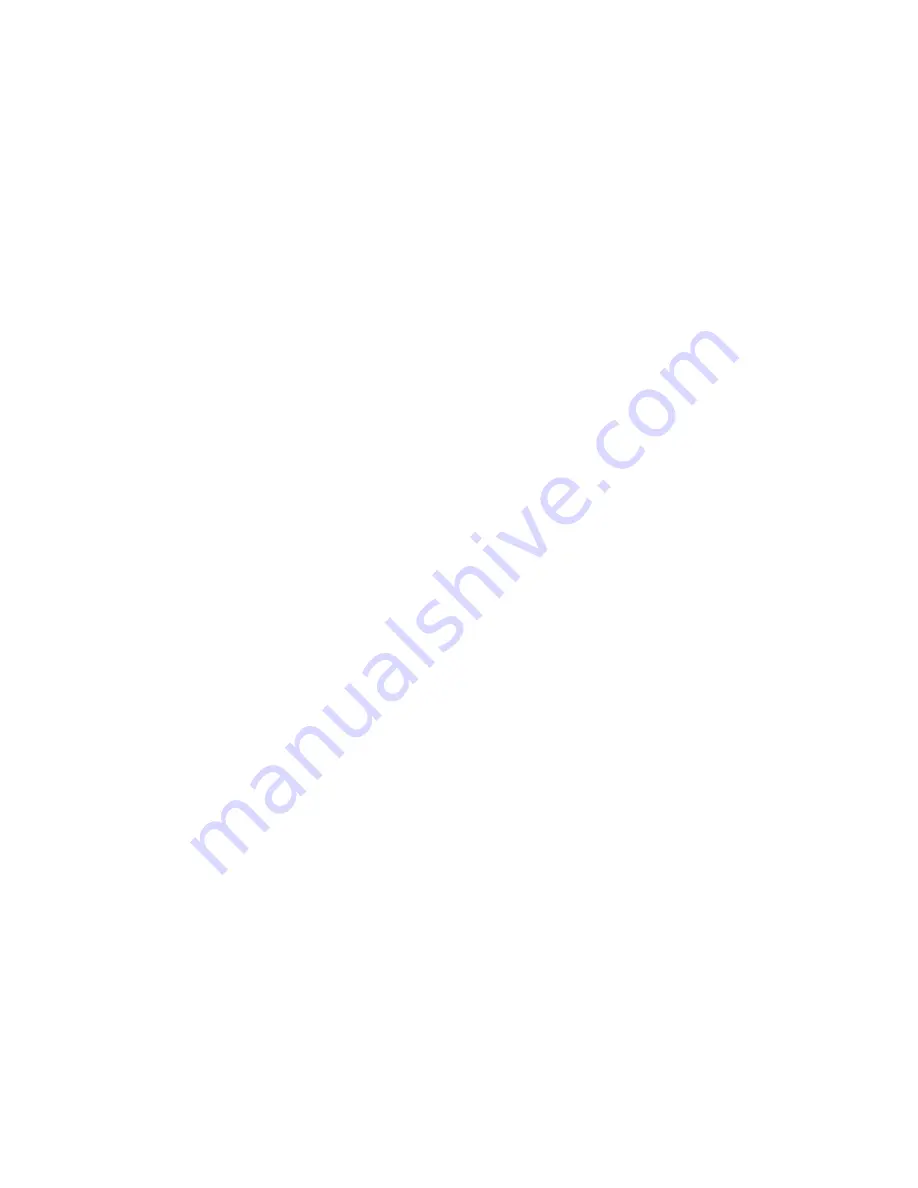
Section 2
DESCRIPTION
10
UNLOAD MODE - EXCESS OF 360 PSIG (24.8
BAR)
As the required air is reduce, the discharge pres-
sure and line pressure rise above the 360 psig (24.8
bar), the Supervisor activates the unload solenoid
valve which in turn pressurizes the blowdown valve.
This opens the blowdown valve, which allows dis-
charge air to flow back to the compressor inlet.
Since the inlet poppet valve is fully closed, the air
pressure from the sump tank will be relieved
through the blowdown valve, which will reduce the
sump pressure. Some of the outgoing air will flow
directly into the compressor inlet to avoid cavitation
during this time of blowdown. As the sump pres-
sure drops, motor power consumption is also
reduced. The unload pressure regulator is set to
maintain the unload pressure at a designated value,
between 140 and 175 psig (9.6 to 12 bar). At this
time, the compressor is in the unload mode.
When the line pressure drops back to the load point
(cut-in pressure) of the pressure transducer, usual-
ly 350 psig (24.1 bar), the compressor will change
state back to the modulating mode as discussed
earlier. This cycle will repeat itself, maintaining the
demand required on the system line supply.
SHUTDOWN MODE
When the compressor is shut down based on a
manual shutdown, a safety shutdown or an auto-
matic shutdown from the Supervisor touch pad, the
unload solenoid valve is de-energized allowing air
to flow through the check valve and into the poppet
valve keeping the inlet poppet valve closed. This
also opens the blowdown valve to allow com-
pressed air to vent back above inlet poppet valve
through the inlet filter. The control lines are proper-
ly sized and routed to allow the compressed air to
relieve to atmosphere rather than below the inlet
poppet valve.
If the compressor Supervisor Controller is in the
automatic mode, the compressor will shut down
after running unloaded for a specific amount of
time. The reverse also holds true, if the system line
pressure requires additional compressed air, the
compressor will start automatically to satisfy this
demand.
Summary of Contents for LS20T 1100 CFM
Page 18: ...Section 2 DESCRIPTION 12 Figure 2 3B Control System Diagram START...
Page 19: ...Section 2 DESCRIPTION 13 Figure 2 3C Control System Diagram MODULATION...
Page 20: ...Section 2 DESCRIPTION 14 Figure 2 3D Control System Diagram FULL LOAD...
Page 21: ...Section 2 DESCRIPTION 15 Figure 2 3E Control System Diagram UNLOAD...
Page 44: ...NOTES 38...
Page 104: ...Section 9 ILLUSTRATIONS AND PARTS LIST 98 02250146 367R00 9 19 CONTROL START SYSTEM...
Page 106: ...Section 9 ILLUSTRATIONS AND PARTS LIST 100 02250146 367R00 9 19 CONTROL START SYSTEM...
Page 108: ...Section 9 ILLUSTRATIONS AND PARTS LIST 102 02250138 633R00 9 20 CONTROL PANEL...
Page 110: ...Section 9 ILLUSTRATIONS AND PARTS LIST 104 02250139 119R01 9 21 ENCLOSURE...
Page 112: ...Section 9 ILLUSTRATIONS AND PARTS LIST 106 02250139 119R01 9 21 ENCLOSURE...
Page 114: ...Section 9 ILLUSTRATIONS AND PARTS LIST 108 9 22 DECAL GROUP...
Page 116: ...Section 9 ILLUSTRATIONS AND PARTS LIST 110 9 22 DECAL GROUP...
Page 118: ...Section 9 ILLUSTRATIONS AND PARTS LIST 112 9 22 DECAL GROUP...
Page 120: ...Section 9 ILLUSTRATIONS AND PARTS LIST 114 9 23 DECAL LOCATIONS OPEN AIR COOLED...
Page 122: ...Section 9 ILLUSTRATIONS AND PARTS LIST 116 9 24 DECAL LOCATIONS OPEN WATER COOLED...
Page 124: ...Section 9 ILLUSTRATIONS AND PARTS LIST 118 9 25 DECAL LOCATIONS REMOTE COOLER...
Page 126: ...Section 9 ILLUSTRATIONS AND PARTS LIST 120 9 26 DECAL LOCATIONS CONTROL BOX...
Page 128: ...Section 9 ILLUSTRATIONS AND PARTS LIST 122 9 27 ENCLOSURE DECALS...
Page 145: ...NOTES 139...