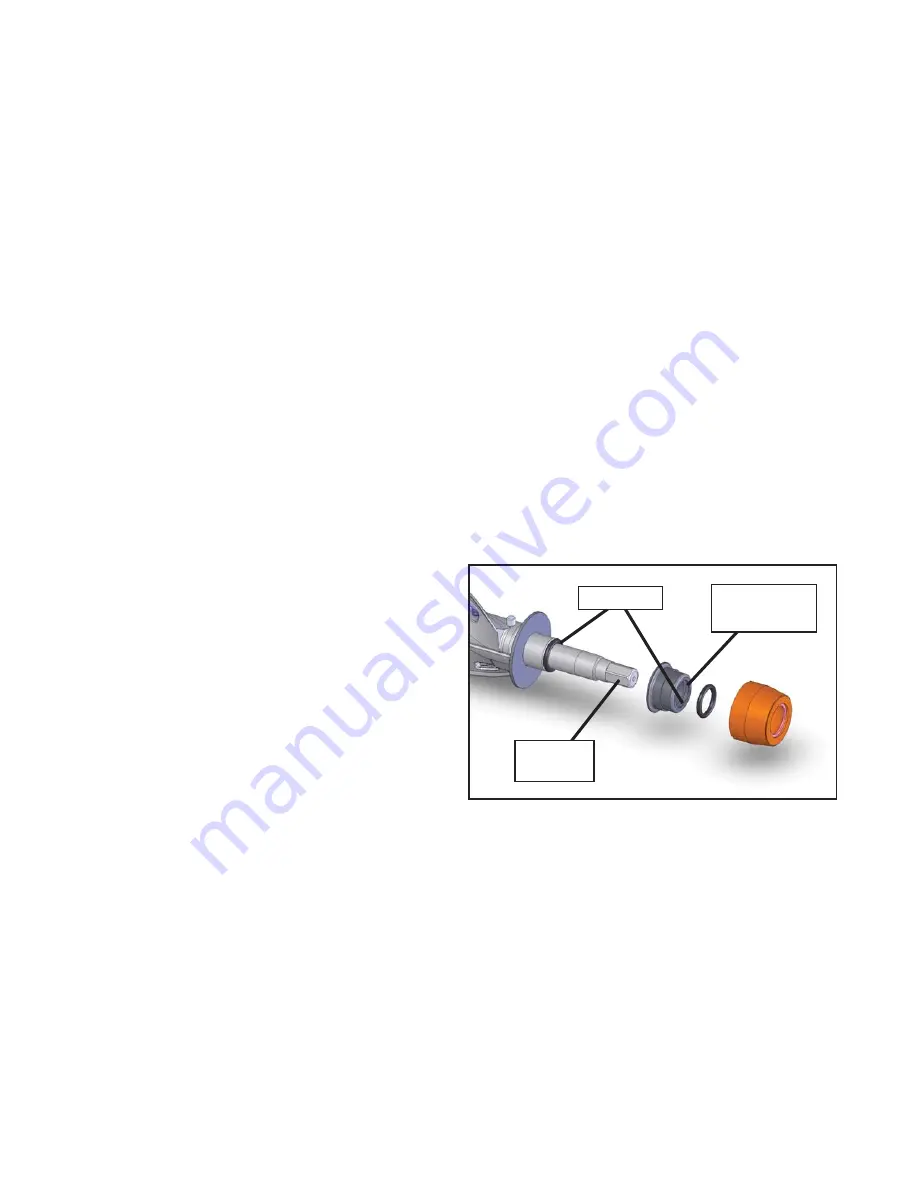
10
3.4 CLEANING DISASSEMBLED PARTS
Disassembled machine parts require complete cleaning,
sanitizing and air drying before assembling. Local and state
health codes will dictate the procedure required. Some
state health codes require a four sink process (pre-wash,
wash, rinse, sanitize, air dry), while others require a three
sink process (without the pre-wash step). The following
procedures are a general guideline only. Consult your
local and state health codes for the procedures required
in your location.
A.
Disassemble all parts. (Refer to Section 3.4 for
the disassembly of machine parts.)
B.
Place all front door and auger parts in clean 90° to
110°F (32°C to 43°C) water and wash thoroughly
(four sink procedure only).
C.
Place all parts in 90° to 110°F (32°C to 43°C) mild
detergent water and wash thoroughly.
D.
Rinse all parts with clean 90° to 110°F (32°C to
43°C) water.
E.
Sanitize all machine parts following procedures
outlined below.
3.5 SANITIZING MACHINE PARTS
A.
Use a sanitizer, mixed according to manufacturer’s
instructions, to provide a 100 parts per million
strength solution. Mix sanitizer in quantities of
no less than 2 gallons of 90° to 110°F (32°C to
43°C) water. Any sanitizer must be used only in
accordance with the manufacturer’s instructions.
B.
Place all parts in the sanitizing solution for 5
minutes, then remove and let air dry completely
before assembling in machine.
3.6 CLEANING THE MACHINE
The exterior should be kept clean at all times to preserve
the luster of the stainless steel. A high grade of stainless
steel has been used on the machine to ease cleanup. To
remove spilled or dried mix, wash the exterior with 90° to
110°F (32°C to 43°C) soapy water and wipe dry.
Do not use highly abrasive materials, as they will mar the
fi nish. A mild alkaline cleaner is recommended. Use a soft
cloth or sponge to apply the cleaner. For best results, wipe
with the grain of the steel.
A.
Clean the rear seal surface from inside of the
freezing cylinder.
B.
Using sanitizing solution and the large barrel
brush provided, sanitize the freezing cylinder by
dipping the brush in the sanitizing solution and
brushing the inside of the freezing cylinder.
C.
Remove the drip tray by pulling from the front
panel. Clean and replace the drip tray.
3.7 ASSEMBLING MACHINE
To assemble the machine parts, refer to the following steps:
NOTICE
Petrol-Gel sanitary lubricant or equivalent must be
used when lubrication of machine parts is specifi ed.
NOTICE
The United States Department of Agriculture and
the Food and Drug Administration require that lubri-
cants used on food processing equipment be certi-
fi ed for this use. Use lubricants only in accordance
with the manufacturer’s instructions.
A.
Assemble all o-rings onto parts dry, without
lubrication. Then apply a thin fi lm of sanitary
lubricant to exposed surfaces of the o-rings.
B.
Lubricate the rear seal area on the auger shaft
with a thin layer of sanitary lubricant. Install the
rear seal o-ring. Lubricate the outside of the rear
seal o-ring with sanitary lubricant.
C.
Install the stainless steel rear seal adapter into
the rear seal dry (without lubricant). Lubricate the
inside surface of the rear seal adapter, including
the adapter o-ring, and install it onto the auger
shaft. DO NOT lubricate the outside of the rear
seal adapter (Fig. 3-6).
D.
Lubricate the hex drive end of the auger with a
small amount of spline lubricant. A small container
of spline lubricant is shipped with the machine.
E.
Screw the springs onto the studs in the plastic
fl ights. The springs must be screwed into the
fl ights completely to provide proper compression.
F.
Install the two plastic fl ights onto the rear of the
auger and insert it part way into the freezing
cylinder.
Figure 3-6 Rear Seal Assembly
Spline
Lubricant
Petrol-Gel
Place O-Ring
Inside Insert