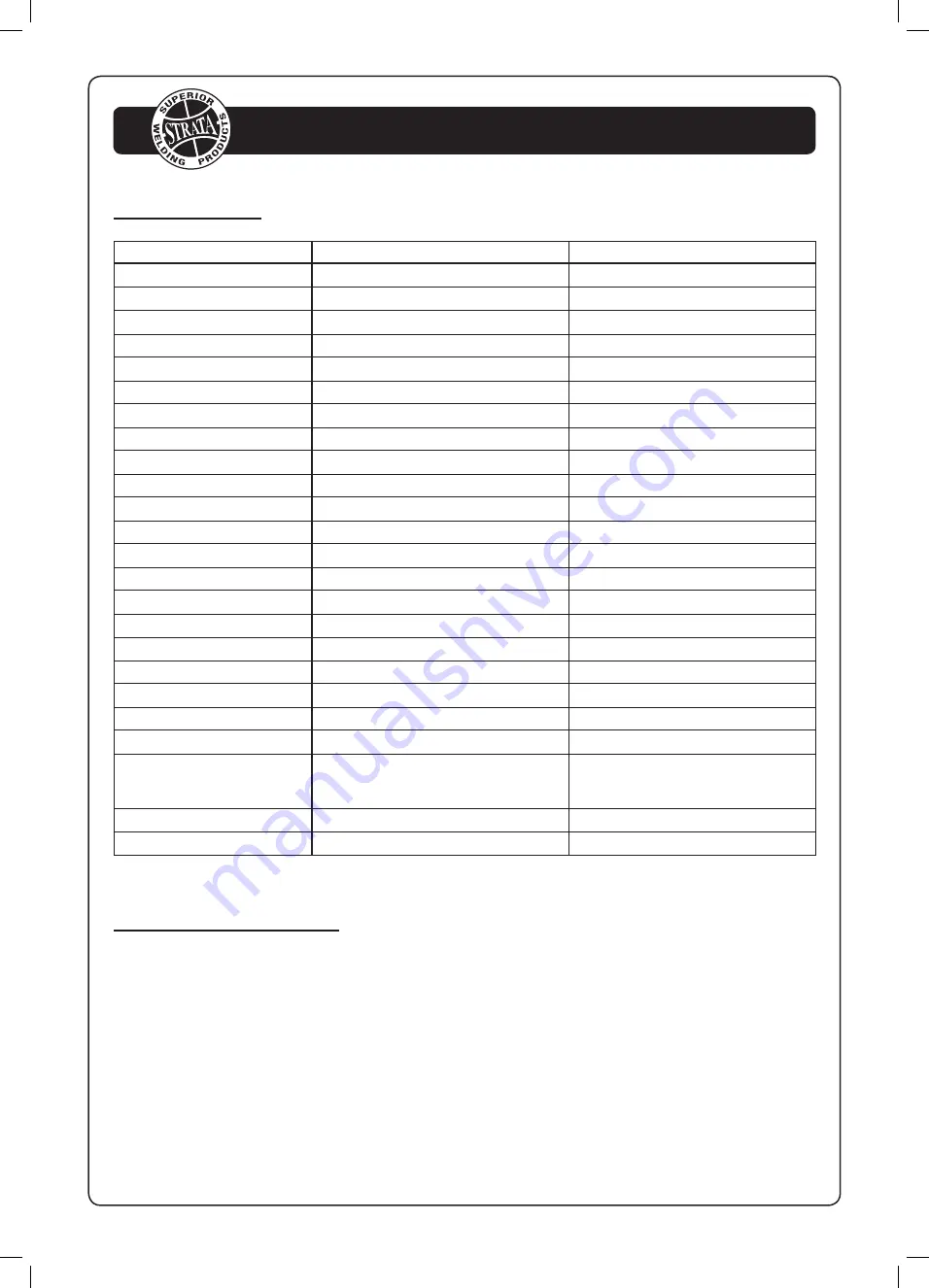
4
www.strata.co.nz
www.strata.co.nz
EZIMIG 205 / ADVANCEMIG 255
Model EziMig205
AdvanceMig255
Dimensions (WxLxH)
850x440x730mm
850x440x730mm
Weight 36kg
38.5kg
Input Power Supply -
230V AC 15A 50/60Hz
230V AC 15A 50/60Hz
Input Power Supply Tolerance
230±10%V
90V-275V AC
Maximum Input Current
44A
38A
Input Generator Capacity
12 KVA
10 KVA
MIG Voltage Output
16V-27V
16V-30V
MIG Current Output
40A-200A
40A-250A
MIG Duty Cycle
200A@ 25% 145A@60%, 110A @ 100%
250A@ 40% 195A@60%, 150A @ 100%
MIG No Load Voltage
28V
26V
Wire Feeding Speed
2.4-18m/min
2.4-18m/min
MMA Current Output
10A-200A
10A-250A
MMA Duty Cycle
200A@25%, 130A@60%, 80A@100%
250A@15%, 180A@60%, 140A@100%
MMA No Load Voltage
58V
58V
TIG Current Output
10A-200A
10A-250A
TIG Duty Cycle
200A@25%, 165A@60%, 130A@100%
250A@30%, 195A@60%, 150A@100%
TIG Sytem
Internal solenoid gas control, Lift ignition
Internal solenoid gas control, Lift ignition
Insulation Class
IP23
IP23
Power Efficiency
≥
85%
≥
85%
Power Factor
0.65
0.99
Standards EN60974-1:2012
EN60974-1:2012
MIG Drive Rollers Available
0.6/0.8/0.9/1.0/1.2mm V Groove,
0.6/0.8/0.9/1.0/1.2mm V Groove,
Knurled 0.8/0.9/1.0/1.2mm,
Knurled 0.8/0.9/1.0/1.2mm,
U Groove 0.8/1.0/1.2mm
U Groove 0.8/1.0/1.2mm
MIG Wire spool Size
D200mm/D300mm 5kg/15kg
D200mm/D300mm 5kg/15kg
Warranty
36 months with registration
36 months with registration
Specifications
Standard Accessories
Strata Professional MT250-40ER MIG Torch
4m MMA lead with heavy duty twist lock electrode holder
3m Earth Lead with heavy duty earth clamp
Strata 2 Stage Flowmeter Argon Gas Regulator
Argon Regulator/CO2 Cylinder Adaptor
4m Gas Hose
Gas Inlet Quick Connector
Gas Hose Clamp x2
Wire Drive Roller 0.6/0.8mm ‘v’ groove x2
Wire Drive Roller 0.9/1.0mm ‘v’ groove x2
Wire Drive Roller 0.8/0.9mm flux cored x2