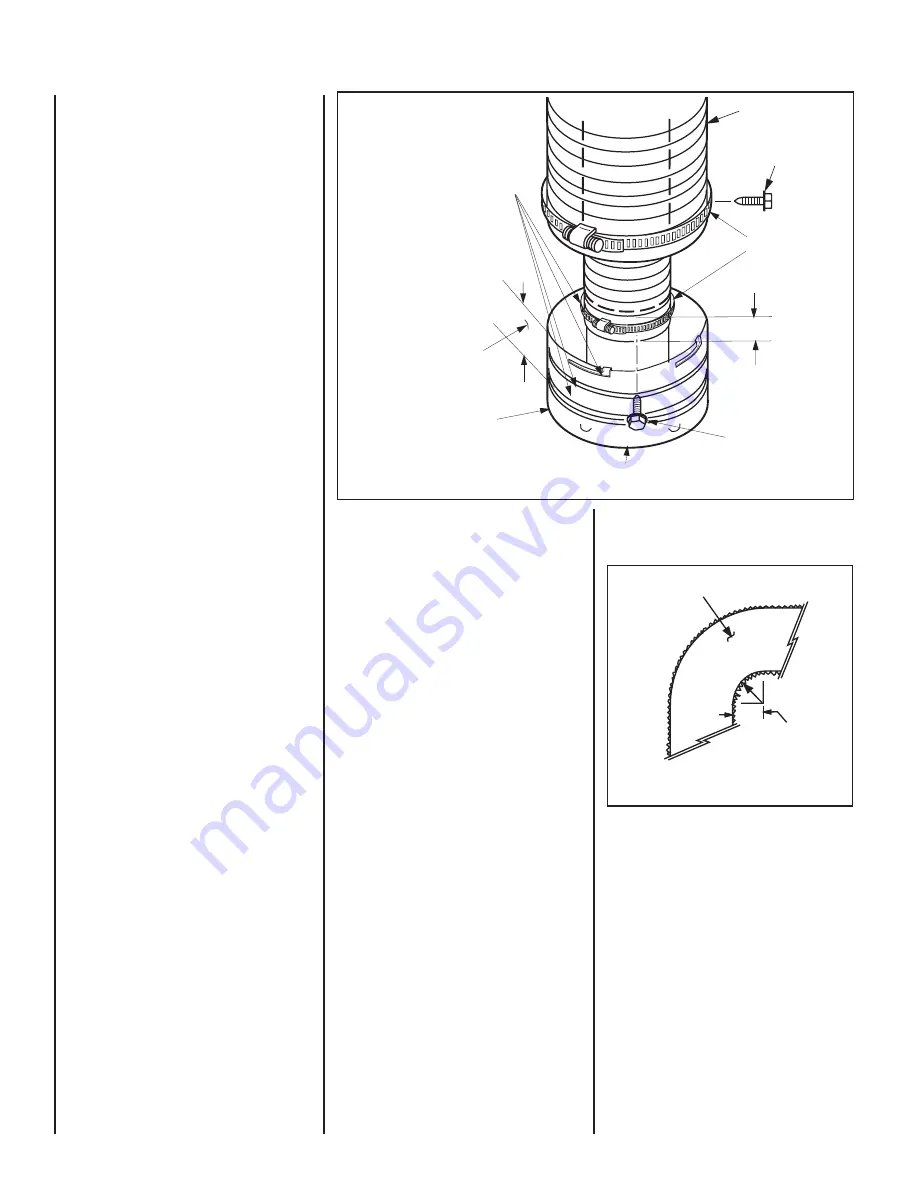
NOTE: DIAGRAMS & ILLUSTRATIONS ARE NOT TO SCALE.
24
See the appropriate sections and Figures shown
throughout the venting section for their instal-
lation requirements.
Note: Outer Pipe Is Pulled Away To Show
The Detail of The Inner Pipe
APPLY ONLY MIL-PAC BLACK
HIGH TEMPERATURE SEALANT
(Cat. No. 10K81) to the outside
surface of both collars of the
adapter (be especially careful to
fi ll the grooves of the outer collar
to be covered by the fl exible pipe)
and slide fl exible pipe over inner
and outer adapter collars.
1-3/4 inch (44 mm) Flexible
Pipe and Adapter Outer Collar
Overlap
Adapter (SV4.5RF)
Attach Adapter to Appliance
Collar, or Secure Vent Sections
Flex Vent
Gear Clamps
Securing Screw
- 3 Places, 120° apart
(equally spaced) Just
Below Gear Clamp
1-3/4 in. (44 mm) Flexible
Pipe and Adapter Inner Collar
Overlap
Securing Screw - 3 Places
Equidistant (equally spaced)
Just Below Gear Clamp)
Figure 41
VERTICAL OR HORIZONTAL VENTING USING
SECURE FLEX
KITS AND COMPONENTS
Secure Flex
venting kits and components
may be used in any venting application in
place of rigid
Secure Vent
(SV4.5) direct vent
components. All restrictions, clearances and
allowances that pertain to the rigid piping apply
to the fl exible venting.
Secure Flex
kits may
not be modifi ed; also, under no circumstances
may separate sections of fl ex pipe be joined
together
.
Using adapter (SV4.5RF),
Secure Flex
kits
may be added to the end of a vent run made
up of rigid
Secure Vent
(SV4.5) vent sections
provided that doing so does not violate any of
the venting length, height, routing, horizontal
to vertical ratio requirements or clearance
considerations detailed in this manual.
Secure Flex
kits come with an adapter that
can be fi tted to the inclined channel end of the
last
Secure Vent
(SV4.5) vent section in a rigid
system in the exact same fashion as any other
Secure Vent
section.
Align the dimpled end of the adapter over
the previously installed section or appliance
collar, adjusting the radial alignment until the
four locking dimples of the adapter are aligned
with the inlets of the four incline channels of
the last vent section or collar. Push on the
adapter until it fully engages, then twist the
adapter clockwise running the dimples down
and along the incline channels until they seat
at the end of the channels.
Attach the fl exible vent to the adapter as fol-
lows
(see
Figure 41
)
:
A. Install the Inner Flex Pipe -
1.
Install the small gear clamp loosely around
the inner fl exible vent pipe, push it back out
of the way.
2.
Apply a bead of
Mill-Pac Black (700° F) high
temperature sealant - Catalog No. 10K81
to the inner adapter collar, approximately
1/2
inch from the end.
3.
Pull and extend the inner fl exible vent
pipe.
4.
Slide the inner fl ex pipe over the adapter col-
lar. Ensure the fl exible vent pipe completely
engages the adapter collar to a distance of
1-3/4
inches from the end, and that it is free
from damage or tears.
5
. Slide the gear clamp down and tighten it
fully to secure the fl exible vent to the adapter
inner collar approximately 3/4 inch from the
end of the fl ex.
6
. Install
three screws 120 degrees apart
through the fl exible vent pipe and into the
adapter collar just below the gear clamp to
provide additional security to the connec-
tion.
B. Install the Outer Flex Pipe -
1.
Install the large gear clamp loosely around
the outer fl exible vent pipe, push it back out
of the way.
2.
Apply a bead of
Mill-Pac Black (700° F) high
temperature sealant - Catalog No. 10K81)
to the outer adapter collar; to the grooves
of the collar which extend approximately 1
inch from the end and to the fl at surface,
approximately 1-3/8 inches from the end.
3.
Pull and extend outer fl exible vent pipe.
4.
Slide the outer fl ex pipe over the adapter col-
lar. Ensure the fl exible vent pipe completely
engages the adapter collar to a distance of
1
³⁄₄
inches from the end, and that it is free
from damage or tears.
5
. Slide the gear clamp down and tighten it
fully to secure the fl exible vent to the adapter
outer collar approximately 3/4 inch from the
end of the fl ex.
6.
Install
three screws 120 degrees apart
through the fl exible vent pipe and into the
adapter collar just below the gear clamp to
provide additional security to the connec-
tion.
C. Route Flex Vent -
Ensure that the fl ex vent is properly routed to
provide the required clearance.
Do not
allow the
fl exible vent to bend in a radius tighter than 5"
(127 mm). Refer to
Figure 42
. Space out the
internal fl ex vent spacers evenly - approximately
every 6 inches - and avoid kinking of inner pipe.
Support horizontal sections of fl ex with metal
straps at 2 foot (0.61 m) intervals.
D. Install Firestop / Spacers at ceilings and
walls -
When Secure Flex penetrates a wall or
ceiling, a fi restop / spacer is required: use the
SF4.5 VF fi restop / spacer for ceilings and the
SF4.5 HF fi restop / spacer for walls.
E. Attach Flex Vent to Termination -
Secure Flex
components can be purchased
separately and attached to bulk lengths of
Se-
cure Flex
fl exible tubing cut to size at the job
site. Secure the fl exible vent to the
Secure Flex
terminations in the same manner (see
Figure
41)
as it was attached to the adapter.
Note: Secure Flex vent must be attached to
Secure Flex terminations only. DO NOT sub-
stitute Secure Vent terminations or the Secure
Vent adapter for Secure Flex components.
The collars of Secure Flex terminations and
adapters have a different diameter than that
used with the Secure Vent pipe. Additionally,
Secure Flex components have an extended
length center tube for use in attaching the
fl exible vent.
Flexible Vent
Section
5” (127 mm)
Radius
Minimum
Figure 42