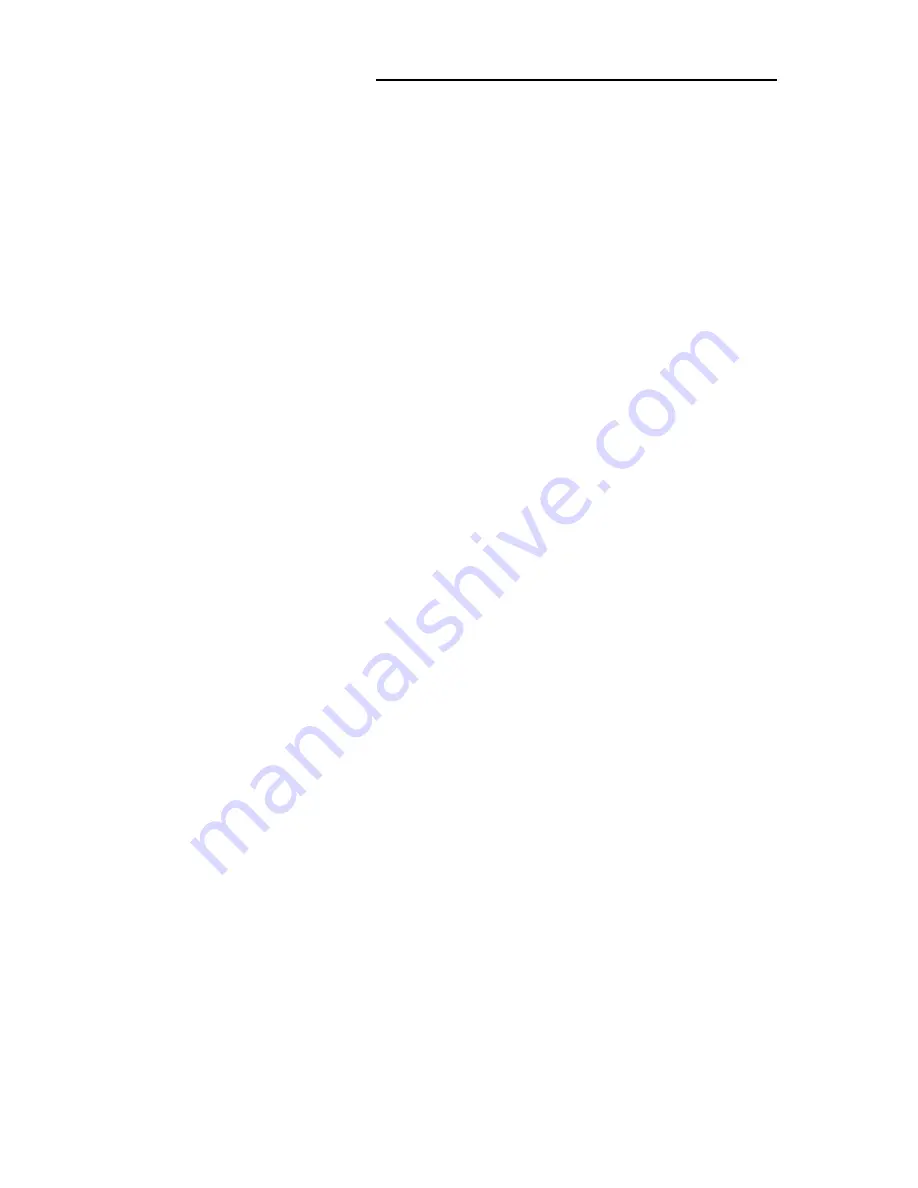
SULLIVAN-PALATEK______________________________
21
6. Once the parameter has been selected, press “enter,” then use the “up” (+) or
“down” (-) keys to change the setting.
7. Press “enter” to effect this change in setting.
8. Press “enter” again and then use the “up” (+) or “down” (-) key to select the next
setting to be changed.
9. Press “enter” and then use the “up” (+) or “down” (-) keys to change the setting.
10. Press “enter” to effect this change in setting.
Once the desired settings have been made, press the “C” key twice (or hold
“reset” for 2 seconds) to return to main menu.
5.4
NORMAL OPERATION
1. Open and lock out main power disconnect.
2. Check lubricoolant level. Refill if necessary.
3. Re-close disconnect switch. Micro processor will illuminate indicating
compressor is ready to start.
4. Start machine by pressing ‘run’ button on micro processor.
5. Fully open service air valve.
6. Observe pressure and temperature. If temperature is incorrect, refer to
SECTION 6.6 – TROUBLE SHOOTING.
5.5 SHUTDOWN
To stop compressor, close service valve, allow sump pressure to fall to 40-45 PSI, then
press stop button on micro processor control.
5.6 STARTS
After a power failure, open and lock out the main disconnect, check all fuses and
breakers. Close disconnect switch and follow Normal Operation start-up procedure.
Following a shutdown caused by either of the protective devices (i.e. temperature or
R.O.P.), open and lock out the main disconnect switch, correct the cause of shutdown,
reset electrical controls, then close the disconnect and follow Normal Operation start-up
procedure.
1. If the overload relay has tripped the motor off, first open and lock out the main power
disconnect, then push the starter overload reset button. Next, check overload relay
to be sure that it is properly sized and correctly adjusted. Note: Never adjust
overload relay higher than indicated by starter manufacturer to match motor
nameplate amperage rating, as an unsafe operating condition will result!
2. Check lubricoolant level. Refill if necessary.
3. Re-close disconnect switch.
4. Start machine by pressing ‘run’ button on micro processor.
5. Fully open service air valve.
6. Observe pressure and temperature displayed by micro processor.
Summary of Contents for 125G
Page 12: ...______________________________SULLIVAN PALATEK 12 CONTROL SCHEMATIC ...
Page 18: ...______________________________SULLIVAN PALATEK 18 4 5b WIRING DIAGRAM Y DELTA START OPTIONAL ...
Page 28: ...______________________________SULLIVAN PALATEK 28 PARTS LISTING ...
Page 31: ...SULLIVAN PALATEK______________________________ 31 DRIVE AND BASE ASSEMBLY ...
Page 32: ...______________________________SULLIVAN PALATEK 32 7 3 DRIVE AND BASE ASSEMBLY PARTS LIST ...
Page 33: ...SULLIVAN PALATEK______________________________ 33 LUBRICATION AND COOLING SYSTEM AIR COOLED ...
Page 37: ...SULLIVAN PALATEK______________________________ 37 LUBRICATION COOLING SYSTEM W C 200 250 ...
Page 38: ...______________________________SULLIVAN PALATEK 38 7 5b LUBRICATION COOLING SYSTEM W C 200 250 ...
Page 39: ...SULLIVAN PALATEK______________________________ 39 INLET AND CAPACITY CONTROL SYSTEM ...
Page 41: ...SULLIVAN PALATEK______________________________ 41 DISCHARGE SYSTEM 125 150 HP ...
Page 43: ...SULLIVAN PALATEK______________________________ 43 DISCHARGE SYSTEM 200 250 HP ...
Page 45: ...SULLIVAN PALATEK______________________________ 45 OPEN COMPRESSOR ELECTRICAL CONTROL PARTS ...
Page 47: ...SULLIVAN PALATEK______________________________ 47 ENCLOSED COMPRESSOR CONTROL PARTS ...
Page 48: ...______________________________SULLIVAN PALATEK 48 7 8b ENCLOSED COMPRESSOR CONTROL PARTS ...
Page 49: ...SULLIVAN PALATEK______________________________ 49 AIR COOLED ENCLOSURE 125 250 ...
Page 50: ...______________________________SULLIVAN PALATEK 50 7 10a AIR COOLED ENCLOSURE 125 150 ...
Page 51: ...SULLIVAN PALATEK______________________________ 51 AIR COOLED ENCLOSURE 200 250 ...
Page 52: ...______________________________SULLIVAN PALATEK 52 7 10b AIR COOLED ENCLOSURE 200 250 ...
Page 53: ...SULLIVAN PALATEK______________________________ 53 WATER COOLED ENCLOSURE ...
Page 54: ...______________________________SULLIVAN PALATEK 54 7 11 WATER COOLED ENCLOSURE ...
Page 56: ...______________________________SULLIVAN PALATEK 56 7 12b DECAL AND IDENTIFICATION ...