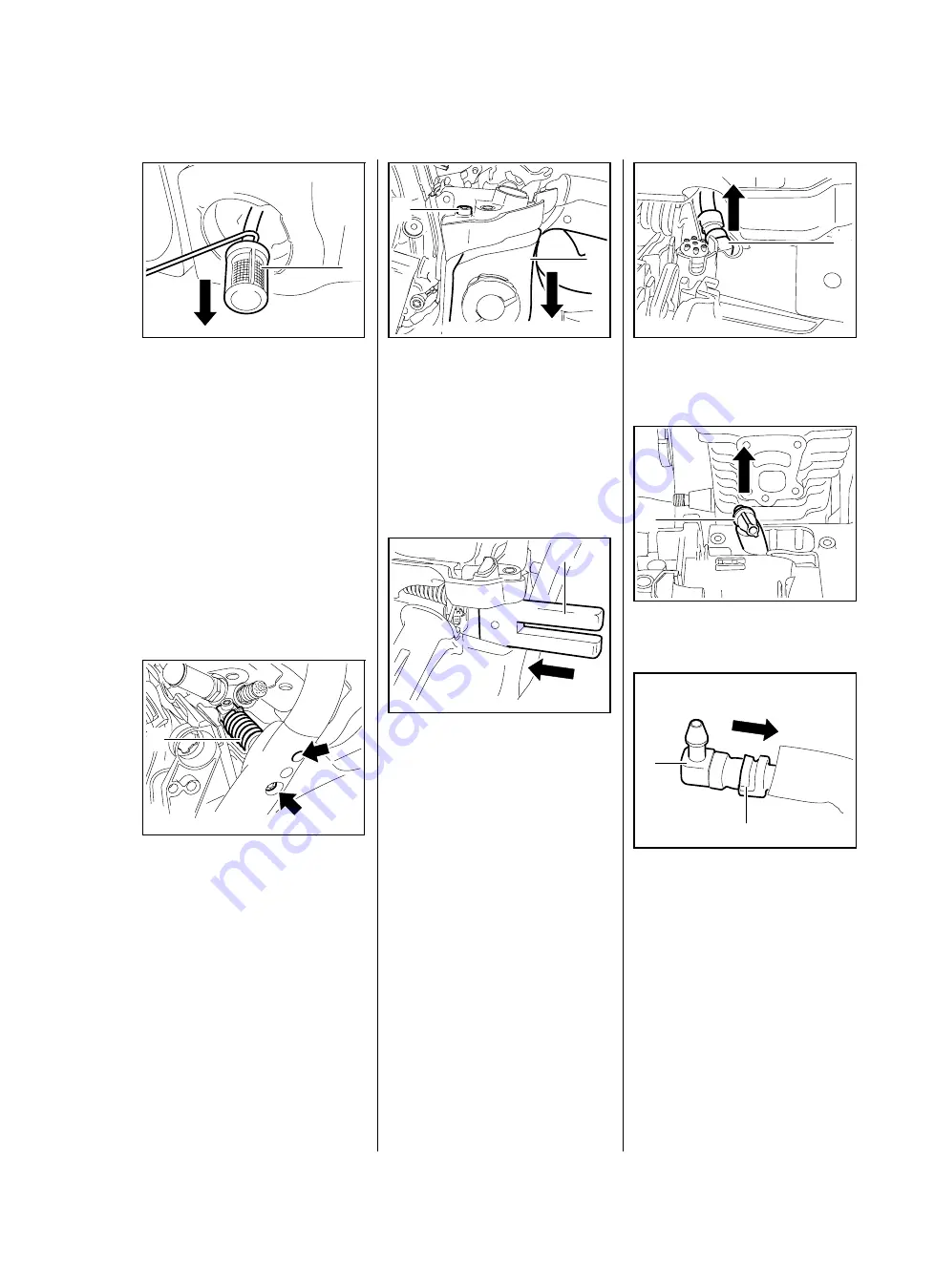
85
MS 311, MS 391
– Open the tank cap.
:
Use hook 5910 893 8800 to
remove the pickup body (1) from
the fuel tank.
Do not overstretch the fuel hose.
:
Pull off the pickup body (1).
– Reassemble in the reverse
sequence.
12.11.2 Fuel Hose
:
Take out the screws (arrows) and
pry the AV spring (1) out of the
handlebar.
1
0001RA410 TG
4903RA243 TG
1
– Remove the shroud,
– Remove the air guide shroud,
:
Take out the screw (1).
:
Lower the tank housing (2).
:
Slide the wooden assembly
block (1) between the engine
housing and tank housing.
4903RA060 TG
1
2
4903RA108 TG
1
:
Pull out the fuel hose (1) with
connector.
:
Remove the fuel hose (1).
:
Pull the fuel hose (2) off the
connector (1).
4903RA164 TG
1
4903RA000 TG
1
0001RA412 TG
1
2
Summary of Contents for MS 311
Page 1: ...STIH STIHL MS 311 391 2009 06 ...
Page 92: ...91 MS 311 MS 391 ...
Page 93: ...92 MS 311 MS 391 ...
Page 94: ...englisch english 0455 542 0123 M2 2 K09 FST Printed in Germany ...