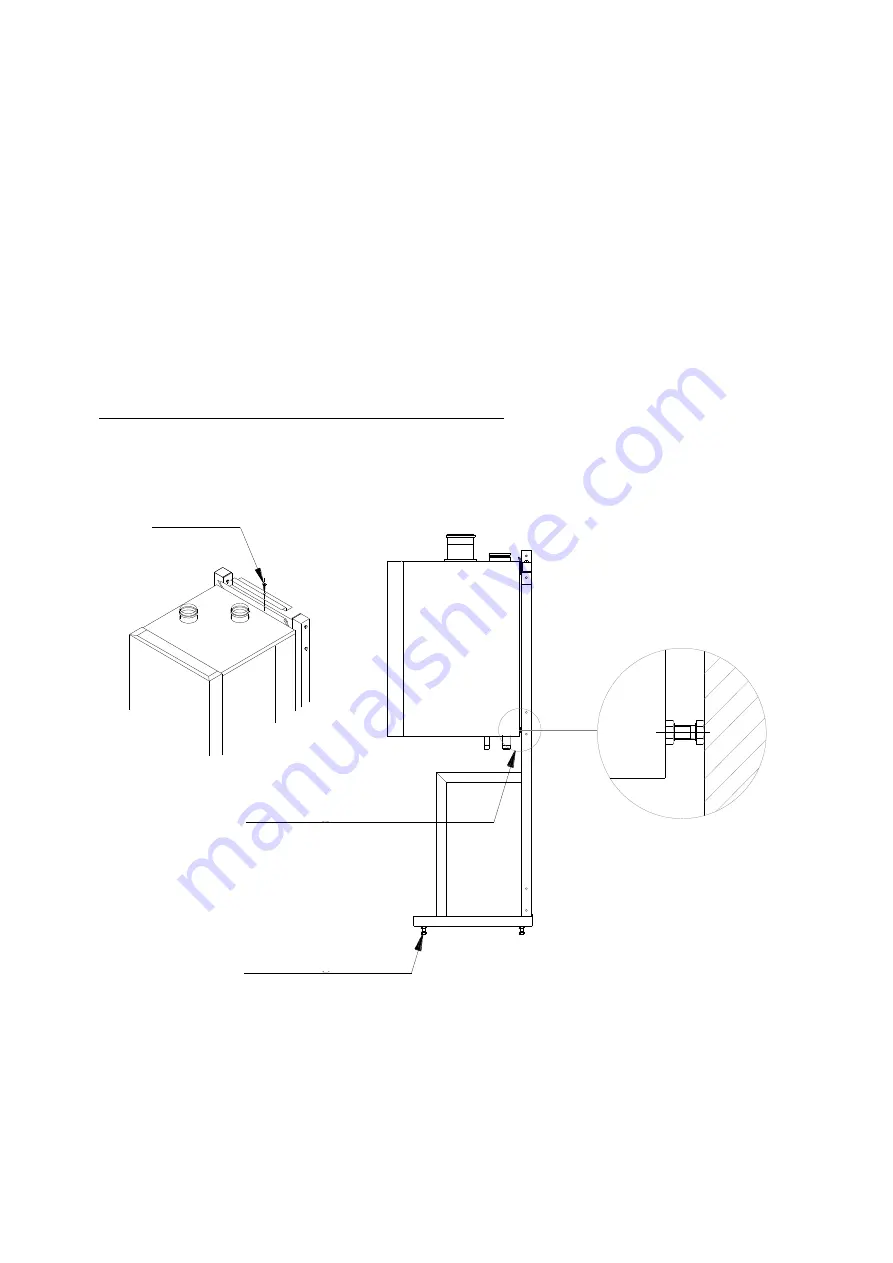
18
10.
Mounting the Boilers on the Frame
1. Before mounting the boiler on the frame, ensure that the frame is level both horizontally and vertically.
If
necessary, adjust with the adjusting bolts on the lower side of the frame (see Figure 10.1).
2. Hang the boilers on the frame.
3. Align the boilers with the L-stand in such a way that there is an exact 50 mm gap between the boilers.
4. Lock the suspension bracket with the locking strip to prevent the boiler from falling off the bracket (see
drawing).
5. Make sure that the boiler is at the right position (near level).
The boilers must hang backwards slightly (1º +/- 0.5º). If necessary, adjust with the adjusting bolts on the
lower rear side of the back panel (see Figure 10.1). When the adjusting bolts are
not
sufficient, the space
behind the bolts needs to be filled to achieve the correct position.
Attention
!
The boiler must
never
lean forward
in the mounted position.
6. Next mount the hydraulic group and connecting sets. See chapter 11.
Figure 10.1 Mounting details
Levelling frame
Locking
Levelling boiler