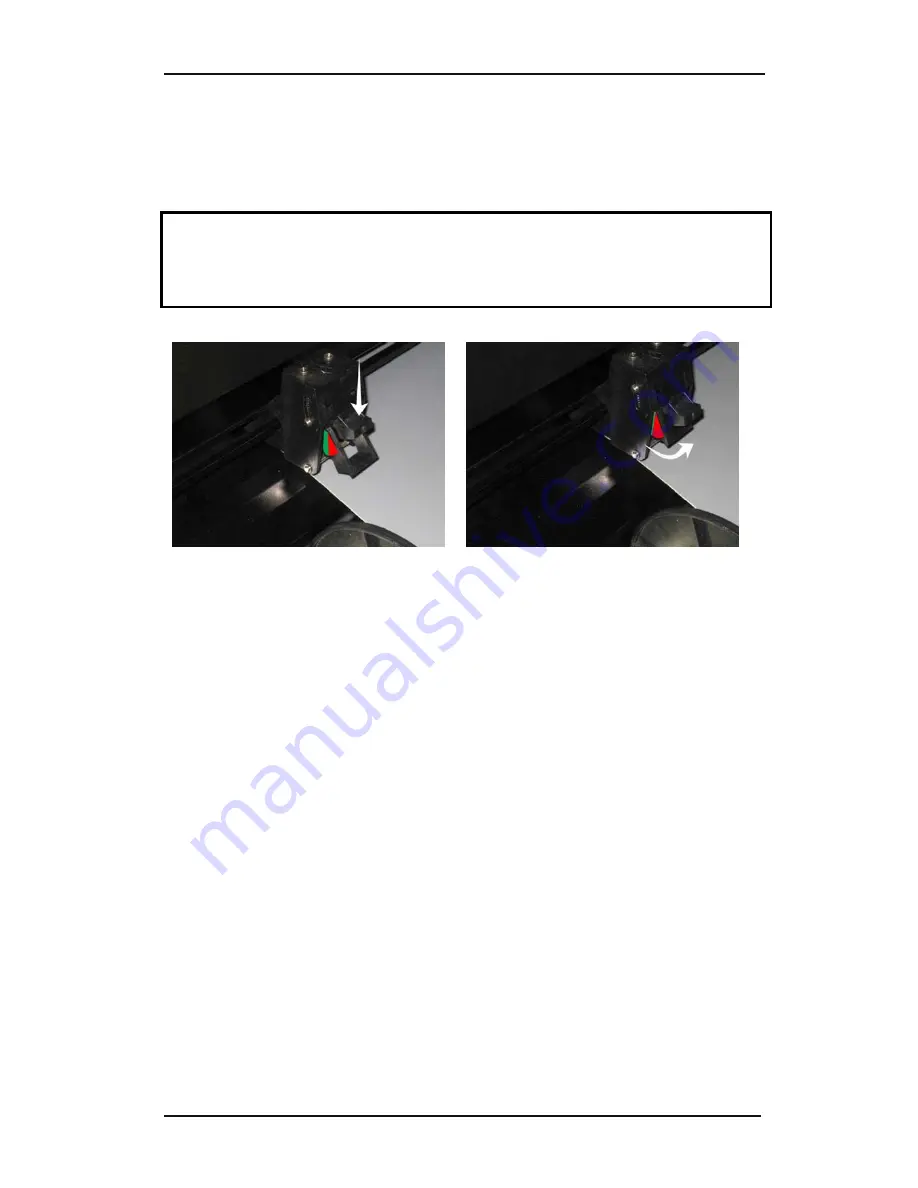
S CLASS™ cutter
User’s Manual
Setup
1-15
1.5.2
Pinch roller pressure setting
The S CLASS™ cutters are equipped with selectable pinch wheel pressure. The
pressure can be set to “standard” or “low.” The pressure can be changed with the
pinch rollers in the “up” position or in the “down” position.
CAUTION:
Always make sure the outer left pinch roller pressure is set the same as the
outer right pinch roller pressure.
There is a label on the assembly that makes it easy for the user to check the selected
pinch roller pressure.
It is best to change pressure when the pinch rollers are in the “up” position.
FIG 1-16
1-16
STANDARD PRESSURE
FIG 1-17
1-17
REDUCED PRESSURE
Standard pressure: the two colors
on the label are clearly visible. The
pressure can be reduced by
pushing on the plastic part as
shown in the picture. If pressed hard
enough, the pinch roller assembly
should click in its new position.
Reduced pressure: only one color
is distinctly visible. The pressure
can be set to “standard” by pulling
the bottom part of the pinch roller
assembly upwards. If pulled far
enough, the pinch roller assembly
should click in its new position.
The S120 and the S160 are equipped with extra pinch rollers to guide wide media.
These pinch rollers can be enabled or disabled by following the same steps used to
change the pressure on the outer pinch rollers.
Summary of Contents for S 75
Page 1: ...User s Manual Rev 05 05...