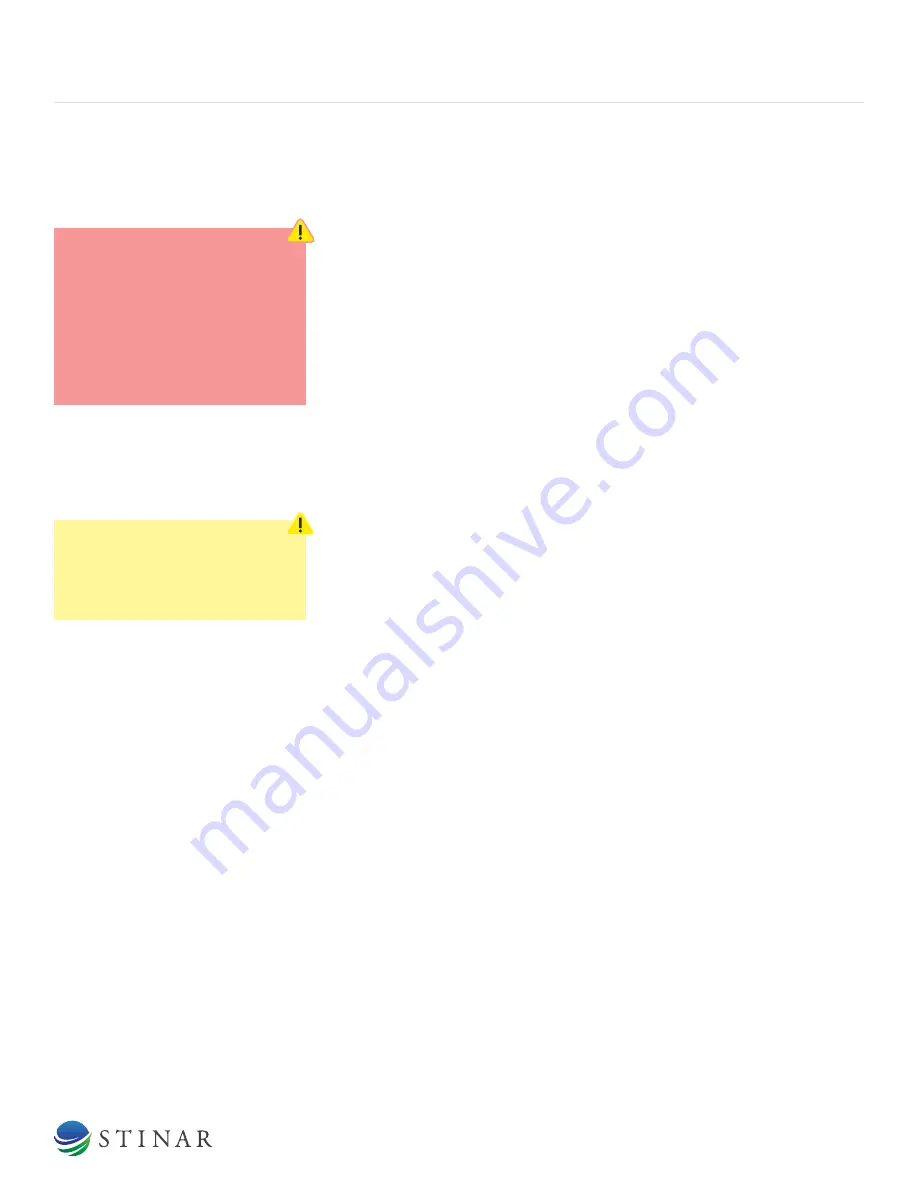
SECTION 2 | SERVICING THE FLUSH AND FILL CART
Flush & Fill Cart SFFC-70/2 | 29
2.1 | SERVICING
WARNING!
Perform no welding, cutting,
patching and such on any load
bearing or supporting structure.
If such repairs are necessary,
contact the Engineering de-
partment of Stinar Corporation
before making any alterations.
CAUTION!
Do not attempt any welding
on tank unless top access
cover is removed.
2.1.1 | Cart Chassis
2.1.1.1 | Brake Adjustment
Check operation of brake mechanism before each use. Adjust brake
linkage if needed. See Adjustment section of this chapter for procedure.
2.1.1.2 | Wheels and Tires
• Check tires for condition before each use.
• Repair tires as required.
• Check operation of brake mechanism before each use. Adjust brake
linkage if required.
2.1.1.3 | Sheet, Bar and Tubular Member (Non-Load
Bearing)
• Repair cracks or metal fatigue failures by stop-drilling, welding,
patching or splicing.
•
Prime and paint marred, rusted or damaged finish using a high
grade primer and finish paint materials.
• Clean areas that are extremely oily or greasy with mineral solvents
and degreasers before painting.
2.1.2 | Coolant System
2.1.2.1 | Coolant Tank
• The coolant tank may be drained by opening the valve at the
bottom of the tank (V8 fig. 2.1.2). To drain contaminated reservoir,
open valve at the bottom of contaminated reservoir (V8). Drain
contaminated coolant only at an approved waste disposal facility.
• The tank is constructed of type 304 stainless steel. If welding is
necessary, use only type 308 rod or wire.
• The coolant tank interior and coolant system may be cleaned with a
mild detergent. Flush thoroughly after repairs and cleaning.
2.1.2.2 | Strainer
A strainer is located in the line running from the coolant tank to the
pump on both tanks. A gate valve adjacent to the strainer allows service
to be performed on the strainer without draining the coolant tank. Clean
strainer screen every 100 hours.
2.1.2.3 | Filter
A filter is located between the flow meter and the supply hose. Replace the
filter element according to the filter condition indicator. When the green
indicator turns red, it is time to replace the filter element.
Summary of Contents for Flush & Fill Cart SFFC-70/2
Page 12: ...Flush Fill Cart SFFC 70 2 12 FIGURE 1 1 1 2 COOLANT SYSTEM FILL MODE...
Page 15: ...Flush Fill Cart SFFC 70 2 15 FIGURE 1 1 1 4 ELECTRICAL SYSTEM THERMOSTAT...
Page 19: ...Flush Fill Cart SFFC 70 2 19 FIGURE 1 2 3 3 FLUSH AND FILL MODE...
Page 21: ...Flush Fill Cart SFFC 70 2 21 FIGURE 1 2 3 5 DEAERATE MODE...
Page 23: ...Flush Fill Cart SFFC 70 2 23 FIGURE 1 2 3 6 PUMPING OUT OF THE WASTE TANK...
Page 30: ...Flush Fill Cart SFFC 70 2 30 FIGURE 2 1 2 1 COOLANT TANK DRAIN V8...
Page 44: ...Flush Fill Cart SFFC 70 2 44 FIGURE 4 3 2 FRONT AXLE ASSEMBLY...
Page 46: ...Flush Fill Cart SFFC 70 2 46 FIGURE 4 3 3 WHEEL HUB ASSEMBLY A A SECTION A A 1 5 2 4 3...
Page 48: ...Flush Fill Cart SFFC 70 2 48 FIGURE 4 3 4 COOLANT SYSTEM...
Page 51: ...Flush Fill Cart SFFC 70 2 51 FIGURE 4 3 8 ELECTRICAL SYSTEM...