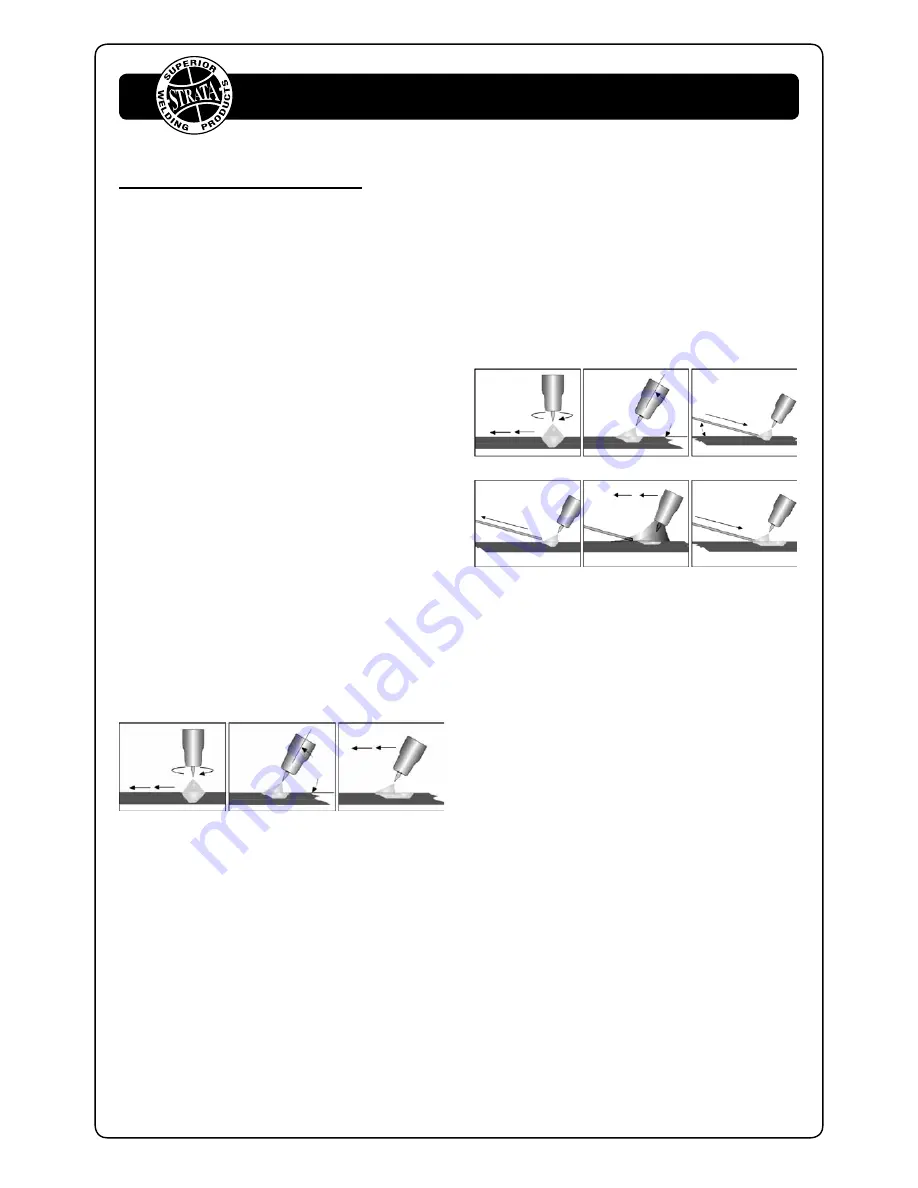
18
www.strata.co.nz
EZITIG 180
Tig Welding Techniques
Tig Welding Fusion Technique
Manual TIG welding is often considered the most dif-
ficult of all the welding processes. Because the welder
must maintain a short arc length, great care and skill
are required to prevent contact between the electrode
and the work piece. Similar to Oxygen Acetylene torch
welding, TIG welding normally requires two hands
and in most instances requires the welder to manu-
ally feed a filler wire into the weld pool with one hand
while manipulating the welding torch in the other.
However, some welds combining thin materials can
be accomplished without filler metal like edge, cor-
ner, and butt joints.
This is known as Fusion welding where the edges of
the metal pieces are melted together using only the
heat and arc force generated by the TIG arc. Once the
arc is started the torch tungsten is held in place until a
weld pool is created, a circular movement of the tung-
sten will assist is creating a weld pool of the desired
size. Once the weld pool is established tilt the torch
at about a 75° angle and move smoothly and evenly
along the joint while fusing the materials together.
of the molten pool, the arc will melt the filler wire into
the weld pool as the torch is moved forward. Also a
dabbing technique can be used to control the amount
of filler wire added, the wire is fed into the molten
pool and retracted in a repeating sequence as the
torch is moved slowly and evenly forward. It is im-
portant during the welding to keep the molten end of
the filler wire inside the gas shield as this protects the
end of the wire from being oxidised and contaminat-
ing the weld pool.
TIG Welding Guide
Tig Welding with Filler Wire Technique
In many situations with TIG welding, it is necessary
to add a filler wire into the weld pool to build up weld
reinforcement and create a strong weld. Once the arc
is started the torch tungsten is held in place until a
weld pool is created, a circular movement of the tung-
sten will assist is creating a weld pool of the desired
size. Once the weld pool is established tilt the torch
at about a 75° angle and move smoothly and evenly
along the joint. The filler metal is introduced to the
leading edge of the weld pool. The filler wire is usually
held at about a 15° angle and fed into the leading edge
Travel Direction
75
o
Form a weld pool
Angle torch
Move the torch slowly
and evenly forward
75
o
Travel Direction
Form a weld pool
Angle torch
Add TIG filler wire
Retract the filler wire
Move the torch forward to
the front of the weld pool
Repeat the process
15
o
Gas Shield
Electrodes
Tungsten Electrodes
Tungsten is a rare metallic element used for manufac-
turing TIG welding electrodes. The TIG process relies
on tungsten’s hardness and high temperature resist-
ance to carry the welding current to the arc. Tungsten
has the highest melting point of any metal at 3410
degrees Celsius.
Tungsten electrodes are non-consumable and come
in a variety of sizes, they are made from pure tung-
sten or an alloy of tungsten and other rare earth ele-
ments. Choosing the correct tungsten depends on the
material being welded, the amount of amps required
and whether you are using AC or DC welding current.
Tungsten electrodes are colour-coded at the end for
easy identification.
Thoriated Tungsten Electrodes
Thoriated tungsten electrodes (AWS classification
EWTh-2) contain a minimum of 97.30 percent tung-
sten and 1.70 to 2.20 percent thorium and are called 2
percent thoriated. They are the most commonly used