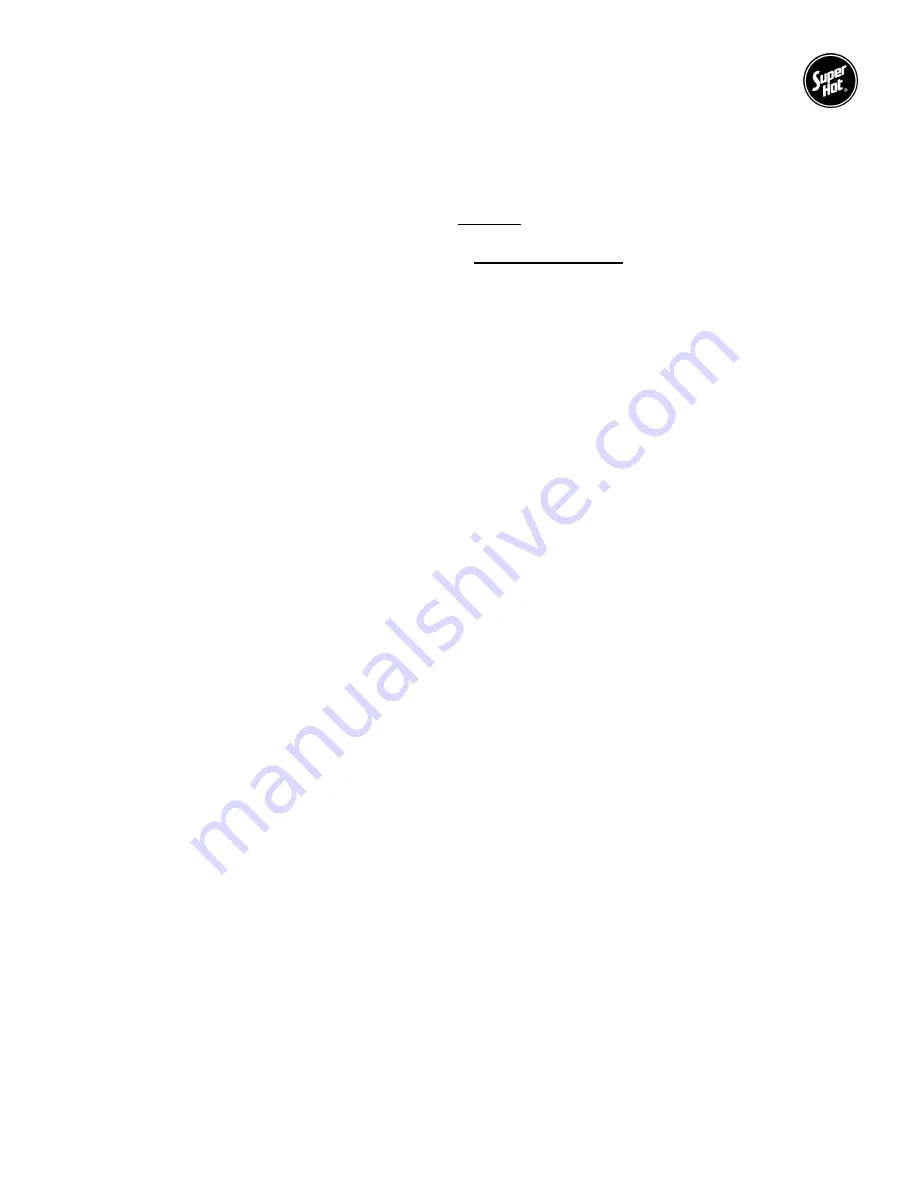
AAA Series Gas Boiler – Installation and Service Manual
7
2.4
GAS SERVICE PIPING
The boiler and its gas connection must be leak tested before placing the boiler in operation. The gas
controls furnished are suitable for a maximum operating gas pressure of 1/2 psi (14 inches water column).
The boiler and its individual shutoff valve must be disconnected from the gas supply piping system during
any pressure testing of that system at test pressures in excess of 1/2 psig (14 inches water column).
The boiler must be isolated from the gas supply piping system by closing its individual manual shutoff
valve during any pressure testing at test pressures equal to or less than 1/2 psig (14 inches water
column).
A manual main shut-off valve should be installed in the gas line outside the boiler jacket and as required in
Section 2.2
. The valve should be readily accessible for turning on and off.
A drip pocket or sediment trap should be installed in the gas supply line upstream of the gas controls and
as close to the boiler as possible (example shown in Figure 7 in
Section 6
).
Some pressure regulators or pressure regulating sections of gas valves are provided with an integral vent
limiter and threaded connection. A bleed or gas relief line should be connected to it and piped to the
outdoors.
The pipe compound used should be resistant to the action of liquefied petroleum gases. Check for gas
leaks in piping before placing the boiler in operation by using a soap and water solution.
DO NOT USE
AN OPEN FLAME.
INSTALLER MUST IDENTIFY EMERGENCY SHUT-OFF DEVICES.
All piping and fittings must be installed as per codes in
Section 2.2
.
2.5
AIR SUPPLY FOR COMBUSTION AND VENTILATION
A sufficient air supply MUST be provided to this boiler. Air openings to the boiler room provide the air for
combustion, flue gas dilution and ventilation and are always required, regardless whether the air is taken
from inside or outside. The air opening size and location (as well as other air supply and venting
considerations) must conform to
Section 2.2
.
The boiler room must never be under a negative pressure. Always provide air openings sized not only to
the dimensions required for the total input of all fuel-fired appliances in the boiler space, but also to handle
the air movement rate of any
exhaust fans
or
air movers
using air from the building or space.
The venting terminations must always be kept clear of obstructions (i.e. snow, ice, etc.). Louvers and
grilles used in the air supply and ventilation system should be kept clear of any dust, dirt, or debris which
will block proper air flow.
2.6
CORROSIVE ATMOSPHERES
If a gas boiler is to be installed near a corrosive or potentially corrosive air supply, the boiler should be
isolated from it and outside air should be supplied as recommended in
Section 2.5
.
Chemical vapors from products containing
chlorine
or
fluorine
must be avoided. Even though these
chemicals may be safe to breathe, corrosive substances can become liberated when passed through a
gas flame. Even at low concentrations, these chemicals can significantly contaminate the air supply and
shorten the life of any gas burning appliance. The following is a list of some of the products which should
be avoided:
•
bleaches and chlorinated cleaning products
•
paints and sprays
•
water softeners (calcium or sodium chloride)
•
leaking refrigeration equipment
•
freon from common aerosol dispensers
These chemicals are especially common near swimming pools, beauty shops, dry cleaning
establishments, laundry areas, workshops, and garages.
The warranty is void when failure is due to
corrosion.
Summary of Contents for AAA-3000 series
Page 28: ...AAA Series Gas Boiler Installation and Service Manual 28 ...
Page 29: ...AAA Series Gas Boiler Installation and Service Manual 29 Wiring Diagrams Section 7 ...
Page 30: ...AAA Series Gas Boiler Installation and Service Manual 30 ...
Page 31: ...AAA Series Gas Boiler Installation and Service Manual 31 ...
Page 34: ...AAA Series Gas Boiler Installation and Service Manual 34 NOTES Section 9 ...
Page 35: ...AAA Series Gas Boiler Installation and Service Manual 35 NOTES Section 9 ...