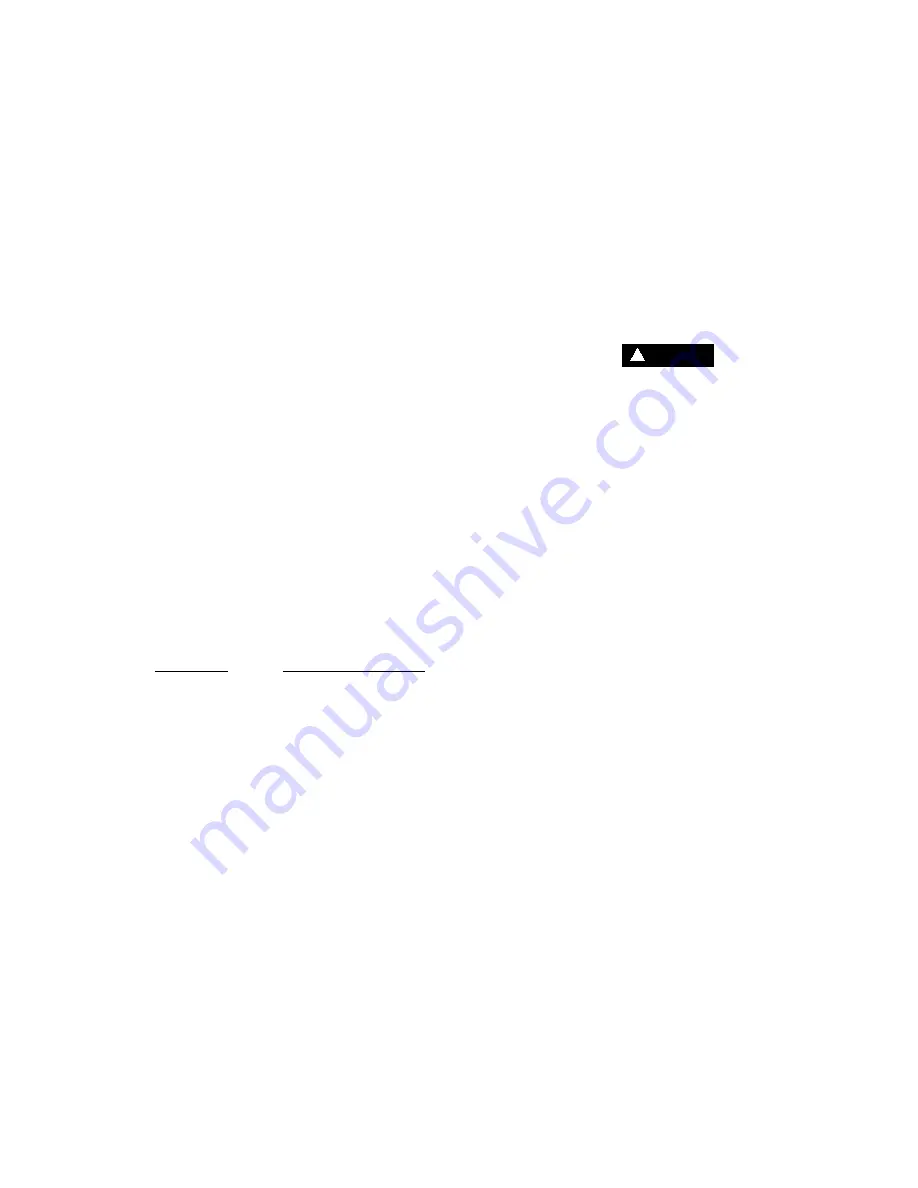
Section 4
INSTALLATION
22
4.4 FLUID PIPING (AIR---COOLED ONLY)
To allow depressurization of the cooling package
and connecting piping between the compressor
and the cooling package upon shutdown of the
compressor, a 1/2 in./13mm depressurization line
must be installed between the top of the fluid cooler
and the sump tank connection, which is located on
the fluid supply and return line connection bracket.
This line must be maintained at a higher level than
the supply and return piping for the fluid cooler.
The supply and return piping for the fluid cooler
must be adequately sized to prevent excessive
pressure drop. The total pressure drop in the sup-
ply and return piping and associated fittings and
valves shall not exceed 10 psig (0.7 bar). If the pres-
sure drop is excessive, a pump may be installed.
Consult the Sullair Service Department for recom-
mendations.
It is recommended that shutoff valves be installed
in the supply and return piping to facilitate com-
pressor components maintenance.
Because of the variability in installations, the fluid
necessary to fill the supply and return piping for the
fluid cooler is not part of the standard scope of sup-
ply for the compressor. The fluid necessary to fill the
piping may be ordered from the nearest Sullair rep-
resentative or the representative from whom the
compressor was purchased. To assist in determin-
ing the amount of fluid necessary to fill the piping,
the following chart may be used.
PIPE SIZE
GALLONS OF FLUID
PER FOOT OF PIPE
2”
.1635
2 1/2”
.2555
3”
.368
4”
.6542
6”
1.4719
4.5 COUPLING ALIGNMENT CHECK
In preparation for the factory test, the coupling sup-
plied with your compressor is properly aligned for
operation. However, due to shipping and handling,
it is necessary to recheck the coupling alignment.
Refer to Coupling Alignment procedure explained
in the Maintenance section of this manual.
4.6 FLUID LEVEL CHECK
Your air compressor is also supplied with the
proper amount of fluid. However, it is necessary to
check the fluid level at installation. The level is
checked by looking at the sight glass located on
the sump. If the sump is properly filled, the coolant
level should fill 1/2 of the sight glass when the com-
pressor is shutdown.
4.7 ELECTRICAL PREPARATION
Interior electrical wiring is performed at the factory.
Required customer wiring is minimal, but should
be done by a qualified electrician in compliance
with any applicable regional or local electrical code
concerning isolation switches, fuse disconnects,
etc. Sullair provides a wiring diagram for use by the
installer.
DAN GER
!
Lethal shock hazard inside.
Disconnect all power at source before opening or
servicing starter or control panel.
1. Check incoming voltage. Be sure that the incom-
ing voltage is the same voltage that the com-
pressor was wired for.
2. Check starter and overload heater sizes (see
electrical parts in Parts Manual).
3. Check all electrical connections for tightness.
4. “DRY RUN” the electrical controls by discon-
necting the three (3) motor leads from the
starter. Pull out the EMERGENCY STOP button
on the control panel. Depress the PROG pad
twice to get to AUTOMATIC/MANUAL mode se-
lection and use the cursor pad to change to
MANUAL mode.
5. Reconnect the three (3) motor leads and jog the
motor for a direction of rotation check, as ex-
4.8 MOTOR ROTATION DIRECTION CHECK
After the electrical wiring has been done, it is nec-
essary to check the direction of the motor rotation.
With the control system in MANUAL mode, press
the ON/OFF pad twice in succession to bump start
the compressor. When looking at the motor from
the end opposite the compressor unit, the shaft
should
be
turning
counterclockwise
for
200HP/150KW (direct drive) packages and clock-
wise for 250 --- 350HP/150 --- 261KW (gear drive)
packages. If the motor shaft is not turning in the
proper direction, disconnect the power to the
starter and exchange any two of the three power in-
put leads, then re---check rotation. A “Direction of
Rotation” decal is located on the coupling guard
between the motor and compressor to show
proper motor/compressor rotation.
Summary of Contents for LS-25S
Page 12: ...Section 2 DESCRIPTION 7 Figure 2 3 Compressor Piping and nstrument Diagram...
Page 16: ...Section 2 DESCRIPTION 11 Figure 2 5A Control System Diagram Start Full Load...
Page 17: ...Section 2 DESCRIPTION 12 Figure 2 5B Control System Diagram Modulation Unload...
Page 49: ...Section 7 ILLUSTRATIONS AND PARTS LIST 44 7 4 COMPRESSOR AIR INTAKE SYSTEM...
Page 71: ...Section 7 ILLUSTRATIONS AND PARTS LIST 66 7 10 COMPRESSOR DISCHARGE SYSTEM...
Page 73: ...Section 7 ILLUSTRATIONS AND PARTS LIST 68 7 10 COMPRESSOR DISCHARGE SYSTEM...
Page 79: ...Section 7 ILLUSTRATIONS AND PARTS LIST 74 7 12 COMPRESSOR ACTUATOR...
Page 81: ...Section 7 ILLUSTRATIONS AND PARTS LIST 76 7 13 ELECTRO PNEUMATIC CONTROL SYSTEM...
Page 83: ...Section 7 ILLUSTRATIONS AND PARTS LIST 78 7 13 ELECTRO PNEUMATIC CONTROL SYSTEM...
Page 85: ...Section 7 ILLUSTRATIONS AND PARTS LIST 80 7 14 ENCLOSURE...
Page 87: ...Section 7 ILLUSTRATIONS AND PARTS LIST 82 7 14 ENCLOSURE...
Page 89: ...Section 7 ILLUSTRATIONS AND PARTS LIST 84 7 15 UNIT TUBING...
Page 91: ...Section 7 ILLUSTRATIONS AND PARTS LIST 86 7 16 DECAL GROUP 1 2 3 4 5 6 7 8 9 10...
Page 95: ...Section 7 ILLUSTRATIONS AND PARTS LIST 90 7 16 DECAL GROUP 21 22 23 24 25...
Page 97: ...Section 7 ILLUSTRATIONS AND PARTS LIST 92 7 16 DECAL GROUP 26 28 29 30 31...
Page 102: ...Section 7 ILLUSTRATIONS AND PARTS LIST 97 7 20 WIRING DIAGRAM...
Page 103: ...Section 7 ILLUSTRATIONS AND PARTS LIST 98 7 21 WIRING DIAGRAM WYE DELTA...