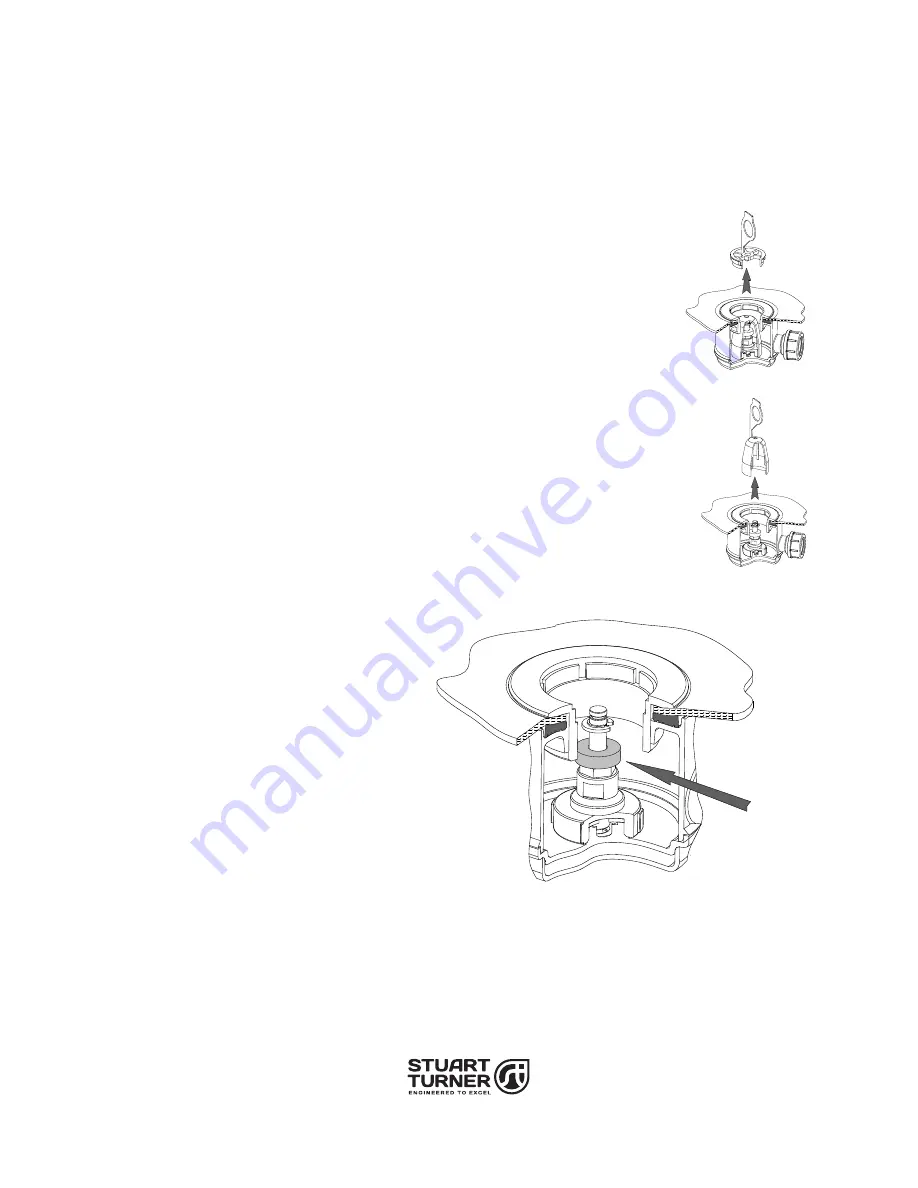
ROUTINE MAINTENANCE
REGULAR MAINTENANCE AND CLEANING IS REQUIRED AS FOLLOWS
STUART TURNER GULLIES – CLEANING PROCEDURE
IT IS RECOMMENDED THAT THIS PROCEDURE SHOULD BE CARRIED OUT AT LEAST EVERY 3 MONTHS.
HOWEVER, MORE FREQUENT MAINTENANCE MAY BE REQUIRED DEPENDING ON USAGE.
Note: This procedure covers all Stuart Turner Gullies – images used for reference only
1. Using ‘Hook’ provided remove central Grill from Gully, clean the Grill and rinse with
fresh water (Fig 11).
2. Using ‘Hook’ provided remove Sensor Cover from Gully, clean the Cover and rinse
with clean water (Fig 12).
3. Remove all debris from Gully and clean around the Sensor switch, taking particular
care around the Sensor Switch Float to ensure no damage occurs (Fig 13). Flush
with clean water
4. Ensure the Sensor Switch Float is free to move up / down on the Shaft
5. If the Sensor Switch Float is stuck / not freely moving, clean any detriment from the
Shaft ensuring no damage to the Shaft or Float occurs. If scale is present this can
be cleaned off using a NON ACID based descalent. Flush with clean water
6. Re-assembly is the reverse of the instructions above
7. Once re-assembled flush the Gully with clean water and check Pump System is
operating
correctly
8. If the Sensor Switch is damaged or not working please refer to the full Shower Tray
Pump Assembly instruction sheet for how to replace this part.
Issue No. 0315/2-01
Pt. No. 19633
Fig. 11
Fig. 12
Fig. 13
Sensor Switch Float
Stuart Turner Ltd, Henley-on-Thames, Oxfordshire RG9 2AD ENGLAND
Tel: +44 (0) 1491 572655, Fax: +44 (0) 1491 573704
[email protected] www.stuart-turner.co.uk
Summary of Contents for Wasteflo
Page 14: ...14 NOTES...
Page 15: ...15 NOTES...