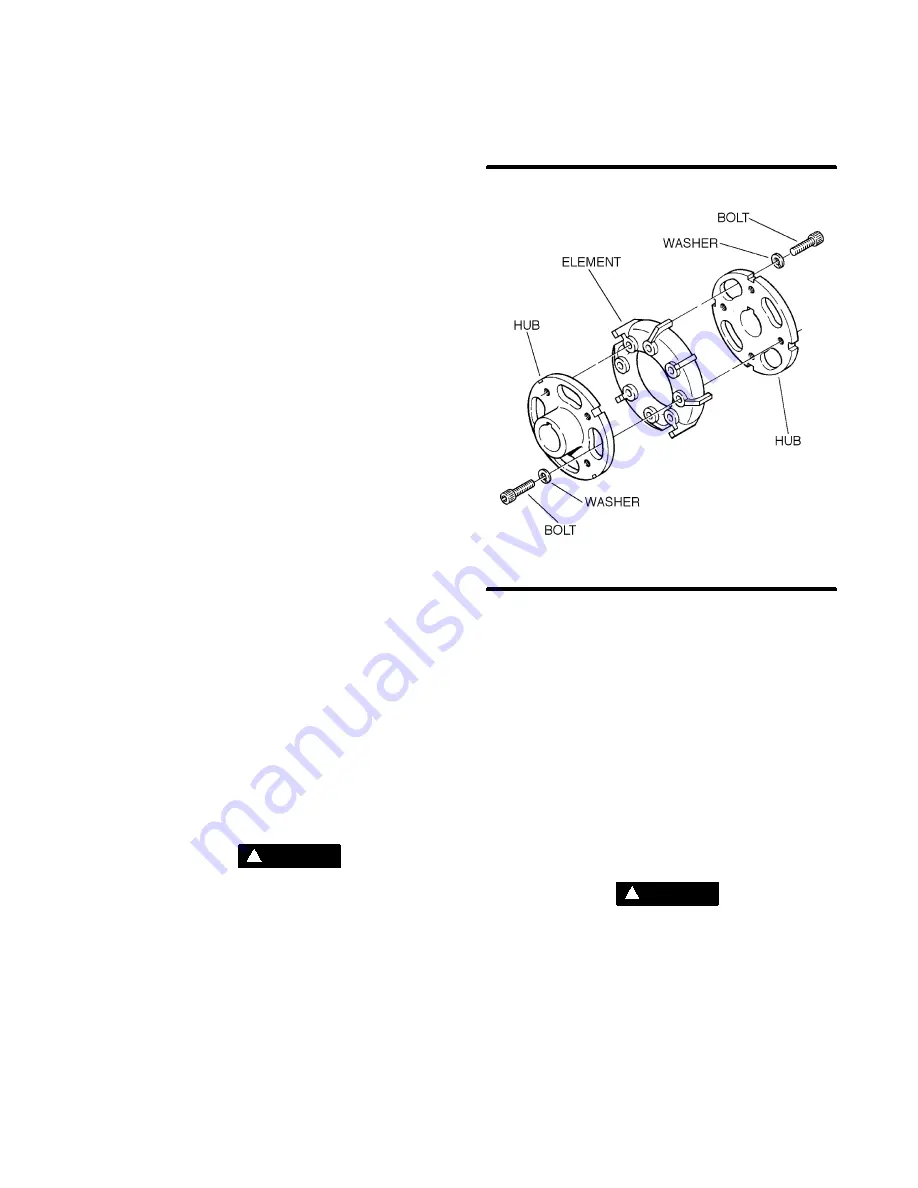
Section 7
MAINTENANCE
39
UNLOAD pressure (110 psig [7.6 bar]). Note that
pressing the pad for over 2 seconds will initiate fast
scrolling of the value being set.
Once the correct value is selected, press the PROG
pad to proceed to the display “PRES DIF P2A. This
value is used to set the LOAD pressure where the
compressor will begin building pressure (10 PSID
[0.7 bar]). This will provide LOAD/UNLOAD opera-
tion at 100 to 110 psig [6.7 to 7.6 bar]). These val-
ues will be entered when the display is returned to
operating mode condition by continuing to press
PROG through the end of the PROGRAMMING
menu or allowing the display to automatically re-
turn to operating mode status after 5 seconds of in-
activity. While scrolling with the PROG pad, all exist-
ing user programmable values will be displayed.
FOR DIFFERENTIAL PRESSURE REGULATOR
ADJUSTMENT:
The differential pressure regulators are adjusted by
loosening the jam nut on the end of the cone
shaped cover of the pressure regulator. When the
jam nut is loose, turn the adjusting screw clockwise
to increase or counterclockwise to decrease the
setting.
Above 100 psig (6.9 bar), the spiral valve regulator
should allow pressure to flow into the chamber of
the spiral valve actuator. The spiral valve should
start to rotate at this time.
At approximately 108 psig (7.5 bar), the Sullicon
regulator should allow pressure to flow into the
control chamber of the Sullicon Control. The Sul-
licon Control level should start to move at this time.
Cycle the Control System several times and re-
check all pressure settings.
DRIVE COUPLING INSTALLATION AND
ALIGNMENT (200, 250 and 300HP/150, 187
and 225KW)
. F o r c o u p l i n g
installation and alignment, the tools required are a
straight edge, a measuring scale, one set of feeler
gauges, a set of standard Allen wrenches and one
set of standard socket wrenches.
WA R N I N G
!
Disconnect all power at source, before attempting
maintenance or adjustments.
For installation and alignment of the drive coupling,
follow the steps explained below.
STEP 1 MOUNT HUBS
--- Mount the motor hub
and the compressor hub onto respective shaft. Po-
sition the hubs to establish the correct gap speci-
. S ec ur e eac h hub with a s etsc r ew.
STEP 2 OFFSET ALIGNMENT
--- Clean any oil,
grease, dirt or paint from coupling faces and the
Figure 7---5 Drive Coupling (200---300HP/150---225KW)
Element P/N 046999
other surfaces of the drive flanges. Rotate shafts so
that a straight edge will rest squarely (or within the
0.010 inch maximum limit shown in Table 1) on both
flanges and at a point 90
_
away. The vertical offset
alignment is adjusted by the addition or removal of
motor mounting shims. Loosen the motor mount-
ing bolts and slide the motor sideways to correct
the horizontal offset.
STEP 3 COUPLING GAP AND ANGULAR ALIGN-
MENT
--- Position the hubs to establish the proper
gap and angular alignment as indicated in Table 1.
To determine the angular misalignment in inches,
measure the maximum space between the hub
flanges and the minimum space 180
_
away, and
then subtract. To adjust the horizontal angular
misalignment, loosen the motor mounting bolts
and adjust the motor position until the angular
alignment is within tolerance.
WA R N I N G
!
DO NOT upset the offset alignment or hub gap
when adjusting motor position.
When within the limits specified in Table 1, tighten
the motor mounting bolts and recheck the offset
and angular alignment. If the vertical angular align-
ment is not within .010 inch tolerance, shim the
front or rear of the motor separately to correct. Re-
check the vertical offset.
STEP 4 INSTALL THE FLEXIBLE ELEMENT
--- Po-
sition the motor and compressor keyways 180
_
Summary of Contents for TS32 Series
Page 2: ......
Page 3: ......
Page 33: ...Section 5 COMPRESSOR SYSTEMS 25 Figure 5 8 Control System 200 250 300HP 150 187 225KW...
Page 34: ...Section 5 COMPRESSOR SYSTEMS 26 Figure 5 8 Control System Diagram 200 250 300HP 150 187 225KW...
Page 35: ...Section 5 COMPRESSOR SYSTEMS 27 Figure 5 9 Control System 400 500 600HP 300 375 450KW...
Page 36: ...Section 5 COMPRESSOR SYSTEMS 28 Figure 5 9 Control System 400 500 600HP 300 375 450KW...
Page 56: ...48 NOTES...
Page 59: ...Section 8 ILLUSTRATIONS AND PARTS LIST 51 NOTES...
Page 62: ...Section 8 ILLUSTRATIONS AND PARTS LIST 54 8 5 MOTOR COMPRESSOR FRAME AND PARTS 400HP 300KW...
Page 66: ...Section 8 ILLUSTRATIONS AND PARTS LIST 58 8 7 AIR INLET SYSTEM 200 300HP 150 225KW...
Page 68: ...Section 8 ILLUSTRATIONS AND PARTS LIST 60 8 8 AIR INLET SYSTEM 400 600HP 300 450KW...
Page 74: ...Section 8 ILLUSTRATIONS AND PARTS LIST 66 8 10 FLUID COOLING SYSTEM 400HP 300KW WATER COOLED...
Page 76: ...Section 8 ILLUSTRATIONS AND PARTS LIST 68 8 10 FLUID COOLING SYSTEM 400HP 300KW WATER COOLED...
Page 126: ...Section 8 ILLUSTRATIONS AND PARTS LIST 118 8 21 SULLICON CONTROL 200 600HP 150 450KW...
Page 128: ...Section 8 ILLUSTRATIONS AND PARTS LIST 120 8 22 COMPRESSOR ACTUATOR 200 600HP 150 450KW...
Page 134: ...Section 8 ILLUSTRATIONS AND PARTS LIST 126 8 24 ENCLOSURE 200 300HP 150 225KW...
Page 136: ...Section 8 ILLUSTRATIONS AND PARTS LIST 128 8 24 ENCLOSURE 200 300HP 150 225KW...
Page 138: ...Section 8 ILLUSTRATIONS AND PARTS LIST 130 8 25 ENCLOSURE 400 600HP 300 450KW...
Page 140: ...Section 8 ILLUSTRATIONS AND PARTS LIST 132 8 25 ENCLOSURE 400 600HP 300 450KW...
Page 142: ...Section 8 ILLUSTRATIONS AND PARTS LIST 134 8 26 RTD PROBES 200 300HP 150 225KW...
Page 144: ...Section 8 ILLUSTRATIONS AND PARTS LIST 136 8 27 RTD PROBES 400 600HP 300 450KW...
Page 146: ...Section 8 ILLUSTRATIONS AND PARTS LIST 138 8 28 AFTERCOOLER 400HP 300KW WATER COOLED...
Page 148: ...Section 8 ILLUSTRATIONS AND PARTS LIST 140 8 28 AFTERCOOLER 400HP 300KW WATER COOLED...
Page 150: ...Section 8 ILLUSTRATIONS AND PARTS LIST 142 8 29 AFTERCOOLER 500 600HP 375 450KW WATER COOLED...
Page 152: ...Section 8 ILLUSTRATIONS AND PARTS LIST 144 8 29 AFTERCOOLER 500 600HP 375 450KW WATER COOLED...
Page 154: ...Section 8 ILLUSTRATIONS AND PARTS LIST 146 8 30 DECAL GROUP...
Page 156: ...Section 8 ILLUSTRATIONS AND PARTS LIST 148 8 30 DECAL GROUP...
Page 158: ...Section 8 ILLUSTRATIONS AND PARTS LIST 150 8 30 DECAL GROUP...
Page 160: ...Section 8 ILLUSTRATIONS AND PARTS LIST 152 8 30 DECAL GROUP...
Page 162: ...Section 8 ILLUSTRATIONS AND PARTS LIST 154 8 31 WIRING DIAGRAM STANDARD FULL VOLTAGE...
Page 163: ...Section 8 ILLUSTRATIONS AND PARTS LIST 155 8 32 WIRING DIAGRAM WYE DELTA...