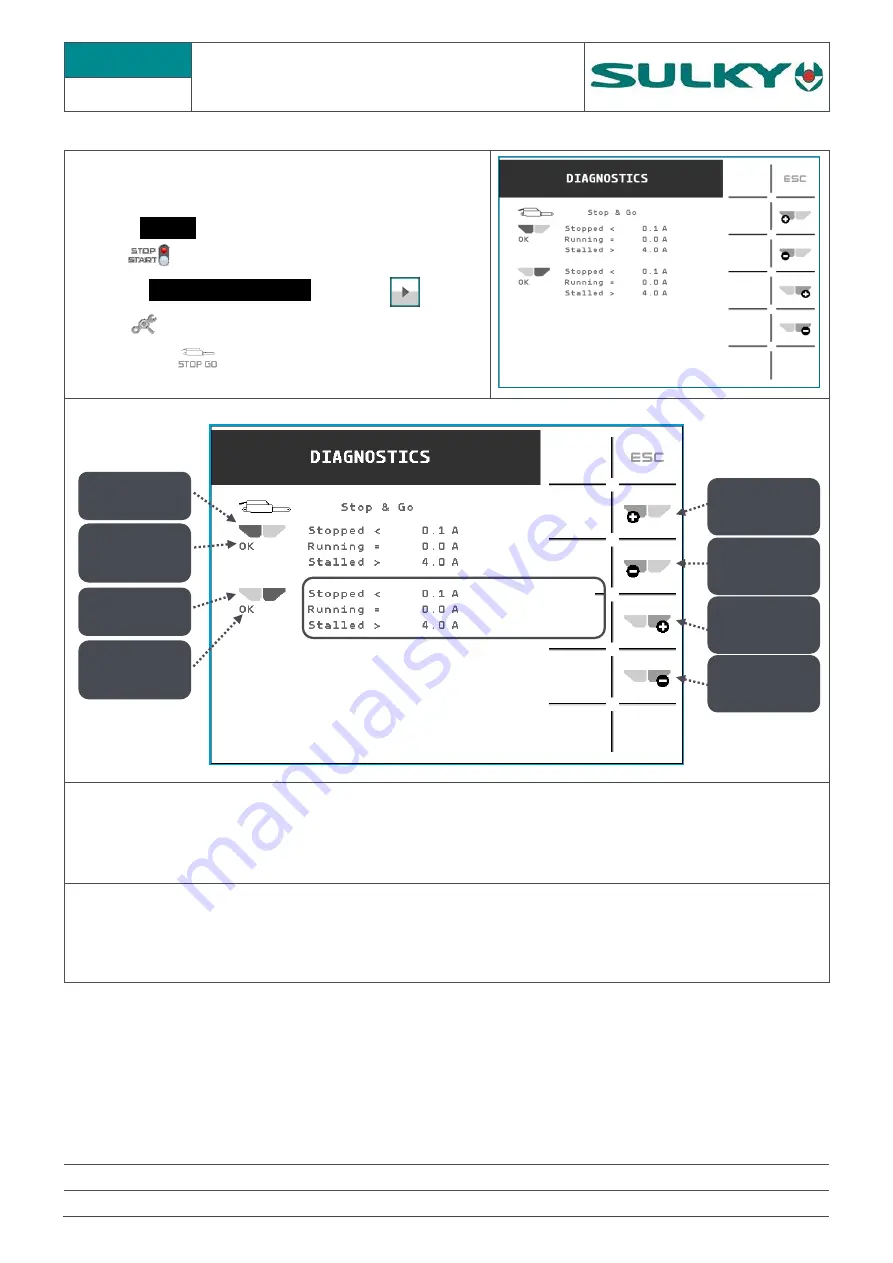
DX - ISOBUS
S
TOP
&
G
O ACTUATORS
D3.2
N
AME
:
T
RAINING
D
EPARTMENT
D
ATE
:
2019.09
P
AGE
:
27/55
R
ÉFÉRENCE
:
T
ECHNICIAN
O
PERATING
M
ANUAL
DX
ISOBUS
I
ND
01
3.
Diagnostics on the console :
From the
HOME
menu, make sure that the shutters are
closed
Access the
ADVANCED SETTINGS
menu with
Select
Diagnostics
And press the
key
To check an actuator, perform an extension and a retraction of the rod. An electricity consumption of between
0.1
and
0.4 A
should be seen.
If there is a fault, the screen displays
Blocked
4.
Electrical control :
Using a direct current power supply, create a +/- or -/+ supply on the red and blue wires, the rod will
extend or retract.
Right Stop & Go
actuator
Left Stop & Go
actuator
Actuator status
Ok/Run
/Blocked
Actuator status
Ok/Run
/Blocked
Min. alarm threshold
I measured
Max. alarm threshold
Left actuator
extension
control
Right actuator
extension
control
Left actuator
retraction
control
Right actuator
retraction
control