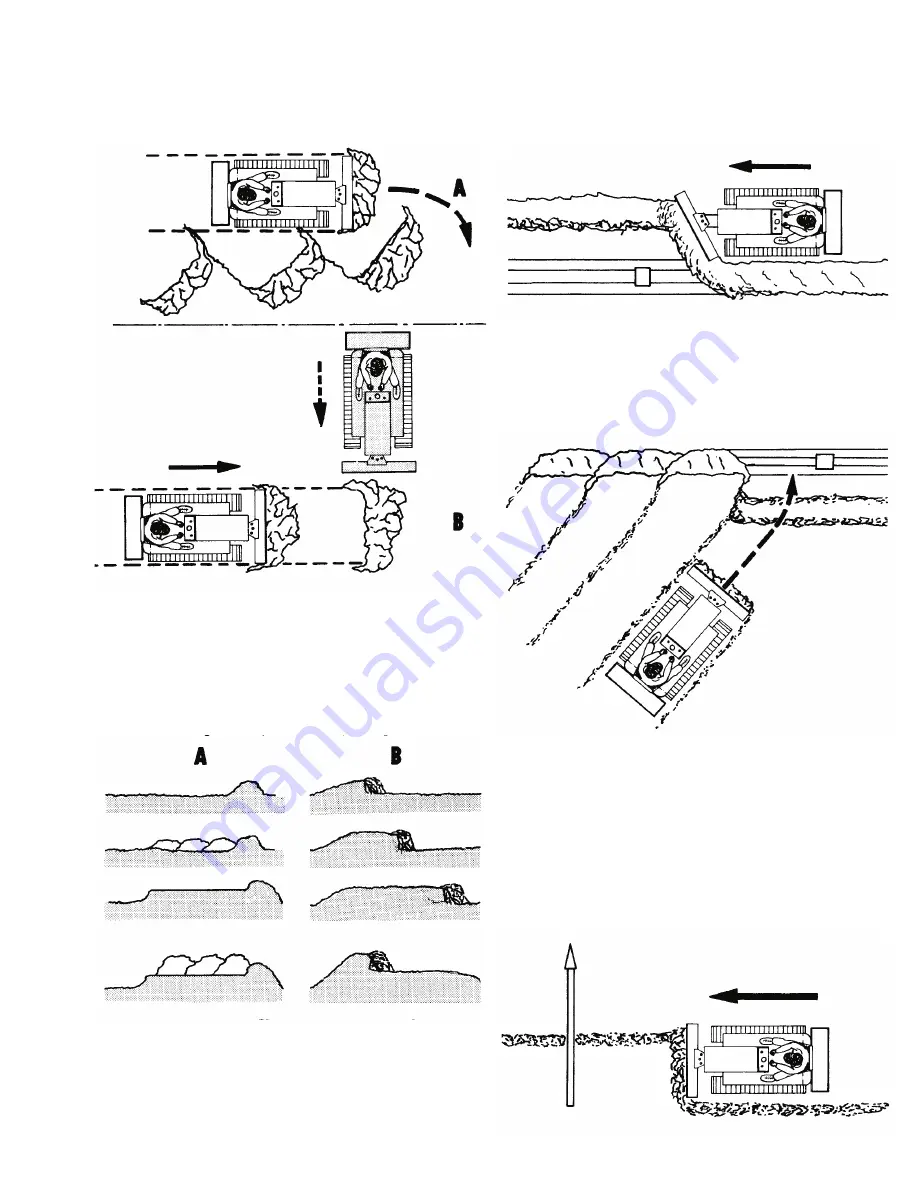
EARTH MOVING
When stripping soil from a road or driveway, either
push it forward and angle it to the side (A) or push it
forward, then perpendicularly push it to the side (B).
Dirt can be piled by dropping successive loads
together, then leveling this material and repeating the
process at a higher plane (A). In the alternative, loads
can be dumped in the opposite direction, creating the new
plateau while pushing loads forward (B).
Both methods will work. When working in heavy
growth or particularly hard soils, plow or rip the area prior
to dozing.
BACKFILLING
Angling blade bulldozers are excellent for backfilling
ditches as they can drift material into the trench while
maintaining forward motion.
With straight blade dozers, approach at an angle and
end up each pass by swinging into the structure or culvert
for smooth, fast results.
FINISH DOZING
Side slopes can be finished with a dozer by starting
at the top and traveling parallel to the right-of-way. Earth
from each pass will fall to the lower side of the blade and
form a windrow. This material is then picked up on
succeeding passes filling up irregularities in terrain. Don’t
allow blade corner to dig as the slope will steepen beyond
job specifications.
44