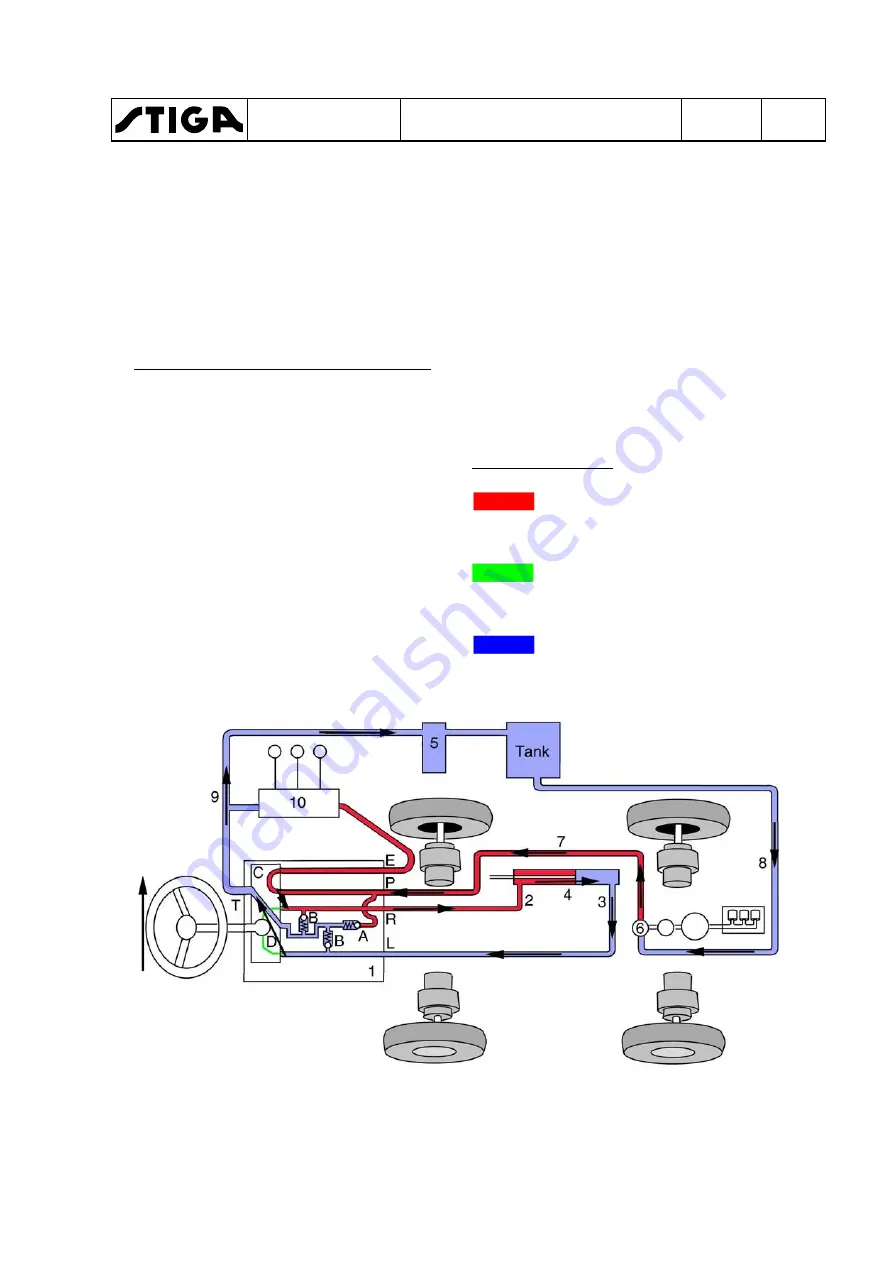
Steer to the right
1. Power steering servo containing the
following:
A. Pressure relief valve
B. Safety valves
C. Control module
D. Oil pump
Connections on power steering servo
P. Unregulated input from hydraulic
pump for external hydraulics.
T. Output to the tank for tramp oil and
return oil from the passive side of the
steering cylinder when steering.
E. Output to other external hydraulics.
L. Output to steering cylinder. Pres-
sure when steering to left.
R. Output to steering cylinder. Pres-
sure when steering to right.
2, 3Pressure lines for transferring steer-
ing force.
4. Steering cylinder.
5. Collector block.
6. Pump for external hydraulics, integrat-
ed with the drive pumps.
7. Pressure line.
8. Suction line.
9. Tramp oil line and return line.
10.External hydraulics.
Colour - Pressure
Red displays the supply pres-
sure to the power steering servo
and external hydraulics.
Green can be both the pressure
line and the return line, depend-
ing on the movement.
Blue displays the atmospheric
pressure in the oil reservoir and
lines.
WORKSHOP MANUAL
TITAN
Chapter
4 - Hydraulic system
EDITION
2018
Page
5
6
Summary of Contents for 13-7454-11
Page 1: ...Titan 2013 2019 WORKSHOP MANUAL...
Page 17: ...WORKSHOP MANUAL TITAN Chapter 1 General instructions EDITION 2018 Page 15...
Page 18: ...WORKSHOP MANUAL TITAN Chapter 1 General instructions EDITION 2018 Page 16...
Page 19: ...WORKSHOP MANUAL TITAN Chapter 1 General instructions EDITION 2018 Page 17...
Page 39: ...WORKSHOP MANUAL TITAN Chapter 3 Steering system EDITION 2018 Page 37...
Page 40: ...WORKSHOP MANUAL TITAN Chapter 3 Steering system EDITION 2018 Page 38...
Page 86: ...4 10 Hydraulic diagram WORKSHOP MANUAL TITAN Chapter 4 Hydraulic system EDITION 2018 Page 84...
Page 106: ...6 3 2 Cable WORKSHOP MANUAL TITAN Chapter 6 Electrical system EDITION 2018 Page 104...
Page 120: ...6 7 Wiring diagram WORKSHOP MANUAL TITAN Chapter 6 Electrical system EDITION 2018 Page 118...
Page 121: ...WORKSHOP MANUAL TITAN Chapter 6 Electrical system EDITION 2018 Page 119...
Page 122: ...WORKSHOP MANUAL TITAN Chapter 6 Electrical system EDITION 2018 Page 120...
Page 123: ...STIGA S p A Via del Lavoro 6 31033 Castelfranco Veneto TV Italy www stiga com...