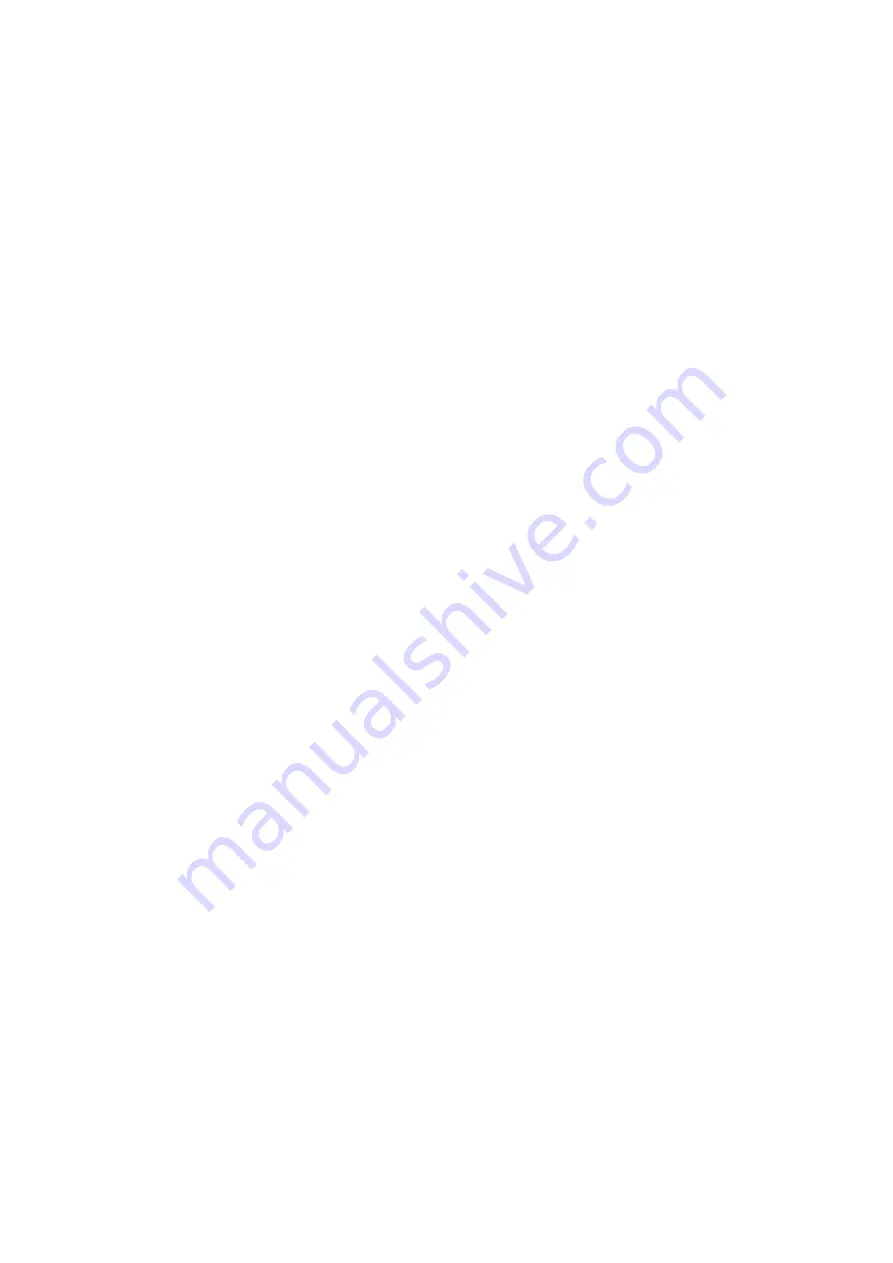
7
Maintenance.
Stokvis EP units have been designed to be easy to maintain, thus ensuring trouble-free operation.
On two pump units the duty pump will automatically rotate per operation, to equalise wear and to
exercise the standby pump.
At regular intervals, but all least every six months, the following points should be checked.
1)
Bleed a little water from the system when at ambient temperature, and check that the pump
cut-in and cut-out pressures are as shown in the table of settings attached.
On two pump units continue to bleed water from the system, at a rate greater than approx.
0.75gpm, once the duty pump has started.
This will cause the standby pump to start.
Once the standby pump has started, close the bleed and allow the pressure to rise, noting the
pressure at which the pumps switch off.
If necessary adjust the pressure switch (es) to achieve the correct pressure settings.
Check that the pump(s) run, without excessive noise or vibration and do not leak from the
mechanical seal, either when running or when stationary.
2)
Using the isolating valve provided within the unit to isolate the system from the pressure
sensing line, bleed off a few drops of water from the sensing line, having first switched the
pump (s) off.
The pressure within the sensing line will drop, as indicated by the unit gauge.
Check that the switch resets before cold fill pressure is reached.
Close the valve between the unit and system and expansion vessels.
Run the pump, raising the pressure and check that the system high pressure alarm switch
operates at the correct pressure.
Switch off the pump and open isolating valve.
If necessary, adjust the pressure switch (es) to achieve the correct pressure settings.
3)
Check the pre-charge pressures in both the unit pressure vessel and system expansion
vessel(s).
Isolate and drain all water from vessels before checking pre-charge pressure at the Schrader
valve, with suitable pressure gauge.
When a checking the pre-charge pressure, note if any water vapour is exhausted from the
Schrader valve.
If this is the case, then the vessel diaphragm has become perforated, and either the
diaphragm (or complete vessel, if it is a fixed diaphragm type), must be replaced.
4)
Check over all electrical equipment, checking operation of relays, Mcb’s, lamps, etc.
Check all terminals are tight. Generally clean within the enclosure.
5)
Check operation of unit ball valve, ensuring valve will open, and close drip-tight. Lubricate the
fulcrum and/or strip and clean if necessary.
Check inside break tank for any debris or sediment and if necessary drain tank and clean out.
If larger amounts of sediment are found regularly, check the system for leakage.
6)
Generally check over and clean the exterior of the unit, at the same time checking for leaks.