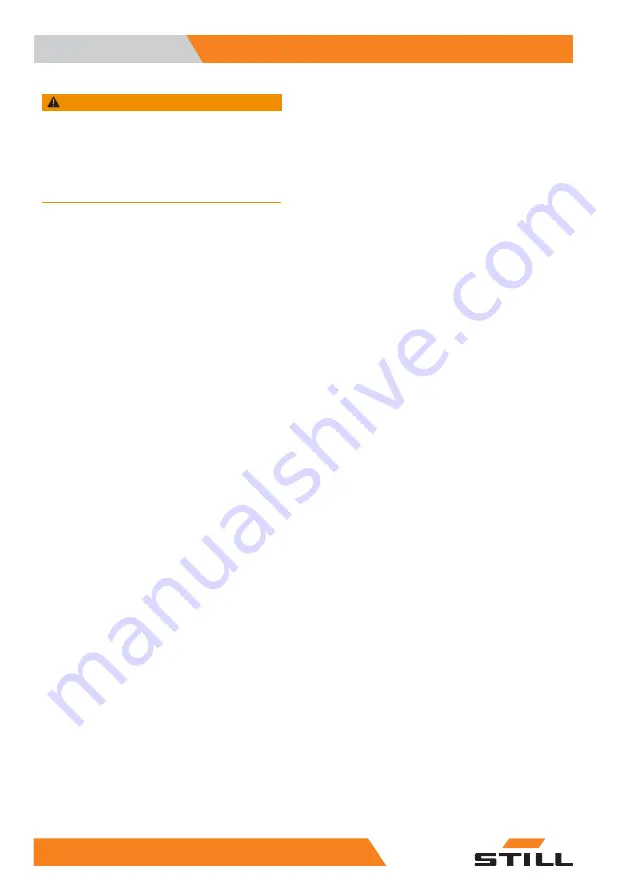
4
Operation
General commissioning
WARNING
Risk of damage to property, risk of crushing
Observe the information in the section entitled Safe
handling of the traction battery.
Before starting each shift, check that the battery
lock is in good working order and that it functions
correctly.
Function check
Before releasing the truck for its intended
use, a thorough function check should first be
carried out. For this, see the Checklist before
starting work.
If, after having done the checks before starting
work any defects, regarding operating or
traffic safety are discovered, then steps
have to be taken immediately to properly
and professionally repair theses defects. It
is prohibited to continue using the truck until it
is repaired.
If your truck is equipped with any special
features, these should also be tested carefully.
A descritption of the optional attachments see
Optional Equipment.
54
5231 804 2502 EN - 11/2017
Summary of Contents for MX-X
Page 1: ...Original instructions Order picking truck MX X 2332 2334 5231 804 2502 EN 11 2017 ...
Page 2: ......
Page 7: ...1 Foreword ...
Page 15: ...2 Safety ...
Page 26: ...2 Safety Personal protective equipment 20 5231 804 2502 EN 11 2017 ...
Page 27: ...3 Overview ...
Page 45: ...4 Operation ...
Page 90: ...4 Operation Parking decommissioning 84 5231 804 2502 EN 11 2017 ...
Page 91: ...5 Regular care and maintenance ...
Page 103: ...6 Technical data ...
Page 105: ...7 Special equipment ...
Page 131: ......