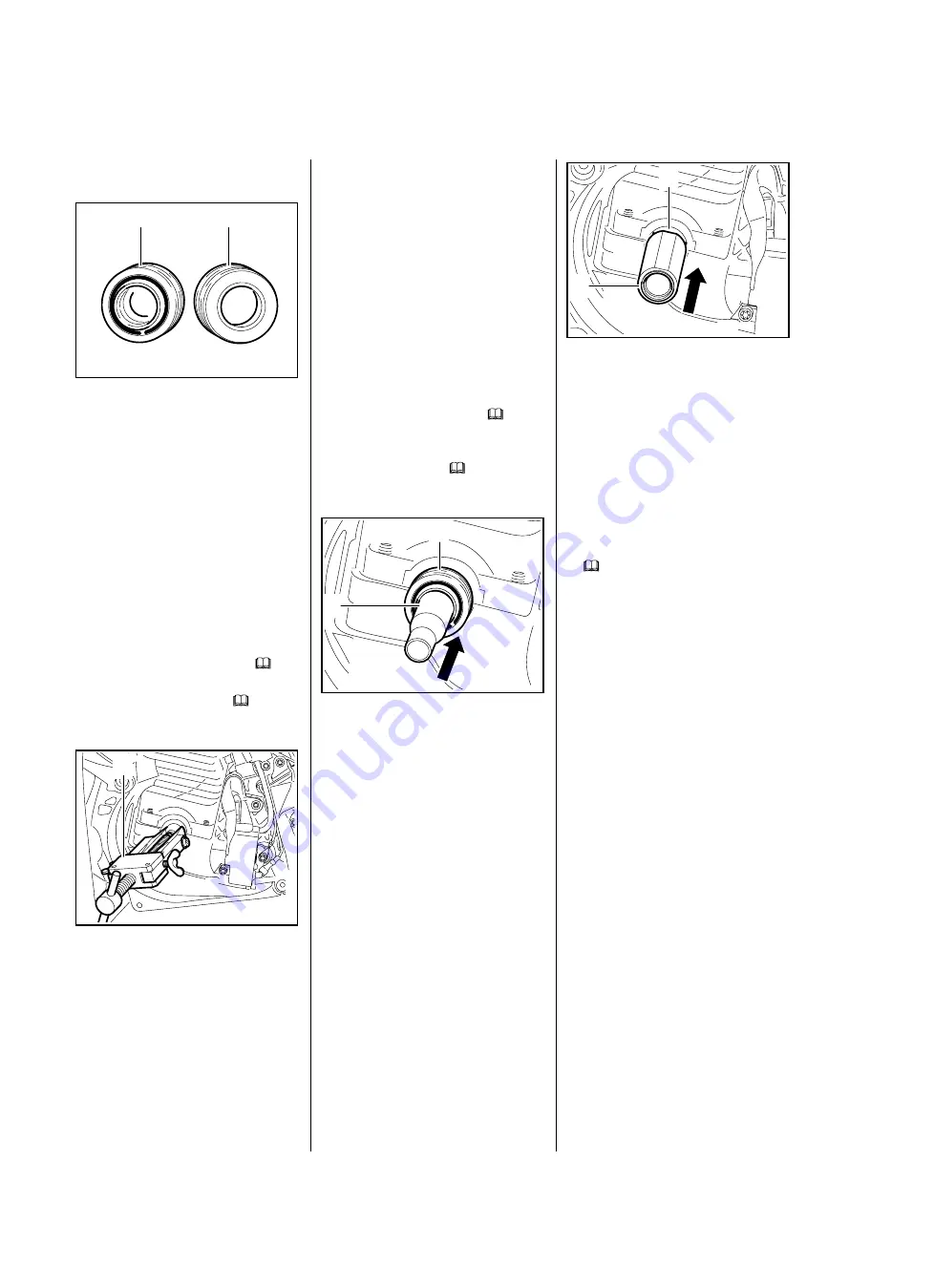
36
MS 271 C, MS 291 C
6.3
Oil Seals
When replacing oil seals, note that a
soft oil seal (1) must be installed at
the ignition side and a hard oil
seal (2) on the clutch side.
Install the soft oil seal with the
support ring facing outwards and
the hard oil seal with its sealing lip
facing the crankshaft.
It is not necessary to disassemble
the engine to replace the oil seals.
Ignition side
– Remove the fan housing,
b
8.2
– Remove the flywheel,
b
7.6
Take care not to damage the
crankshaft stub.
2710RA143 TG
1
2
2710RA084 TG
1
– Free off the oil seal in its seat by
tapping it with a suitable tube or a
punch.
:
Apply puller (1) 5910 890 4400
with No. 3.1 jaws 0000 893 3706.
– Clamp the puller arms.
– Pull out the oil seal.
Installing
– Clean the sealing face,
– Lubricate sealing lips of new oil
seal with grease,
:
Fit the installing sleeve (1)
1141 893 4600.
:
Slip the oil seal (2), support ring
facing outwards, over the
installing sleeve.
– Remove the installing sleeve (1).
2710RA085 TG
2
1
:
Fit press sleeve (2)
1141 893 2401 with the mark
"ZS" facing the engine housing.
:
Use press sleeve (2)
1141 893 2401 to install the oil
seal (1).
The seating face must be flat and
free from burrs.
– Degrease the crankshaft taper,
– Reassemble all other parts in the
reverse sequence.
ZS
AS
2710RA086 TG
2
1