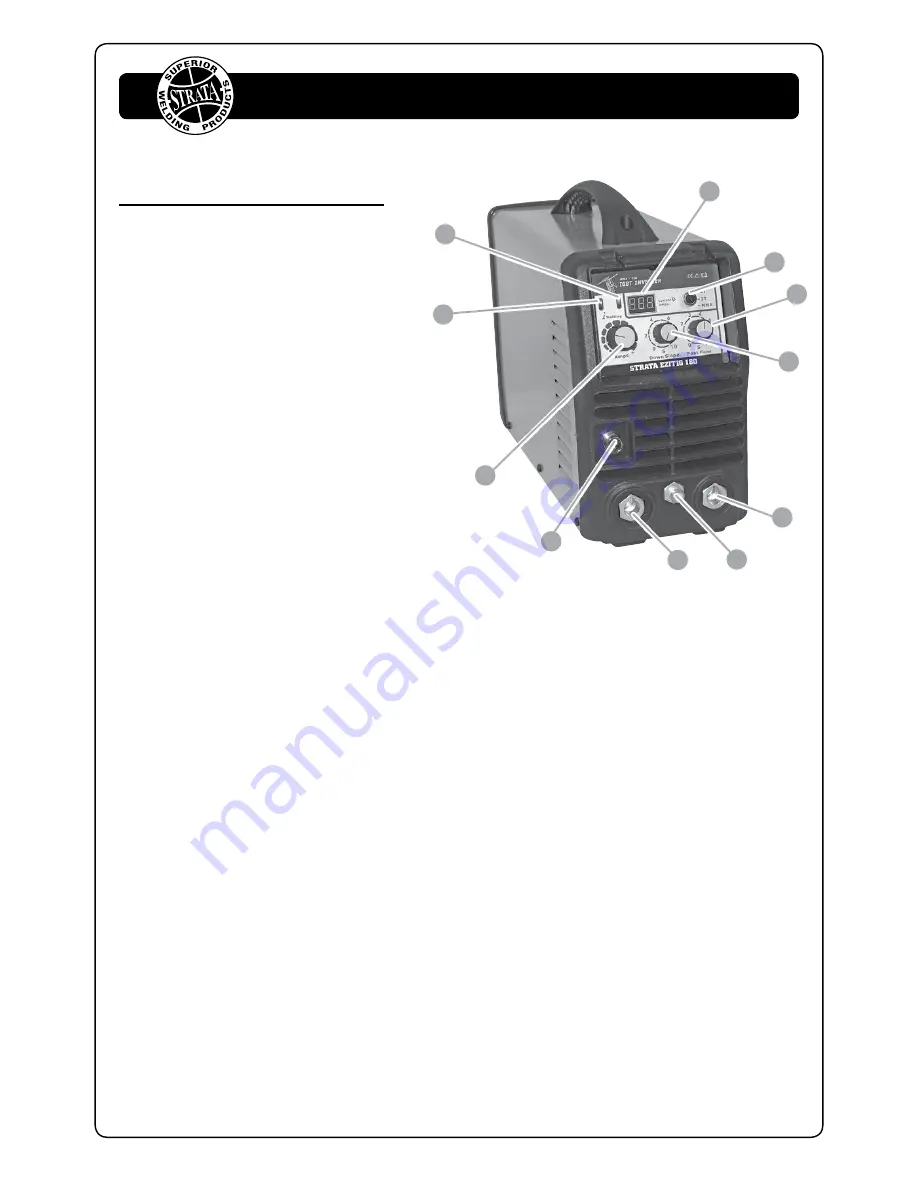
5
www.strata.co.nz
EZITIG 180
*Denotes more detailed explanation of function to follow.
1.
Digital current display meter
2.
Welding output mode switch. Sets power
source in TIG 2T, TIG 4T or MMA mode*
3.
TIG post gas flow control knob*
4.
Down slope control knob*
5.
Positive (+) welding power output connection socket
6.
TIG torch gas connector
7.
Negative (-) welding power output connection socket
8.
TIG torch remote connection socket
9.
Welding current control knob
10.
Power Indicator. Lights when input power
connected and machine switched on
11.
Error/ Overload Indicator*
Further Controls Explained
Overload/ Error Indicator
Lights when over voltage, over current or electrical
overheating (due to exceeding duty cycle) is detected
and protection is activated. When protection is acti-
vated, welding output will be disabled until the safety
system senses the overload has reduced sufficiently
and indicator lamp goes out. May also trigger if ma-
chine experiences an internal power circuit failure.
TIG 2T/4T
In 2T mode the trigger is pulled and held on to acti-
vate the welding circuit, when the trigger is released,
the welding circuit stops. 4T is known as ’latching’
mode. The trigger is pulled once and released to ac-
tivate the welding circuit, pulled and released again
to stops the welding circuit. This function is useful to
longer welds as the trigger is not required to be held
on continuously.
Post Flow
Controls the period of time the shielding gas contin-
ues to flow for after the arc is stopped. This protects
the weld area and torch tungsten from contamination
while it is still hot enough to react with atmospheric
gases, after the weld is finished.
Down Slope
When the trigger is released, the welding current will
reduce gradually over the time selected down to 0.
This allows the operator to complete the weld without
leaving a ‘crater’ at the end of the weld pool.
Tips & Tricks
Duty Cycle Rating
Welding duty cycle is the percentage of actual weld-
ing time that can occur in a ten minute cycle. E.g.
20% at 160 amps - this means the welder can weld at
160 amps for 2 minutes and then the unit will need to
be rested for 8 minutes.
All duty cycle ratings are based on an ambient air
temperature of 40°C with 50% humidity, which is the
international standard for such a rating. In an envi-
ronment with temperatures exceeding 40°C, the duty
cycle will be less than stated. In ambient temperature
less than 40°C, duty cycle performance will be higher.
Know Your Machine
1
3
2
4
5
6
7
8
9
10
11