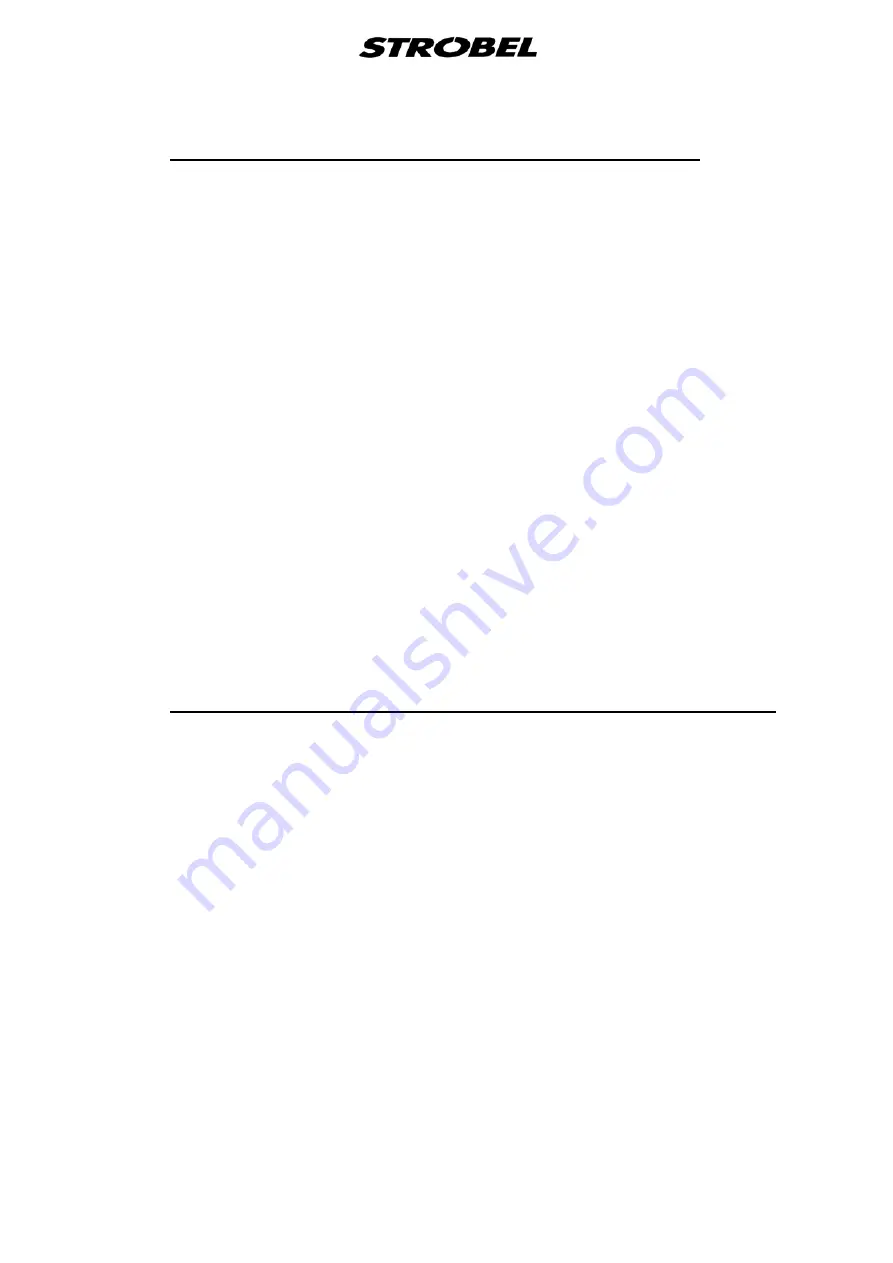
24
MA_310D-R_3100D-R_A16-3_181015_en
3.9.2
Fitting is carried out in reverse order.
However, for accurate adjustment the following points must be observed:
Fitting and adjusting the plunger (Fig. 11 and Fig. 13)
a)
The straight pin (3) (Fig. 11) must engage in the groove of the plunger
sleeve.
b)
Turn stitch depth regulation button (1) (Fig. 13) to the right onto the stop
(highest position).
c)
Turn plunger adjusting screw (2) (Fig. 11) so far into the plunger that the
needle is lifted from the plunger by 0.2 – 0.3 mm when the two-edge
surface of the plunger adjusting screw engages in the groove of the screw
for the plunger regulation (1) (Fig. 11).
d)
The plunger reaches its highest position when the needle point is approx.
4 mm before the centre of the plunger.
The plunger remains stationary until the needle point has crossed it by
5 mm. This value is set by the position of the slide support (5) (Fig. 11),
care must be taken that no double lift occurs, the slide support must not
move above the upper dead point (±0.01 mm tolerance). It is drilled on the
screw, that is, the first grub screw in rotary direction has a point.
e)
Adjustment of the plunger pressure at the works: the screw for the plunger
regulation is flush with the plunger guide (4) (Fig. 11).
By turning the plunger adjusting screw, including the screw for the plunger
regulation, to the right - more plunger pressure, turning to the left - less
plunger pressure.
3.9.3
The plunger regulation must be adjusted on the plunger screw in such a way,
that the pressure generated by the pressure spring (2) (
Adjusting the plunger regulation (Fig. 11, Fig. 12 and Fig. 13)
Fig. 12) in axial
direction is always taken up from the crown rim (4) (Fig. 12) located at the right
end via the adjusting ring (5) (Fig. 12). Between shim(1) (Fig. 12) and slide (3)
(Fig. 12) must be approx. 0.1 mm of air. (Fig. 12)
The bolt with thread (2) (Fig. 13) must be limited with the hexagon screw (5)
(Fig. 13), the hexagon nut (3) and the regulating button (1) (Fig. 13) in such a
way, that the slide (3) (Fig. 12) is adjustable in its crank radius
(= x in Fig. 11) by 13 – 16 mm.
The pressure spring (2) (Fig. 12) must not be pressed together during this to
such an extent that the threads lie on top of each other.
This could result in locking and twisting the slide.
Summary of Contents for 3100D-R
Page 4: ......
Page 8: ...4 MA_310D R_3100D R_A16 3_181015_en...
Page 25: ...21 MA_310D R_3100D R_A16 3_181015_en Fig 9...
Page 31: ...27 MA_310D R_3100D R_A16 3_181015_en Fig 14...
Page 42: ......