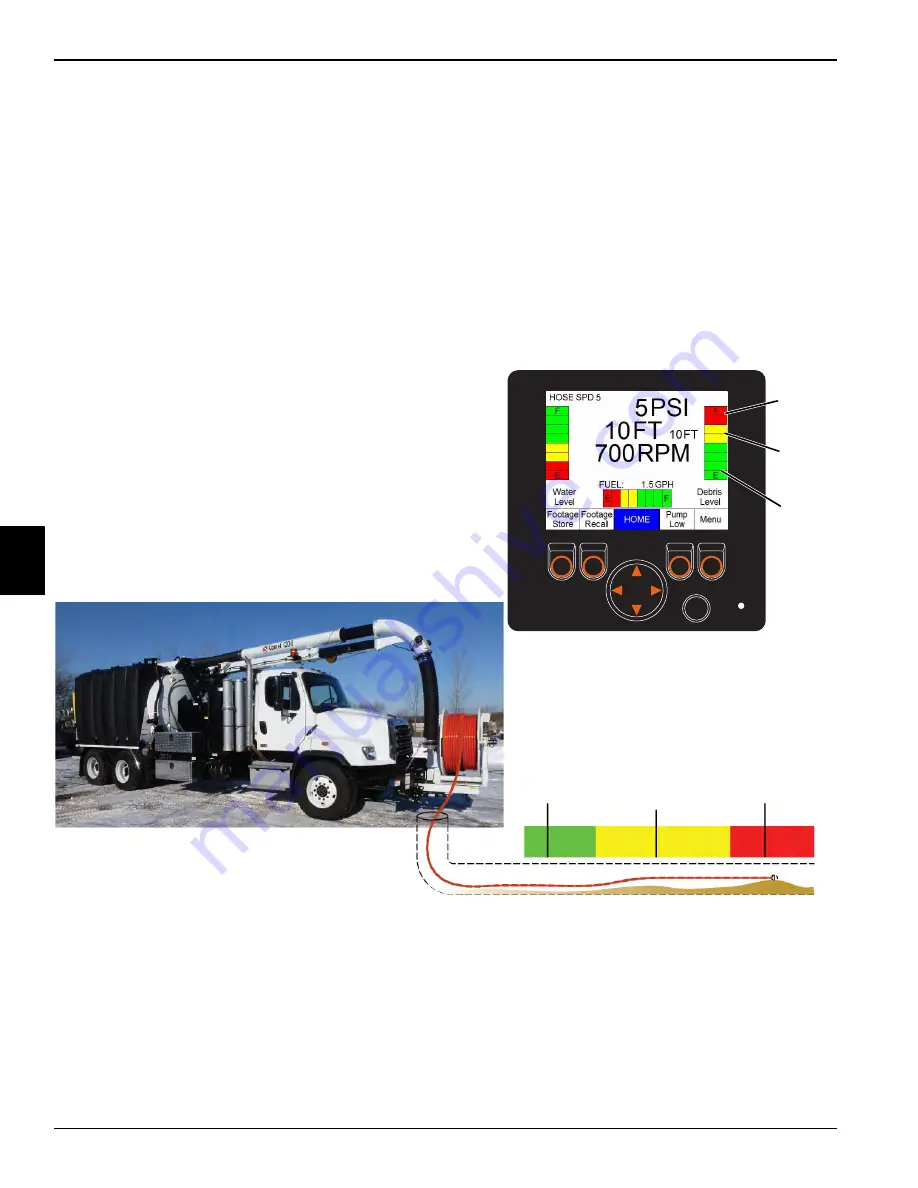
5-2
Publication: 0028607
WATER RECYCLING SYSTEM
5
Typical Recycling Operation
The Camel recycling truck has the capability of recycling
water used during sewer jetting. It must be noted that
operations during water recycling differ from a standard
sewer cleaning operation that does not utilize water
recycling.
When utilizing the Camel water recycling system, the
water and debris together are being deposited into the
debris tank. The water is then separated and filtered from
the debris and sent back through the jetting line to
continue cleaning the sewer line.
Typically the truck will vacuum water and debris faster
than it can be filtered and jetted back into the sewer. The
operator must pay close attention to the acculevel display
to ensure there is enough room for debris. Recycled
water must be used at a rate that allows enough room in
the debris tank for the debris being vacuumed.
See the example below for debris level vs paid out jetting
line. As the jetting line is paid in, the water in the debris
tank should be depleted at a rate similar to what is
shown. Once within 200 feet of the manhole, the operator
must make sure the water level in the debris tank is low
enough to allow for as much debris and water capacity
once the vacuum is turned on for the last 100 feet of
cleaning.
Figure 5-1
ok
100 ft
300+ft
200 ft
100 ft
200 ft
300+ft
Summary of Contents for Camel 1200 (Dump Body)
Page 1: ......
Page 2: ......
Page 4: ......
Page 62: ...1 52 Publication 0028607 SAFETY 1...
Page 64: ...2 2 Publication 0028607 PRE OPERATION 2 Figure 2 1 Figure 2 2 1 3 2 5 6 4 7...
Page 106: ...4 18 Publication 0028607 SEWER CLEANING TYPICAL SEQUENCE 4...
Page 118: ...5 12 Publication 0028607 WATER RECYCLING SYSTEM 5...
Page 132: ...6 14 Publication 0028607 LUBRICATION AND MAINTENANCE 6...
Page 156: ...i vi Publication 0028607 IX...
Page 157: ......