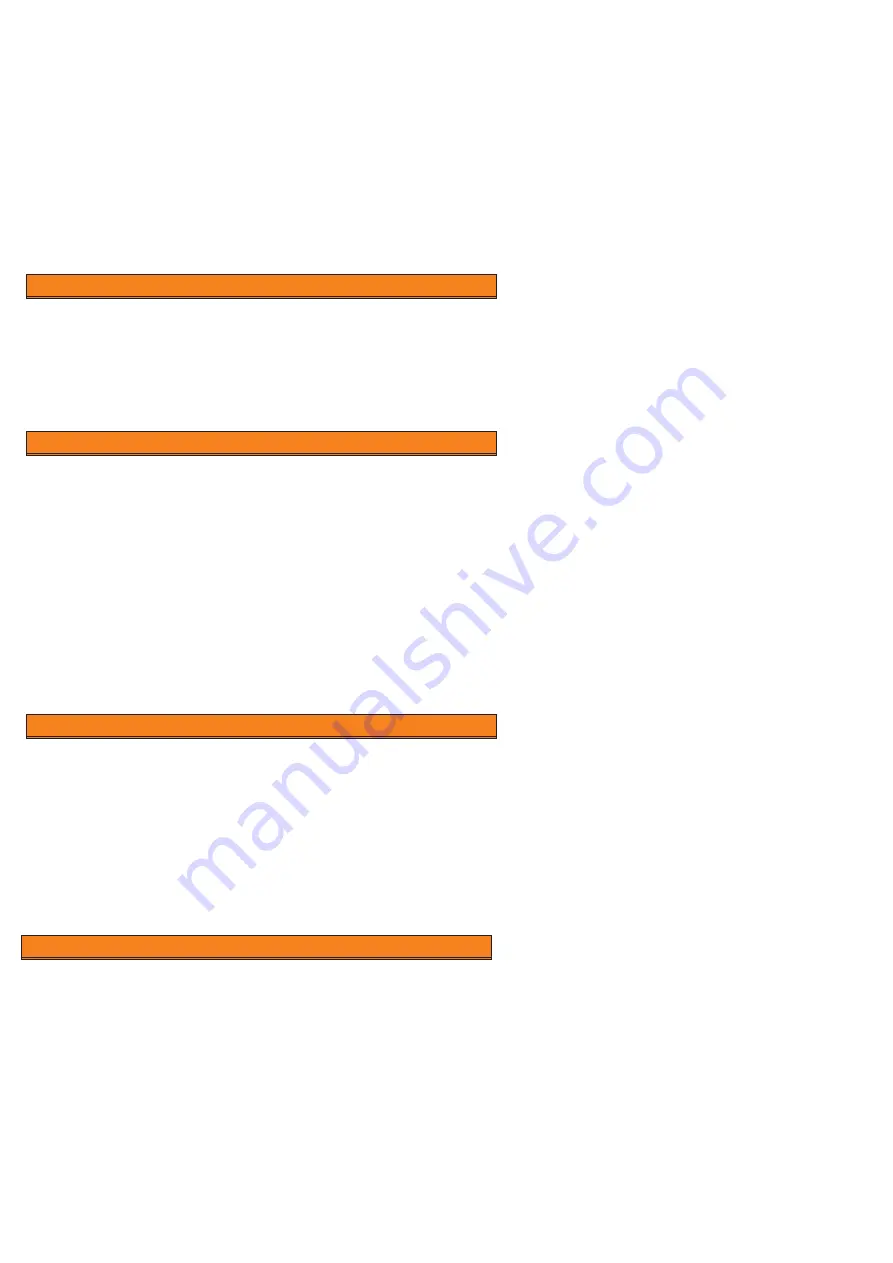
Crewsaver -
Servicing Manual: Crewsaver Crewfit 275 Lifejacket
Date: November 2016
Issue No: 14
Page
of 43
32
6.1.1.7. If the Lifejacket fails the air holding test inspect as follows.
6.1.1.7.1 With the lifejacket inflated carefully brush the surface with a weak solution of soap and water or
alternatively lower the lifejacket into a tank of water to observe for bubbles.
6.1.1.7.2 Identify and mark the source of leakage. Wash off in clean water and allow to dry naturally in air.
Special attention is to be given to the manifold Schrader core and the oral top-up valve.
.
6.1.2
If the test is satisfactory deflate the Lifejacket in preparation for re-assembly. Refer to Section 8.
6.1.2.1. Insert the inverted oral valve dust cap into the top of the oral valve and expel the air.
The Lifejacket may also
be deflated using the Crewsaver Venturi Vacuum System. For part number refer to section 9.
6.1.3
Effect repairs in accordance with the Repair Procedures within the limits defined in Section 7.
6.1.4
Subsequent to remedial action being taken (see Section 7), retest the lifejacket in accordance with Section 6.
6.2.1. Oral Valve.
6.2.1.1. When removing the test adapter from each oral valve check that the oral valve reseats. If in doubt this
may be checked by placing the valve underwater.
6.2.2 Schrader Valve.
6.2.2.1 Should a leak be found in the Schrader valve the faulty core must be removed and a new valve
inserted using the Torque Screwdriver from the tool kit.
6.3.1 Operational Test for Halkey Roberts Manual Operation.
6.3.1.1 Remove the operating mechanism from the lifejacket. With the cylinder also removed, pull the lever on
the side of the operating head, and check that the firing pin is visibly moving inside the open end.
6.3.1.2 If the lever does not move, or the firing pin is not clearly moving, the operating head must be
replaced. Refer to Section 9 for part number.
6.3.2 Operational Test for Crewsaver Mk5 Automatic Operating Heads (to be performed when capsules have expired).
6.3.2.1 Remove the operating mechanism from the lifejacket and remove the cylinder.
6.3.2.2 Assemble the expired capsule onto the body of the operating mechanism.
6.3.2.3 Place the complete unit into water and check that the unit operates within 5 seconds.
6.3.2.4 If the mechanism fails to pass this test replace the complete unit. Refer to Section 9 for part
Number of the replacement part.
NOTE: All failures of this test must be reported to Crewsaver. Crewsaver may require the failed units to be returned.
Please do not discard.
6.4.1 If the retro reflective tape shows any signs of degradation the following tests shall be carried out in accordance
with Marine Guidance Note MGN 105 (M+F) Issued by the UK Marine and Coast guard Agency March 1999.
6.4.1.1 Place a new piece of the same retro-reflective material to, and on the same plane as, a
representative piece of material fitted to the appliance.
6.4.1.2 Pour water over both pieces of material.
6.4.1.3 Using a powerful torch or "Aldis" lamp held at eye level, compare the performance of the two pieces of
material from a distance of 10 Metres.
6.4.1.4 If a noticeable deterioration in performance is observed then the retro-reflective material on the
appliance should be replaced.
6.4.1.5 Dry off the lifejacket before re-packing.
6.5.1. Testing Procedure for lights fitted to lifejackets.
The following sea lights have been fitted to Crewsaver Commercial and Leisure lifejackets.
All light units used have a detailed expiry date, after which the light should be carefully disposed of.
6.5.1.1 Daniamant L6 The Daniamant L6 can be tested using the switch located on the right side (as looked
at).
6.5.1.2 Crewsaver CSL Water Activated Light.
Test the light by immersing the sensor in water. The light must
flash, remove the light from the water and dry it. The light must stop flashing. If the light does not flash
the unit has expired and must be replaced.
6.3
Inflation Mechanisms
6
Section
6.2
Valves
6.4
Retro Reflective Tape
6.5
Lights and Batteries