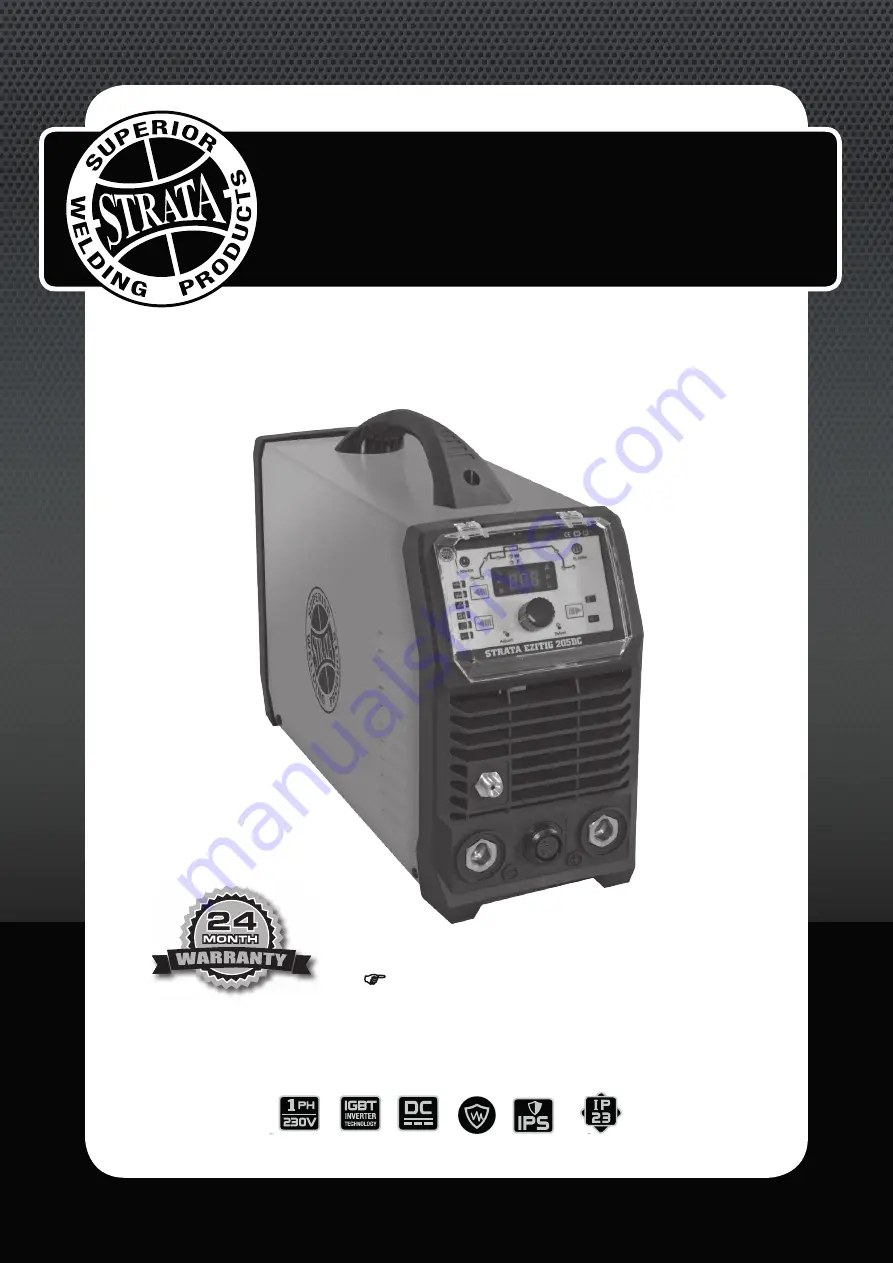
OPERATING INSTRUCTIONS
www.strata.co.nz
230V 50HZ
SINGLE
PHASE
IGBT
INVERTER
TECHNOLOGY
DIRECT
CURRENT
OUTPUT
SPIKE/
GENERATOR
SAFE
INTELLIGENT
PROTECTION
SYSTEM
IP23 CORROSION
& SALT SPRAY
RESISTANT
EZITIG 205DC
INVERTER WELDER
IMPORTANT!
To qualify for full 24 month warranty, you must register within 30 days of purchase. See inside for details.
Read these Operating Instructions Completely before attempting to use this machine. Save this manual and keep
it handy for quick reference. Pay particular attention to the safety instructions we have provided for your
protection. Contact your distributor if you do not fully understand anything in this manual.