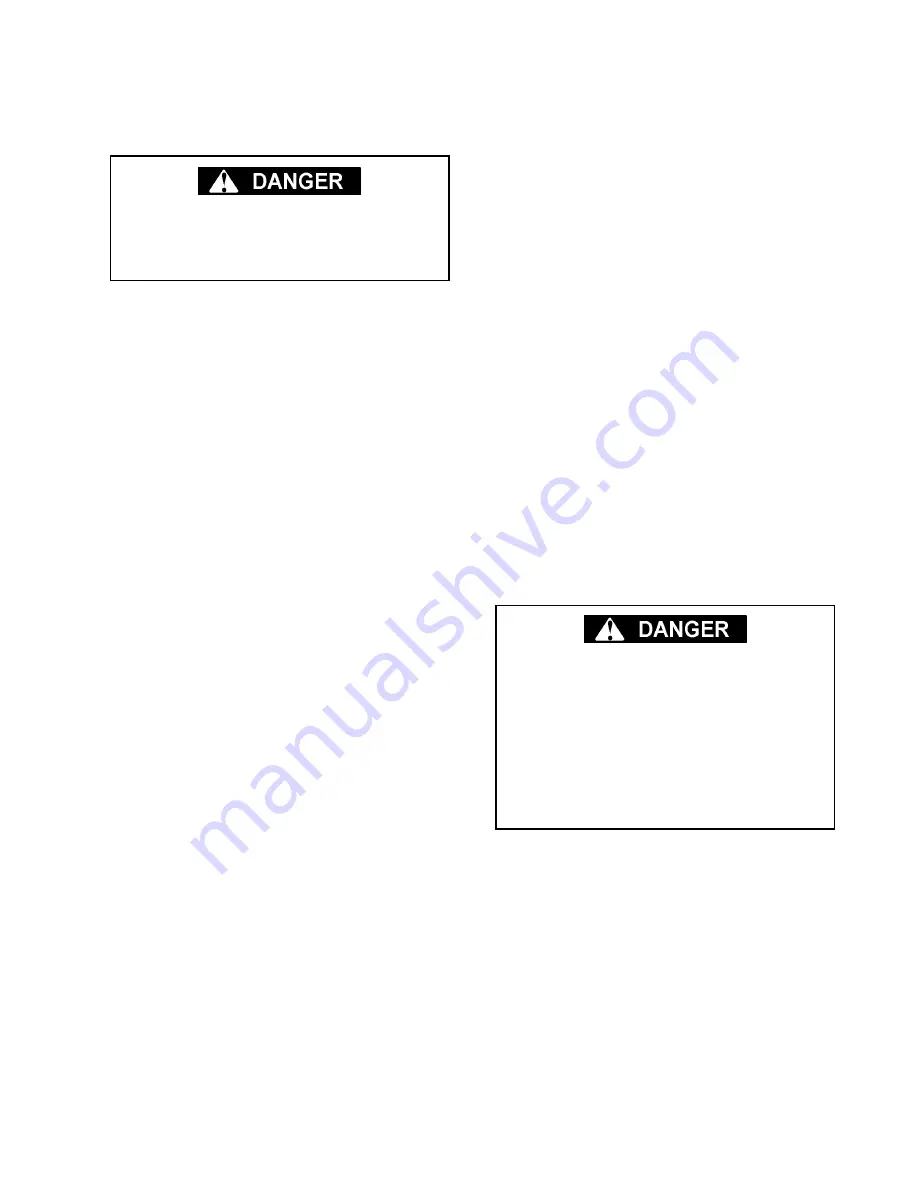
Section 1
SAFETY
3
OSHA Standards 29 CFR 1910 and/or any applica-
ble Federal, State or Local codes or regulations.
B. DO NOT
use air line anti-icer systems in air lines
supplying respirators or other breathing air utiliza-
tion equipment and
DO NOT
discharge air from
these systems into unventilated or other confined
areas.
C.
Operate the compressor only in open or ade-
quately ventilated areas.
D.
Locate the compressor or provide a remote inlet
so that it is not likely to ingest exhaust fumes or
other toxic, noxious or corrosive fumes or sub-
stances.
E.
Coolants and lubricants used in this compressor
are typical of the industry. Care should be taken to
avoid accidental ingestion and/or skin contact. In
the event of ingestion, seek medical treatment
promptly. Wash with soap and water in the event of
skin contact. Consult Material Safety Data Sheet for
information pertaining to fluid of fill.
F.
Wear goggles or a full face shield when adding
antifreeze compound to air line anti-icer systems.
G.
If air line anti-icer system antifreeze compound
enters the eyes or if fumes irritate the eyes, they
should be washed with large quantities of clean
water for fifteen minutes. A physician, preferably an
eye specialist, should be contacted immediately.
H. DO NOT
store air line anti-icer system antifreeze
compound in confined areas.
I.
The antifreeze compound used in air line
antifreeze systems contains methanol and is toxic,
harmful or fatal if swallowed. Avoid contact with the
skin or eyes and avoid breathing the fumes. If swal-
lowed, induce vomiting by administering a table-
spoon of salt, in each glass of clean, warm water
until vomit is clear, then administer two teaspoons
of baking soda in a glass of clean water. Have
patient lay down and cover eyes to exclude light.
Call a physician immediately.
1.8 ELECTRICAL SHOCK
A.
This compressor should be installed and main-
tained in full compliance with all applicable Federal,
State and Local codes, standards and regulations,
including those of the National Electrical Code, and
also including those relative to equipment ground-
ing conductors, and only by personnel that are
trained, qualified and delegated to do so.
B.
Keep all parts of the body and any hand-held
tools or other conductive objects away from
exposed live parts of electrical system. Maintain dry
footing, stand on insulating surfaces and
DO NOT
contact any other portion of the compressor when
making adjustments or repairs to exposed live parts
of the electrical system. Make all such adjustments
or repairs with one hand only, so as to minimize the
possibility of creating a current path through the
heart.
C.
Attempt repairs in clean, dry and well lighted and
ventilated areas only.
D. DO NOT
leave the compressor unattended with
open electrical enclosures. If necessary to do so,
then disconnect, lock out and tag all power at
source so others will not inadvertently restore
power.
E.
Disconnect, lock out, and tag all power at source
prior to attempting repairs or adjustments to rotating
machinery and prior to handling any ungrounded
conductors.
1.9 LIFTING
A.
If the compressor is provided with a lifting bail,
then lift by the bail provided. If no bail is provided,
then lift by sling. Compressors to be air-lifted by hel-
icopter must not be supported by the lifting bail but
by slings instead. In any event, lift and/or handle
only in full compliance with OSHA standards 29
CFR 1910 subpart N and/or any applicable Federal,
State, and Local codes, standards and regulations.
B.
Inspect points of attachment for cracked welds
and for cracked, bent, corroded or otherwise
degraded members and for loose bolts or nuts prior
to lifting.
Death or serious injury can result from inhaling
compressed air without using proper safety
equipment. See OSHA standards and/or any
applicable Federal, State, and Local codes, stan-
dards and regulations on safety equipment.
All field equipment must be tested for electro-
static fields prior to servincing or making contact
with the machine using the following or equiva-
lent test equipment:
• 90-600 VAC : Volt detector such as Fluke
Model 1AC-A
• 600-7000 VAC : Voltage detector such as
Fluke Networks Model C9970
It is the responsibility of each organization to
provide/arrange trainng for all their associates
expected to test for electrostatic fields.
Summary of Contents for LS20T 1100 CFM
Page 18: ...Section 2 DESCRIPTION 12 Figure 2 3B Control System Diagram START...
Page 19: ...Section 2 DESCRIPTION 13 Figure 2 3C Control System Diagram MODULATION...
Page 20: ...Section 2 DESCRIPTION 14 Figure 2 3D Control System Diagram FULL LOAD...
Page 21: ...Section 2 DESCRIPTION 15 Figure 2 3E Control System Diagram UNLOAD...
Page 44: ...NOTES 38...
Page 104: ...Section 9 ILLUSTRATIONS AND PARTS LIST 98 02250146 367R00 9 19 CONTROL START SYSTEM...
Page 106: ...Section 9 ILLUSTRATIONS AND PARTS LIST 100 02250146 367R00 9 19 CONTROL START SYSTEM...
Page 108: ...Section 9 ILLUSTRATIONS AND PARTS LIST 102 02250138 633R00 9 20 CONTROL PANEL...
Page 110: ...Section 9 ILLUSTRATIONS AND PARTS LIST 104 02250139 119R01 9 21 ENCLOSURE...
Page 112: ...Section 9 ILLUSTRATIONS AND PARTS LIST 106 02250139 119R01 9 21 ENCLOSURE...
Page 114: ...Section 9 ILLUSTRATIONS AND PARTS LIST 108 9 22 DECAL GROUP...
Page 116: ...Section 9 ILLUSTRATIONS AND PARTS LIST 110 9 22 DECAL GROUP...
Page 118: ...Section 9 ILLUSTRATIONS AND PARTS LIST 112 9 22 DECAL GROUP...
Page 120: ...Section 9 ILLUSTRATIONS AND PARTS LIST 114 9 23 DECAL LOCATIONS OPEN AIR COOLED...
Page 122: ...Section 9 ILLUSTRATIONS AND PARTS LIST 116 9 24 DECAL LOCATIONS OPEN WATER COOLED...
Page 124: ...Section 9 ILLUSTRATIONS AND PARTS LIST 118 9 25 DECAL LOCATIONS REMOTE COOLER...
Page 126: ...Section 9 ILLUSTRATIONS AND PARTS LIST 120 9 26 DECAL LOCATIONS CONTROL BOX...
Page 128: ...Section 9 ILLUSTRATIONS AND PARTS LIST 122 9 27 ENCLOSURE DECALS...
Page 145: ...NOTES 139...