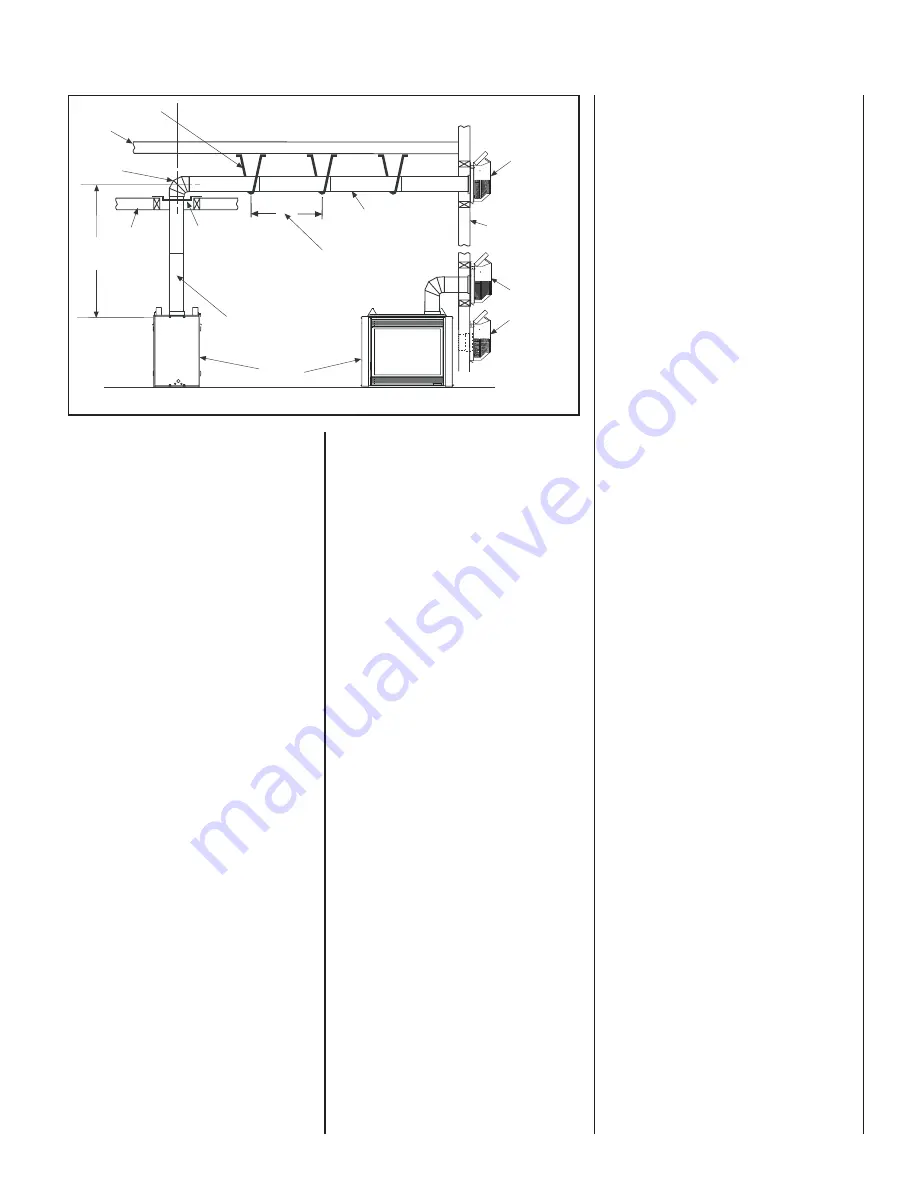
NOTE: DIAGRAMS & ILLUSTRATIONS ARE NOT TO SCALE.
19
HORIZONTAL (OUTSIDE WALL)
TERMINATION SYSTEM
See
Figure 32
, and
Figures 35
to
40
and
their associated Horizontal Vent Table which
illustrates the horizontal venting confi gura-
tions that are allowed to be used with these
appliances.
Secure Vent
pipe applications are
shown in these fi gures;
Secure Flex
pipe may
also be used (see
Page 24
)
. A Horizontal Vent
Table summarizes each system’s minimum and
maximum vertical and horizontal length values
that can be used to design and install the vent
components in a variety of applications.
Both of these horizontal vent systems terminate
through an outside wall. Building Codes limit or
prohibit terminating in specifi c areas. Refer to
Figure 6
on
Page 8
for location guidelines.
Secure Vent
SV4.5 direct vent system compo-
nents are unitized concentric pipe components
featuring positive twist lock connection, (
refer
to
Figure 20
on
Page 15
).
All of the appli-
ances covered in this document are fi tted with
collars having locking inclined channels. The
dimpled end of the vent components fi t over
the appliance collar to create the positive twist
lock connection.
A.
Plan the vent run -
Analyze the vent routing and determine the
types and quantities of sections required
4-1/2" (114 mm), 10-1/2" (267 mm), 22-1/2"
(572 mm), 34-1/2" (876 mm) and 46-1/2" (1181
mm) net section lengths are available. Plan the
vent lengths so that a section joint does not occur
within the space defi ned by ceiling joists, roof
rafters or wall studs. Make allowances for elbows
as indicated in
Figure 23
on
Page 16
.
Figure 32 -
TYPICAL HORIZONTAL VENT INSTALLATION
See
Figures 21
&
22
for verti-
cal vent section support.
Horizontal / Inclined Run
Support
Brackets
Building
Support
Framing
SV4.5E90
Elbow
Ceiling
Firestop / Spacer
SV4.5VF
When Using Secure Flex,
Use Firestop / Spacer SF4.5VF
Fireplace
SV4.5L6/12/24/36/48
Vent Sections
Vertical
Rise
Support Bracket Spacing
Every 5 ft (1.52 m)
Exterior
Wall
To add another vent component to a length
of vent run, align the dimpled end of the
component over the inclined channel end of
the previously installed section, adjusting the
radial alignment until the four locking dimples
are aligned with the inlets of the four incline
channels of the previous section. Push the vent
component against the previous section until it
fully engages, then twist the component clock-
wise running the dimples down and along the
incline channels until they seat at the end of the
channels.
This seating position is indicated
by the alignment of the arrow and dimple as
shown in
Figure 20 on Page 15.
F.
Install fi restop / spacer at ceiling -
When using Secure Vent, use SV4.5VF fi restop
/ spacer at ceiling joists; when using Secure
Flex, use SF4.5VF fi restop / spacer. If there is
living space above the ceiling level, the fi restop/
spacer must be installed on the bottom side of
the ceiling. If attic space is above the ceiling,
the fi restop/ spacer must be installed on the
top side of the joist. Route the vent sections
through the framed opening and secure the
fi restop / spacer with 8d nails or other ap-
propriate fasteners at each corner.
Remember to maintain 1" (25 mm) clearance
to combustibles, framing members, and attic
or ceiling insulation when running vertical
chimney sections. Attic insulation shield
(96K94) may be used to obtain the required
clearances indicated here. See installation
accessories Tables on
Pages 31 and 32
.
G.
Support the vertical run sections -
See Step E on Page 15.
H. Change vent direction -
At transition from
or to a horizontal / inclined run, install the
SV4.5E45 and SV4.5E90 elbows in the same
manner as the straight vent sections. The
elbows feature a twist section to allow them to
be routed about the center axis of their initial
collar section to align with the required direc-
tion of the next vent run element.
Twist elbow
sections in a clockwise direction only so as
to avoid the possibility of unlocking any of
the previously connected vent sections.
See
Figure 20 on Page 15
.
I.
Continue installation of horizontal / inclined
sections -
Continue with the installation of the
straight vent sections in horizontal / inclined run
as described in
Step E
. Install support straps
every 5 ft. (1.52 m) along horizontal / inclined
vent runs using conventional plumber’s tape.
See
Figure 32.
It is very important that the
horizontal / inclined run be maintained in a
straight (no dips) and recommended to be in
a slightly elevated plane, in a direction away
from the fi replace of 1/4" rise per foot (20 mm
per meter)
which is ideal, though rise per foot
run ratios that are smaller are acceptable all the
way down to at or near level. Use a carpenter’s
level to measure from a constant surface and
adjust the support straps as necessary.
Maintain a minimum 1" (25 mm) clearance to
combustibles on the vertical sections. Clear-
ances for the horizontal runs are; 3" (76 mm)
on top, 1" (25 mm) on sides, and 1" (25 mm)
at the bottom.
B.
Frame exterior wall opening -
Locate the center of the vent outlet on the exte-
rior wall according to the dimensions shown in
Figures 13 & 14
on
Pages 11 & 12
.
Cut and/or frame an opening, 10-1/2" x 12 1/8"
(267 mm x 308 mm) inside dimensions, about
this center.
C.
Frame ceiling opening -
If the vertical route
is to penetrate a ceiling, use plumb line to locate
the center above the appliance. Cut and/or frame
an opening, 10-1/2" x 10-1/2" (267 mm x 267
mm) inside dimensions, about this center (refer
to
Figure 19
on
Page 15
)
.
D. Attach vent components to appliance -
To
attach a vent component to the appliance collar,
align the dimpled end over the collar, adjust-
ing the radial alignment until the four locking
dimples are aligned with the inlets of the four
incline channels on the collar (
refer to
Figure
20
on
Page 15
).
Push the vent component against the collar
until it fully engages, then twist the component
clockwise, running the dimples down and along
the incline channels until they seat at the end of
the channels. The unitized design of the
Secure
Vent
components will engage and seal both the
inner and outer pipe elements with the same
procedure. Sealant and securing screws are
not required.
E. Attach vent components to each other
-
Other vent sections may be added to the
previously installed section in accordance with
the requirements of the vent tables.
SV4.5HT-2
Termination
Shown
SV4.5HT-2
Termination
Shown