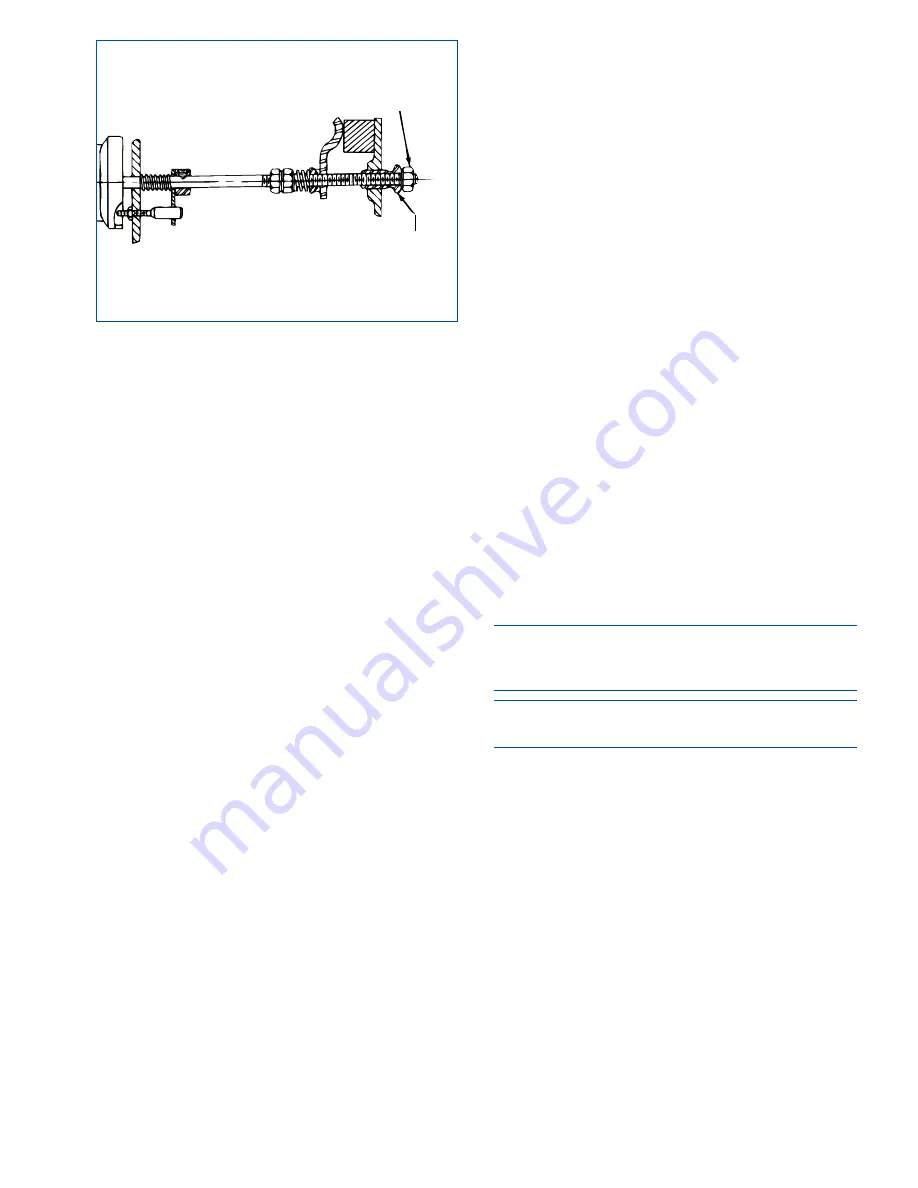
11. Rotate Light Cutting Pressure Control all the
way counterclockwise against stop (to zero).
12. Turn Threaded Sleeve (B) clockwise (as viewed
from rear of machine) until light pressure control
fork will not return to contact collar when it is
pulled away
(refer to Figure 4-5)
.
13. Loosen Locknut (C) on Heavy Cutting Pressure
Control shaft
(see Figure 4-9)
.
14. Rotate Heavy Cutting Pressure Control all the
way counterclockwise against stop (to zero).
15. Turn Threaded Sleeve (D) clockwise (as viewed
from rear of machine) until honing dial needle will
not return to zero when Feed Dial is pushed all the
way in and slowly released.
16. Set Heavy Cutting Pressure Control so that
handle is in line with upper surface of spindle nose
(refer to Figure 4-6)
.
17. Push Feed Dial in as far as you can and release
slowly.
18. While holding Heavy Cutting Pressure Control
in position set in step 21, watch Honing Dial and
turn threaded sleeve D counterclockwise slowly
until honing dial needle moves to between 4 and 5.
If honing dial needle suddenly moves to red line, stop
adjusting threaded sleeve D. Push in on Feed Dial
again and release slowly. If needle stops between
4 and 5, adjustment of threaded sleeve D is correct.
If needle still moves quickly to red line, turn threaded
sleeve D clockwise a small amount and again push
Feed Dial in and release slowly.
Continue adjusting threaded sleeve D until needle
stops between 4 and 5 when Feed Dial is pushed are
released slowly.
19. Tighten locknut C against threaded sleeve D.
20. Recheck threaded sleeve D adjustment by pushing
Feed Dial in as far you can and releasing slowly . . .
honing dial needle should stop between 4 and 5. If
it doesn't, loosen locknut C and repeat step 18.
21. Make sure both pressure controls are turned all
the way counterclockwise against stops (to zero).
22. Push Feed Dial in as far as you can and release
slowly.
23. While holding light cutting pressure control
against stop (at zero) watch honing dial and turn
Threaded Sleeve B slowly counterclockwise until
the needle moves to between 8 and +1
(refer to
Figure 4-8)
.
If needle suddenly moves past 8 toward red line,
stop adjusting Threaded Sleeve B. Push in on Feed
Dial again and release slowly.
If honing dial needle stops between 8 and +1,
adjustment of Threaded Sleeve B is correct. If honing
dial needle still moves quickly past 8 toward red area,
turn Threaded Sleeve B clockwise, a. small amount
and again push Feed, Dial in and release slowly.
Continue adjusting Threaded Sleeve B until needle
stops between 8 and +11 when Feed Dial is pushed
in and released slowly.
24. Tighten Locknut A against Sleeve B. Approximate
adjustment of Light Pressure Control is now complete.
8. Set Heavy Cutting Pressure Control to zero.
9. Set Light Cutting Pressure Control to zero.
10. Check light pressure control fork to make sure it
is seated on shoulder of collar
(refer to Figure 4-5)
.
IMPORTANT
Turn machine ON but do not run spindle while Steps
11 and 12 are performed.
CAUTION
Belt guard must be closed when motor is on.
11. Push Feed Dial in. Slowly release. Honing dial
needle should move toward red line and stop
between 0 and 2, or just barely continue to move.
12. Rotate Light Cutting Pressure Control to 1/2.
Honing dial needle should move to red line.
If everything is okay, continue with step 8.
If not, skip to step 13.
25. Recheck Light Cutting Pressure Control (Sleeve
B) as instructed in steps 8-12.
If the honing dial needle moves quickly to the red
line in Step b.(5). push the Stop button and allow
motor to stop. Open belt guard. Loosen Locknut A
and turn Sleeve B clock-wise a small amount.
Tighten Locknut A against Sleeve B.
Recheck Sleeve B adjustment as necessary using the
procedure in Step (18) above.
21
FIGURE 4-9, Heavy Cutting Pressure Control
LOCKNUT
(C)
THREADED
SLEEVE (D)
Summary of Contents for LBB-1660
Page 8: ...NOTES viii...
Page 34: ...NOTES 26...
Page 38: ...NOTES 30...
Page 40: ...NOTES 32...
Page 44: ...NOTES 36...
Page 45: ...37 APPENDIX E DECLARATION OF CONFORMITY CE PAGE 1 OF 2 SAMPLE CE DOCUMENT...
Page 46: ...38 APPENDIX E DECLARATION OF CONFORMITY CE PAGE 2 OF 2 SAMPLE CE DOCUMENT...