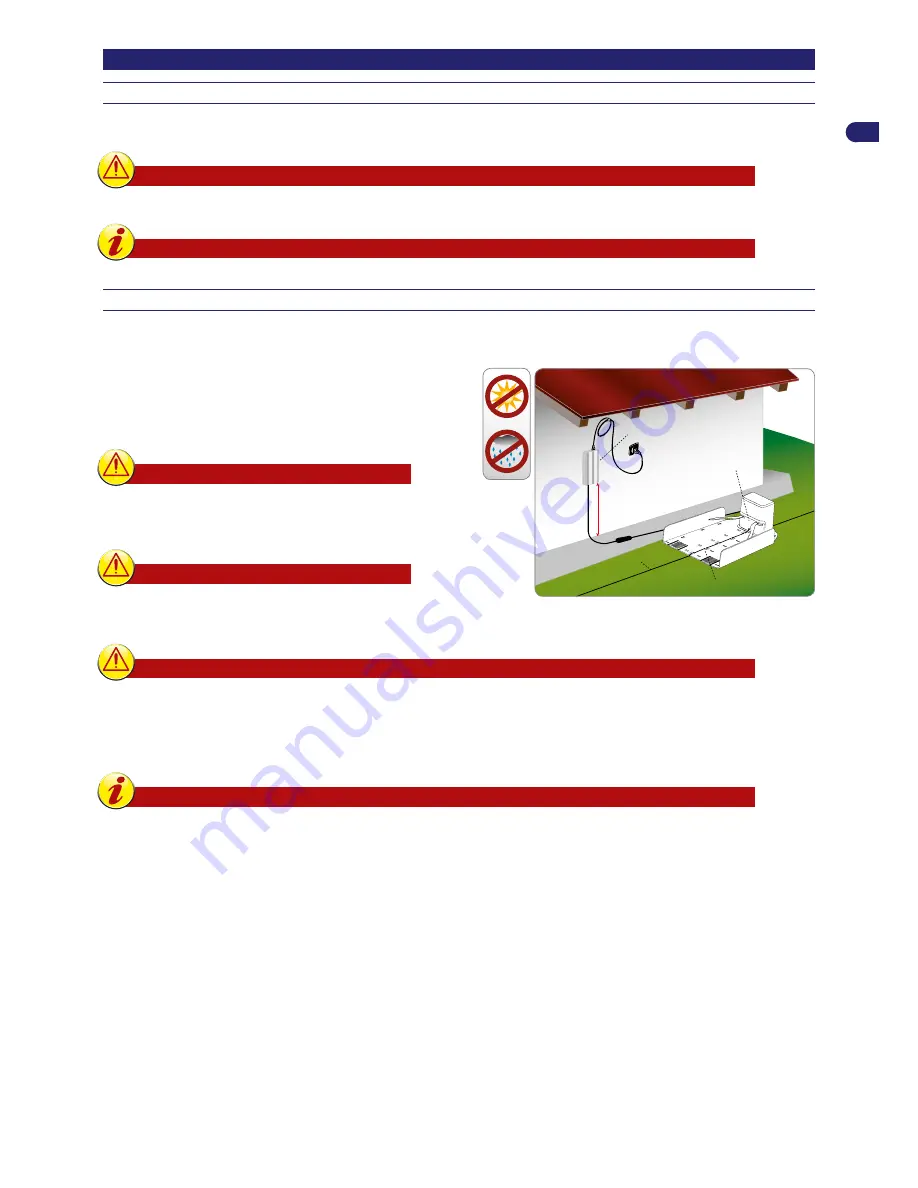
9
User’s manual
EN
INSTALLATION
PACKING AND UNPACKING
The equipment is delivered suitably packaged. When unpacking, carefully remove and check the integrity of the parts.
Warning – Caution
Keep plastic wrapping and plastic containers away from infants and children: risk of suffocation!
Important
Keep the packaging materials for future use.
PLANNING OF SYSTEM INSTALLATION
The robot is not difficult to install, but requires some preliminary planning in order to find the best area for installing the charging
station, power supply unit and for laying out the perimeter wire.
•
The charging station must be positioned on the edge of the
lawn, preferably in the largest area from which other areas of
the lawn are easily accessible. The area where the charging
station is installed is hereinafter referred to as the “Primary
Area.”
Warning – Caution
Position the power supply unit in an area that
cannot be reached by children. For example, at a
height above 160 cm (63 ").
Warning – Caution
Make sure only authorised people have access to
the power supply.
Power supply unit
perimeter wire
charging station
Min. height. 160 cm
/ 63 "
transmitter
Warning – Caution
When connecting the electricity, it is necessary that a power outlet is positioned near the installation area.
Make sure the connection to the mains power complies with the applicable laws. To operate in complete
safety, make sure the electrical system, which is connected to the power supply unit, is equipped with a well-
functioning earthing system. The supply circuit shall be protected by a residual current device (RCD) with a
tripping current of not more than 30 mA.
Important
It is advisable to install the unit in a cabinet for electric components (for outdoor or indoor use), equipped
with a key lock, and well-ventilated to maintain a correct air circulation.
•
The robot must be able to easily find the charging station at the end of the work cycle, which will also be the starting point for
a new work cycle and for reaching any other work areas, hereinafter referred to as “Secondary Areas.”.
•
Position the charging station according to these rules:
-
on level ground;
-
on compact and stable ground with good drainage;
-
preferably in the widest part of the lawn;
-
in case of sprinklers, make sure the water jets are not directed inside the charging station;
-
make sure the entrance of the charging station is positioned as shown in the figure, so that the robot can enter it by
following the perimeter wire in a clockwise direction;
-
there must be a straight area of 200 cm (78,74 ") in front of the charging station;
-
any metal bars or rails separating the lawn near the station may interfere with the signal. Position the station on a different
side of the garden or at a safe distance from the metal barrier. For more information, please contact the Manufacturer’s
Technical Service Centre or an authorised dealer.
•
The charging station must be well fastened to the ground. To prevent a small step from forming at the front of the charging
station, position a small piece of fake grass at its entrance to stop this from occurring. Alternatively, remove part of the grassy
surface and install the charging station flush with the grass.