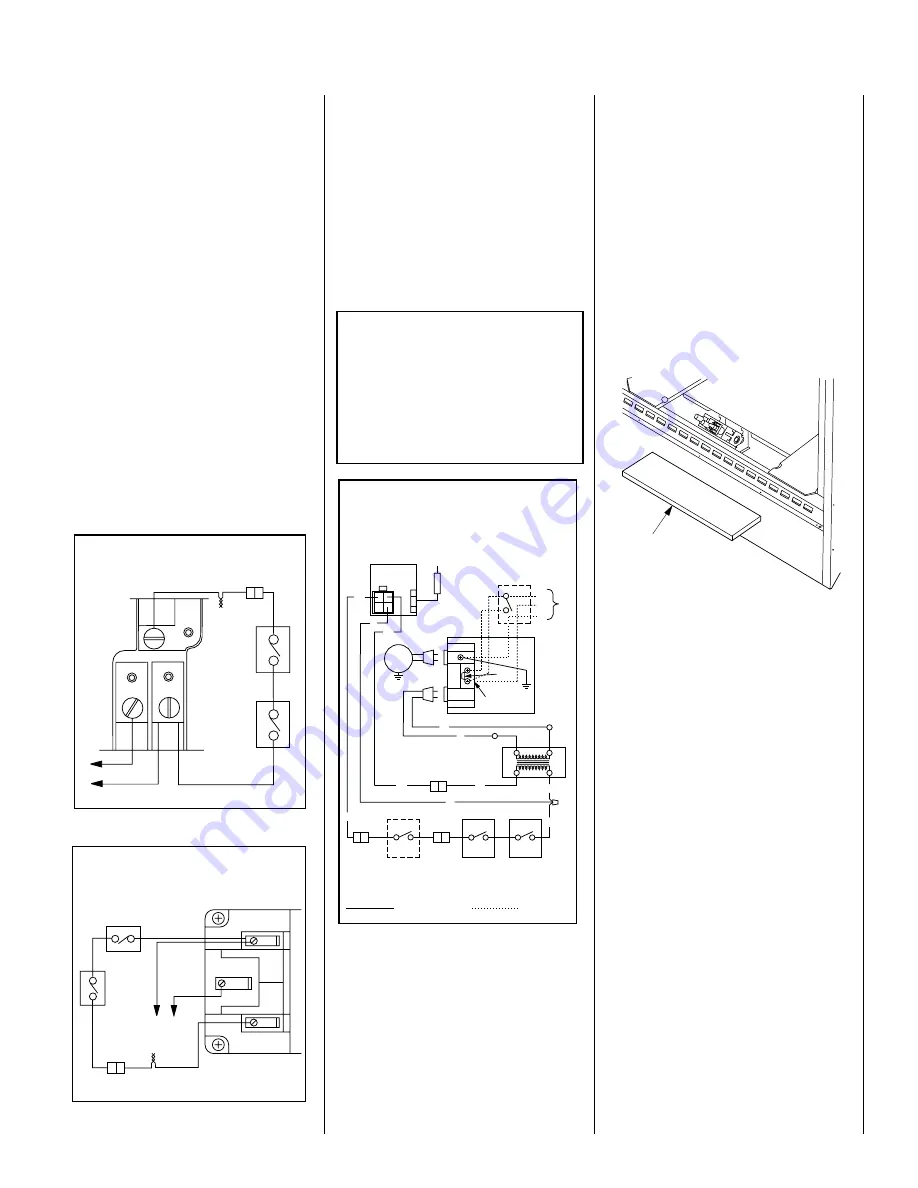
7
NOTE: DIAGRAMS & ILLUSTRATIONS NOT TO SCALE.
Figure 12
CAUTION: DO NOT CONNECT THE WALL
SWITCH TO A 120V POWER SUPPLY.
Step 5. Field Wiring – Refer to Section A for
millivolt appliances and Section B for electronic
appliances.
A. Millivolt Wiring – Units may be fitted at the
factory with either a Honeywell millivolt gas
control valve or an SIT millivolt gas control
valve. Both valves have been tested with and
approved for use with these appliances and
are listed accordingly. Refer to
Figure 11 for
wiring of Honeywell systems and
Figure 12
for wiring of SIT systems.
The gas valve has been set in place and has been
pre-wired at the factory. No additional wiring is
required unless the optional wall switch or op-
tional remote control kit is to be installed. Locate
the optional wall switch or optional remote con-
trol in the desired location and connect the
millivolt wire
(see Figures 11 and 12 ).
Note: Optional wall switch not supplied. If the
optional wall switch is not installed, the ends of
the 15' coiled wire must be connected with a wire
nut (not supplied) for the appliance to operate.
Figure 13
Figure 11
Figure 14
Step 6. Connecting Gas Line – Make gas line
connections. All codes require a shut-off valve
mounted in the supply line.
Figure 16 illus-
trates two methods for connecting the gas
supply. The flex-line method is acceptable in
the U.S., however, Canadian requirements
vary depending on locality. Installation must
be in compliance with local codes.
A. Mix a 50% dish soap, 50% water solution.
B. Light the appliance (refer to the lighting
instructions provided in the Homeowner's Care
and Operation Instructions).
C. Brush all joints and connections with the
soapy water solution to check for leaks. If
bubbles are formed, or gas odor is detected,
turn the gas control knob to the “OFF” position.
Either tighten or refasten the leaking connec-
tion and retest as described above.
D. When the gas lines are tested and leak free,
observe the individual tongues of flame on the
burner. Make sure all ports are open and
producing flame evenly across the burner. If
any ports are blocked, or partially blocked,
clean out the ports.
Step 7. Installing Outside Air Kit – These
appliances are equipped with an outside (make-
up) air door and integral actuator arm. If the
appliance is to be installed with an outside air
vent system, use only Lennox Models FAOK-4
or FAOK-4LD Combustion Air Kits.
After completing the installation of the optional
combustion air vent system the actuator arm
must be put in service and tested to ensure
proper operation before completing any enclo-
sure around the firebox. Failure to do so may
result in extensive and costly rework.
The gas control valve is located in the lower
control compartment. To access the valve re-
move the refractory access panel and set aside
(Figure 14 ). The millivolt control valve has a
³⁄₈
"
(10 mm) NPT thread inlet port. The electronic
control valve has a
¹⁄₂
" (13 mm) NPT thread inlet
port and is fitted with a
¹⁄₂
" x
³⁄₈
" (13 mm x 10 mm)
NPT fitting. Both the millivolt and electronic
models are fitted with a 3" (76 mm) long nipple,
³⁄₈
" NPT. Plan the connections accordingly.
Secure all joints tightly using appropriate tools
and sealing compounds (ensure propane resis-
tant compounds are used in propane applica-
tions). Turn on gas supply and test for gas leaks
using a soapy water solution. Never use an
open flame to check for leaks.
B. Electronic Wiring – The electronic appliance
must be connected to the main power supply.
To install:
1. Route a 3-wire 120V 60Hz power supply to
the appliance junction box and ground.
(See
Figures 13 and 15 ).
2. Locate and install a low voltage (24V) wall
switch (not supplied) in the desired location.
Connect the low voltage wire to this switch
(see
Figure 13 ).
3. After wiring is complete, replace the appli-
ance junction box cover and secure with the hex
head screws previously removed.
IMPORTANT: Ground lead must be connected
to the green screw located on the outlet box.
See
Figure 13 . Failure to do so will result in
a potential safety hazard. The appliance must
be electrically grounded in accordance with
local codes or, in the absence of local codes,
the National Electrical Code, ANSI/NFPA 70-
(latest edition). (In Canada, the current CSA
C22-1 Canadian Electrical Code.)
Refractory
Access Panel
SIT Valve
Shown
1. If any of the original wire as supplied must be replaced,
1.
it must be replaced with
Type AWM 200
°
C – 18 GA. wire.
2. 120V, 60Hz – Less than 3 amps.
BK
Junction Box
Transf.
120 V.
24 V
Factory Wired
Field Wired
BL
Electronic Wiring Diagram (Honeywell)
(Optional ON/OFF Switch Wiring)
R
BK
BL
To Opposite Side
OPT
FAN
G
W
OPT. ACCESSORY
SWITCH
120
VAC.
BK
LIMIT
SWITCH
W
Gas Valve
B
BL
OPTIONAL
ON/OFF SWITCH
OR
WALL SWITCH
R
R
IGNITER
CONTROL
PILOT
ASSEMBLY
Break
Off Tab
DAMPER
SWITCH
BK
BK
WHT
BK
BK
SIT Millivolt Wiring Diagram
* For Wall Switch Attachment Only.
If any of the original wire as supplied must be replaced, it
must be replaced with
Type AWM 200
°
C – 18 GA. wire.
Thermopile
TH
TP
TH
TP
Limit
Switch
Damper Switch
BK
BK
BK
BK
WHT
*
Thermopile
Damper
Switch
TH
TP
TH
TP
Honeywell Millivolt Wiring Diagram
If any of the original wire as supplied must be replaced, it
must be replaced with
Type AWM 200
°
C – 18 GA. wire.
TH
TPTH
TP
* For Wall Switch Attachment Only.
*
Limit
Switch
BK
WHT
BK
BK
BK