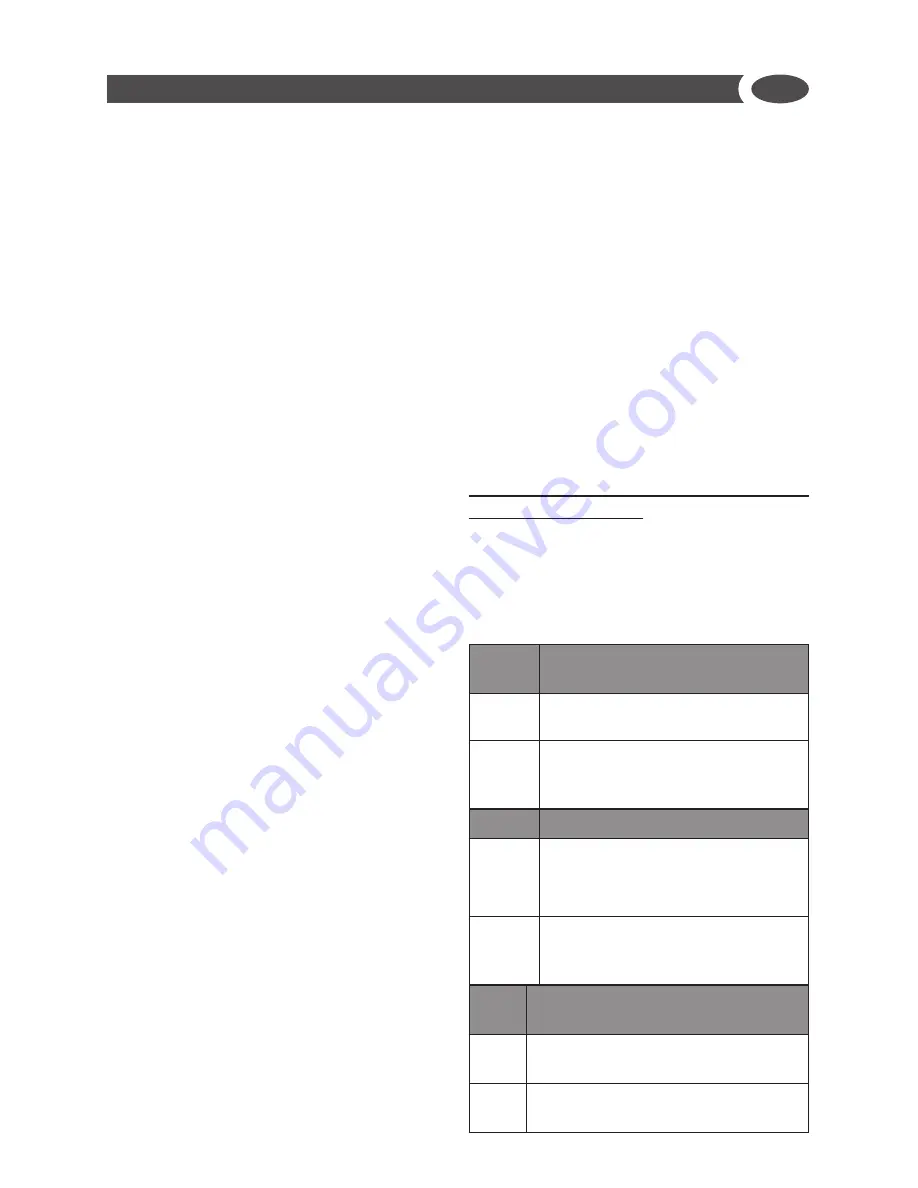
CHECKING THE WATER INTAKE FILTER
Inspect and clean the water intake filter on the inta-
ke union periodically. This is important to prevent
fouling which may impair operation of the pump.
CLEANING THE FUEL FILTER
Check the fuel filter periodically and replace if it has
deteriorated or is excessively dirty.
DESCALING
The descaling procedure must be carried out periodically
with specific products. The interval depends on the hard-
ness of the water. Pour one litre of product for every 15
litres of water into a drum containing at least 30 litres of
water. Disconnect the gun from the high pressure line and
place its free end in the drum, in order to form a closed cir-
cuit, and draw the solution into the machine for at least 10
minutes. The delivery end of the line should discharge into
a canvas or mesh bag so that the scale removed is not re-
turned to the circuit. Then restore the normal connection
and rinse with plenty of cold water. This operation should
be carried out by our after-sales service, since the descal-
ing product may cause wear of components. Comply with
the regulations in force when disposing of the descaling
agent.
Liquid softener tank integrated
(Optional - if included)
The descaling procedure must be carried out pe-
riodically with specific products. The interval de-
pends on the hardness of the water. This opera-
tion should be carried out by our after-sales serv-
ice, since the descaling product may cause wear
of components. Comply with the regulations in
force when disposing of the descaling agent.
•
Fill the softener tank with our products (in
all cases, with non corrosive products). The
dispensing rate is set at a medium value; the
After Sales Services
will be able to adapt the
setting to local conditions.
BOILER CLEANING
•
WARNING:
For all maintenance of the boiler, of the
high pressure pump and of the machine, it is necessary
to address to qualified personnel or to an authorized
assistance center.
The boiler cleaning must be periodically executed every
180 ÷ 200 hours of working proceeding as follows:
- Carefully remove the nozzle holder flange and
the electrodes holder (boiler head).
- Clean with compressed air the nozzle filter and
check the electrodes position.
- Remove the boiler cap, clean the deflector.
- Manually take away the interior cap.
- Unscrewing the locking nuts and take the
boiler coil out.
- Clean the coil by an iron brush.
- Suck the residuums from the boiler.
- Replace every parts doing the operations in the
inverse way.
•
WARNING:
The general checking and combustion
regulation must be periodically executed by specialized
personnel as prescribed by the law.
ELECTRIC DIAGRAM
See illustrations, page 7-8.
WATER DIAGRAM
See illustrations, page 7-8.
TROUBLESHOOTING
Before doing any work on the machine, disconnect
the electricity and water supplies and discharge the
pressure. Proceed systematically to identify Faults
following the chart below; if you are still unable to
eliminate the problem, call in the
Authorized After-
Sales Service
.
Fault
When the main switch is turned on the
machine does not start
Cause
• Plug not properly connected.
• Connection panel fuses are burnt out.
Repair
• Carefully check the plug and the electric
cable.
• Check them and replace them.
Fault
The motor hums but does not start
Cause
• A phase is missing (in three phase
models).
• Lows voltage.
• High pressure pump is blocked.
Repair
• Contact an authorised service centre.
• Contact an authorised service centre.
• Contact an authorised service centre.
Fault
The motor stops suddenly or after a
while
Cause
• The motor-protecting switch is on beCause
of insufficient mains voltage.
Repair
• Check the value of the mains voltage.
• Contact an authorised service centre.
EN
23
Summary of Contents for HYPER L LP
Page 6: ...6 Diesel 4 5 fig L 1 2 3 6 7...
Page 8: ...LKX_LP_1Ph_230V LKX_LP_3Ph_400V 8...
Page 61: ...0 OFF KL 1 13mm 30l min 40 C 1Mpa 15 16 17 18 19 20 21 22 23 24 XZ XX XY XJ EL 61...
Page 64: ...I 50 500 SAE20 30 15W 40 20W 40 11 12 5 10 30 15 10 Optional EL 64...
Page 65: ...180 200 7 8 7 8 EL 65...
Page 66: ...EL 66...
Page 67: ...E 2002 96 27 2003 2002 96 E 12 EL 67...
Page 84: ...01 02 03 04 05a 05b 5 05c 05d 05e 06 30 0 7 RU 84...
Page 85: ...17 18 19 20 21 22 23 24 XX XY XJ 08 09 A S S 2 1 0 A S S stand by 5 11 OFF 12 13 14 16 RU 85...
Page 86: ...1 A H 13 30 40 C 1Mpa I 364 0 03 0 0 H VV F RU 86...
Page 88: ...A S S 1 A A CDEFG OFF 13 1 2 40 C H ON A A RU 88...
Page 89: ...11 30 15 10 Optional 100 C 32 3 749 0183 I I 50 500 SAE 20 30 15W 40 20W 40 RU 89...
Page 90: ...180 200 7 8 7 8 RU 90...
Page 91: ...RU 91...
Page 92: ...12 2002 96 EC 27 2003 RU 92...
Page 108: ...63 OPTIONAL 01 02 03 04 05 05b 5 05c 05d 05e 06 3 07 BG 108...
Page 109: ...21 22 23 24 J 08 09 2 1 0 stand by 5 11 ON OFF 12 13 14 16 17 18 19 20 BG 109...
Page 112: ...CDEFG ON 13 40 1 H ON A A 100 C 32 bar cod 3 749 0183 OPTIONAL I I BG 112...
Page 113: ...30 10 Optional 180 200 14 3 L 50 500 ISO150 80 90 0 45 LP SAE 20 30 20 40 15 40 0 7 15 BG 113...
Page 114: ...7 8 7 8 1 1 1 2 2 2 2 5 0 3 3 4 4 4 5 5 6 6 6 6 6 6 7 7 7 7 7 BG 114...
Page 115: ...8 8 8 9 10 11 12 13 14 14 BG 115...