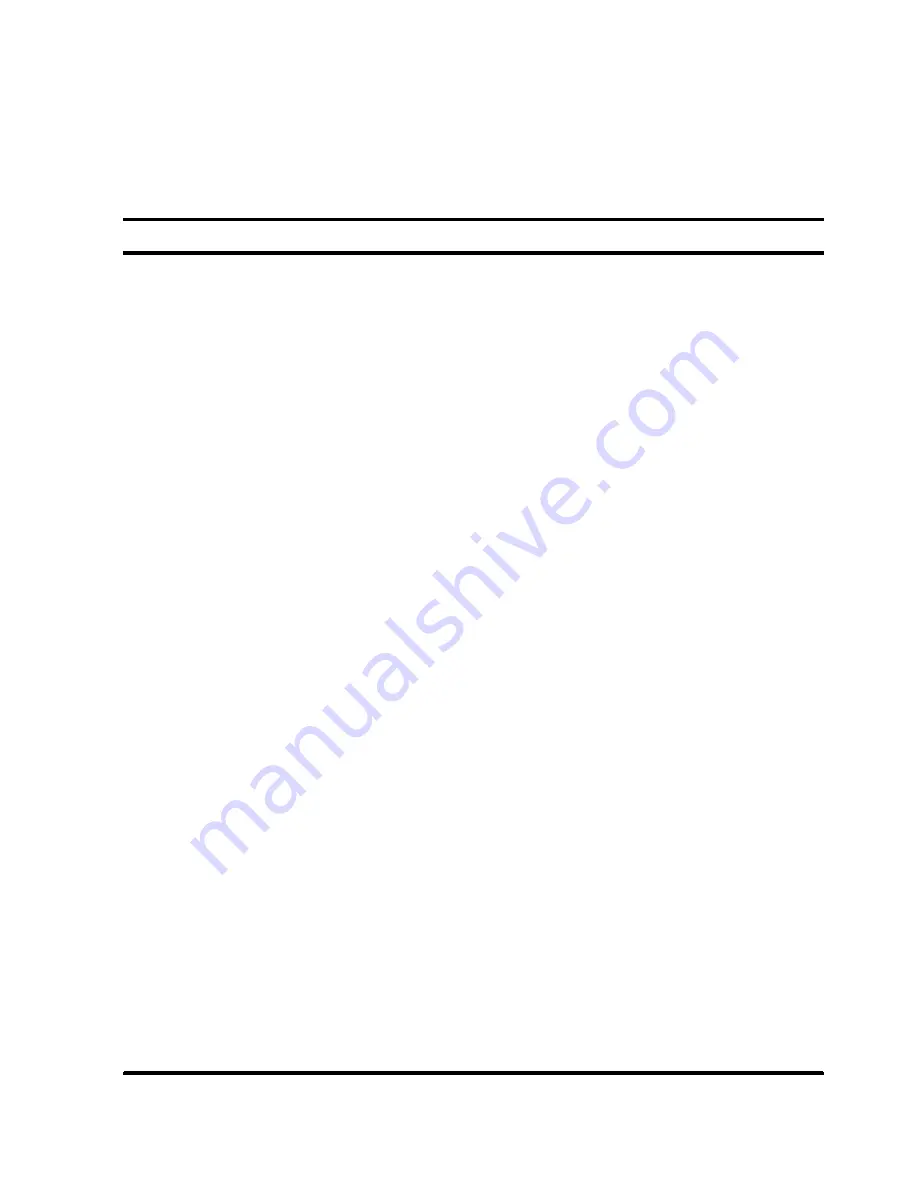
Section 4
SUPERVISOR
13
4.8 SUPERVISOR
I
MICROCONTROLLER PRO-
GRAMMING
Several display and operational functions are user
programmable from the Supervisor keypad. Re-
peatedly pressing the “PROG” pad will scroll the
message display through the various program-
mable parameters. The cursor pad (
Y
) is used to
change parameter values. A built---in timed delay
feature returns the message display to operation
mode after 5 seconds of inactivity.
PARAMETER (IN SEQUENTIAL ORDER)
OPERATION
LANGUAGE
Press the cursor pad for 2 seconds to change to next
language for the message display. Languages in or-
der are: French, German, Italian, Spanish and Eng-
lish.
AUTOMATIC/MANUAL
The controller default state is AUTOMATIC operation.
If line pressure is adequate and/or the sump pressure
is greater than 5 to 10 psig (0.3 to 0.7 bar), pressing
the ON/OFF pad will put the control in STANDBY
mode until line pressure drops to the programmed
differential value and the sump pressure is low
enough to permit a START. AUTOMATIC mode pro-
vides a timed STOP with automatic restart operation.
Automatic restart after power failure is also included
in AUTOMATIC mode.
MANUAL mode ignores the line pressure permissive
of AUTOMATIC and starts the compressor with ON/
OFF as long as the minimum sump pressure and oth-
er fault conditions are satisfied. The compressor is
only stopped manually with no time stop and no auto-
matic restart after power failure.
PRESSURE UNITS
Selects bar or psig; use cursor key to select. 1 bar =
14.5 psig.
TEMPERATURE UNITS
_
C OR
_
F; use cursor key to select.
MAXIMUM PRESSURE P2A
Use the cursor key to set the OFF LOAD pressure set-
ting. Depressing the cursor pad for more than 2 se-
conds will initiate a fast scrolling mode to quickly
reach the desired setpoint for all programmable set-
points. A wraparound feature (on all functions) re-
turns the value to its lowest limit if scrolling exceeds
the high limit. Typically set for 110 psig (7.6 bar).
PRESSURE DIFFERENTIAL P2A
Selects the ON LOAD setting by subtracting the differ-
ential from P2A. Normally set for 10 psig (0.7 bar).
MAXIMUM PRESSURE P2B
Same as P2A, but provides a second OFF LOAD set-
ting for base/load operation.
PRESSURE DIFFERENTIAL P2B
Same as P2A, but provides a second ON LOAD set-
ting for base/load operation.
UNLOAD TIME
Adjusts timed stop function if compressor is running
unloaded for 0 to 60 minutes.
WYE TO DELTA TIME
Adjusts transition timer for Wye---Delta starters from 0
to 30 seconds. ON LOAD function is delayed by the
value of Wye to Delta time. A separate relay contact is
provided with this function. It is recommended that a
transition time of 8 seconds not be exceeded.
DRAIN TIME AND DRAIN INTERVAL
A timed contact is furnished to control a condensate
(OPTIONAL) removal solenoid valve. Both drain dura-
tion time (1 to 10 seconds) and time internal between
drains (1 to 10 minutes) may be set from these
modes.
Summary of Contents for TS32 Series
Page 2: ......
Page 3: ......
Page 33: ...Section 5 COMPRESSOR SYSTEMS 25 Figure 5 8 Control System 200 250 300HP 150 187 225KW...
Page 34: ...Section 5 COMPRESSOR SYSTEMS 26 Figure 5 8 Control System Diagram 200 250 300HP 150 187 225KW...
Page 35: ...Section 5 COMPRESSOR SYSTEMS 27 Figure 5 9 Control System 400 500 600HP 300 375 450KW...
Page 36: ...Section 5 COMPRESSOR SYSTEMS 28 Figure 5 9 Control System 400 500 600HP 300 375 450KW...
Page 56: ...48 NOTES...
Page 59: ...Section 8 ILLUSTRATIONS AND PARTS LIST 51 NOTES...
Page 62: ...Section 8 ILLUSTRATIONS AND PARTS LIST 54 8 5 MOTOR COMPRESSOR FRAME AND PARTS 400HP 300KW...
Page 66: ...Section 8 ILLUSTRATIONS AND PARTS LIST 58 8 7 AIR INLET SYSTEM 200 300HP 150 225KW...
Page 68: ...Section 8 ILLUSTRATIONS AND PARTS LIST 60 8 8 AIR INLET SYSTEM 400 600HP 300 450KW...
Page 74: ...Section 8 ILLUSTRATIONS AND PARTS LIST 66 8 10 FLUID COOLING SYSTEM 400HP 300KW WATER COOLED...
Page 76: ...Section 8 ILLUSTRATIONS AND PARTS LIST 68 8 10 FLUID COOLING SYSTEM 400HP 300KW WATER COOLED...
Page 126: ...Section 8 ILLUSTRATIONS AND PARTS LIST 118 8 21 SULLICON CONTROL 200 600HP 150 450KW...
Page 128: ...Section 8 ILLUSTRATIONS AND PARTS LIST 120 8 22 COMPRESSOR ACTUATOR 200 600HP 150 450KW...
Page 134: ...Section 8 ILLUSTRATIONS AND PARTS LIST 126 8 24 ENCLOSURE 200 300HP 150 225KW...
Page 136: ...Section 8 ILLUSTRATIONS AND PARTS LIST 128 8 24 ENCLOSURE 200 300HP 150 225KW...
Page 138: ...Section 8 ILLUSTRATIONS AND PARTS LIST 130 8 25 ENCLOSURE 400 600HP 300 450KW...
Page 140: ...Section 8 ILLUSTRATIONS AND PARTS LIST 132 8 25 ENCLOSURE 400 600HP 300 450KW...
Page 142: ...Section 8 ILLUSTRATIONS AND PARTS LIST 134 8 26 RTD PROBES 200 300HP 150 225KW...
Page 144: ...Section 8 ILLUSTRATIONS AND PARTS LIST 136 8 27 RTD PROBES 400 600HP 300 450KW...
Page 146: ...Section 8 ILLUSTRATIONS AND PARTS LIST 138 8 28 AFTERCOOLER 400HP 300KW WATER COOLED...
Page 148: ...Section 8 ILLUSTRATIONS AND PARTS LIST 140 8 28 AFTERCOOLER 400HP 300KW WATER COOLED...
Page 150: ...Section 8 ILLUSTRATIONS AND PARTS LIST 142 8 29 AFTERCOOLER 500 600HP 375 450KW WATER COOLED...
Page 152: ...Section 8 ILLUSTRATIONS AND PARTS LIST 144 8 29 AFTERCOOLER 500 600HP 375 450KW WATER COOLED...
Page 154: ...Section 8 ILLUSTRATIONS AND PARTS LIST 146 8 30 DECAL GROUP...
Page 156: ...Section 8 ILLUSTRATIONS AND PARTS LIST 148 8 30 DECAL GROUP...
Page 158: ...Section 8 ILLUSTRATIONS AND PARTS LIST 150 8 30 DECAL GROUP...
Page 160: ...Section 8 ILLUSTRATIONS AND PARTS LIST 152 8 30 DECAL GROUP...
Page 162: ...Section 8 ILLUSTRATIONS AND PARTS LIST 154 8 31 WIRING DIAGRAM STANDARD FULL VOLTAGE...
Page 163: ...Section 8 ILLUSTRATIONS AND PARTS LIST 155 8 32 WIRING DIAGRAM WYE DELTA...