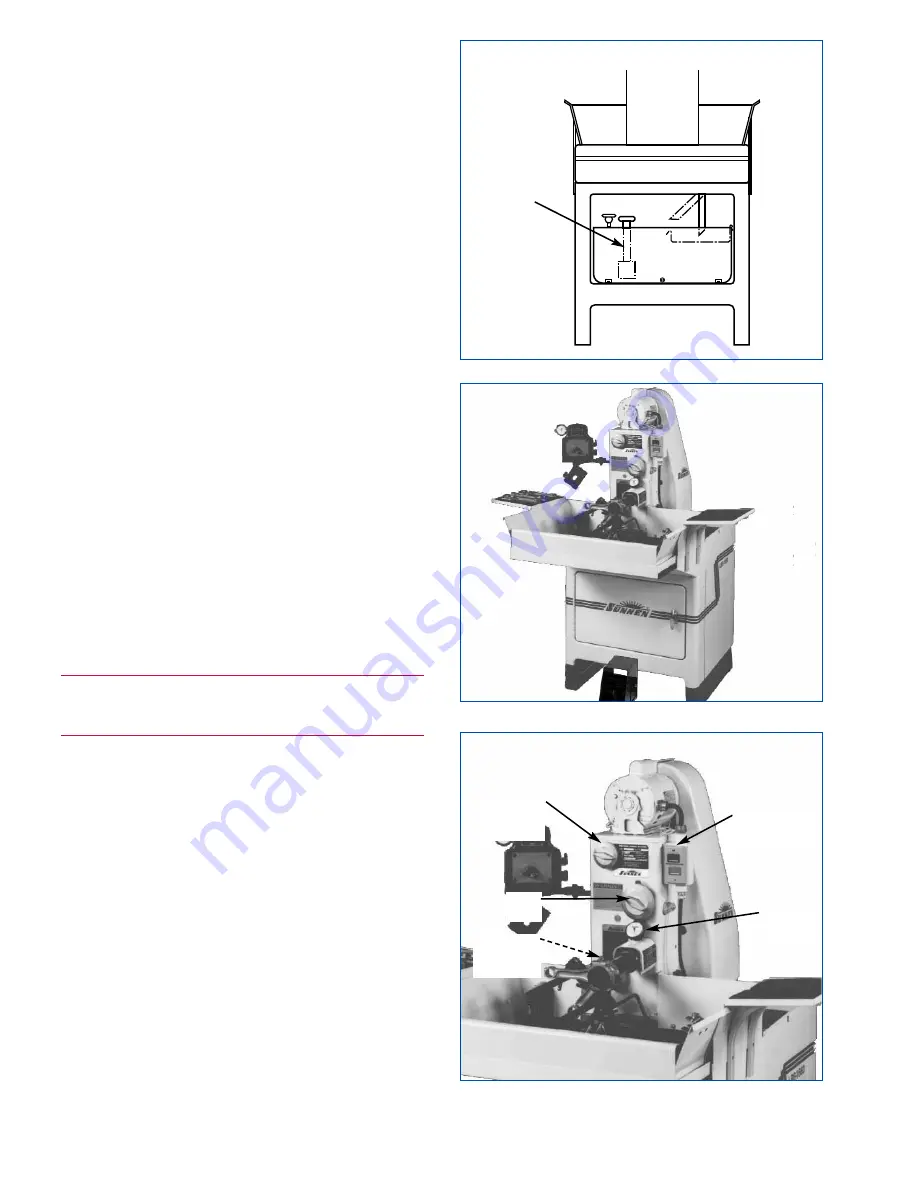
6
Heavy Cutting Pressure Control
Dial is located on
lower left of assembly. It is used to adjust cutting
pressure of honing stone where heavy stock removal
is required. Use in conjunction with Feed Dial and
Honing Dial to ensure maximum efficiency.
Spindle Drive Motor
is located on top of assembly.
It supplies power for honing operation.
4. COOLANT PUMP SYSTEM. Applies coolant to
workpiece and mandrel. Three independently controlled
nozzles are easily positioned to assure an even flow of
coolant through workpiece being honed and over full
length of mandrel. Two nozzles are used to feed
coolant to each end of mandrel. The third may be
used to feed additional coolant to either end of
workpiece, for externally cooling workpiece or for
flushing workpiece before gaging. Coolant Pump
System is located inside top left of machine
(see
Figure 2-4)
. It consists of following components:
Centrifugal Coolant Pump is located inside coolant
reservoir and is driven by spindle motor.
Coolant Flow Control Manifold
is located on left
front of machine. It provides independent regulation
of coolant flow to each
Coolant Nozzle
through
Total Volume Control Valve
and
Individual Coolant
Nozzle Control Valves
. Total volume valve is used
to turn on and off supply of coolant, eliminating
readjustment of individual coolant nozzle control
valve setting.
Coolant Nozzles
attaches to
Coolant Support Arm
located on front of machine in Movable Tray.
Nozzles supply coolant to workpiece and mandrel.
Three independently controlled coolant nozzles are
easily positioned to assure an even flow of coolant
through workpiece and over full length of mandrel.
WARNING
Clean Coolant spills. Coolant can be slick and can
provide a personal fall hazard.
6. ELECTRICAL COMPONENTS Sunnen Honing
Machine is available in 110/230 Volt, single phase,
60 Hz.; or 220//380/440 Volt, 50 Hz, 3 Phase. Its
major components are as follows
(see Figure 2-5)
:
Operator
Controls
are located on right front of Hone
Head Assembly.
Main Power Disconnect is located on left side of
Belt Guard. Electrical power to machine is
controlled by Main Power Disconnect.
7. ACCESSORIES The following items are supplied
as standard equipment with your machine:
Hex Key Wrenches, Metric Wrenches, and T-Wrench.
MAN-700 Diamond Dresser. Used to break glaze on
aluminum oxide and silicon carbide honing stones.
Manual Torque Support. Adjustable support used to
absorb torque from holding fixture (or workpiece)
when honing manually. Manual Torque Support
Arm. Used to hold Manual Torque Support when
manually honing.
FIGURE 2-4, Coolant Pump Assembly
COOLANT
PUMP
FIGURE 2-5, Electrical Components
FIGURE 2-6, Controls
CONTROLS
(START/STOP)
LIGHT
PRESSURE
CONTROL
FEED
DIAL
HEAVY-
PRESSURE
CONTROL
HONING
DIAL
Summary of Contents for LBB-1660
Page 8: ...NOTES viii...
Page 34: ...NOTES 26...
Page 38: ...NOTES 30...
Page 40: ...NOTES 32...
Page 44: ...NOTES 36...
Page 45: ...37 APPENDIX E DECLARATION OF CONFORMITY CE PAGE 1 OF 2 SAMPLE CE DOCUMENT...
Page 46: ...38 APPENDIX E DECLARATION OF CONFORMITY CE PAGE 2 OF 2 SAMPLE CE DOCUMENT...