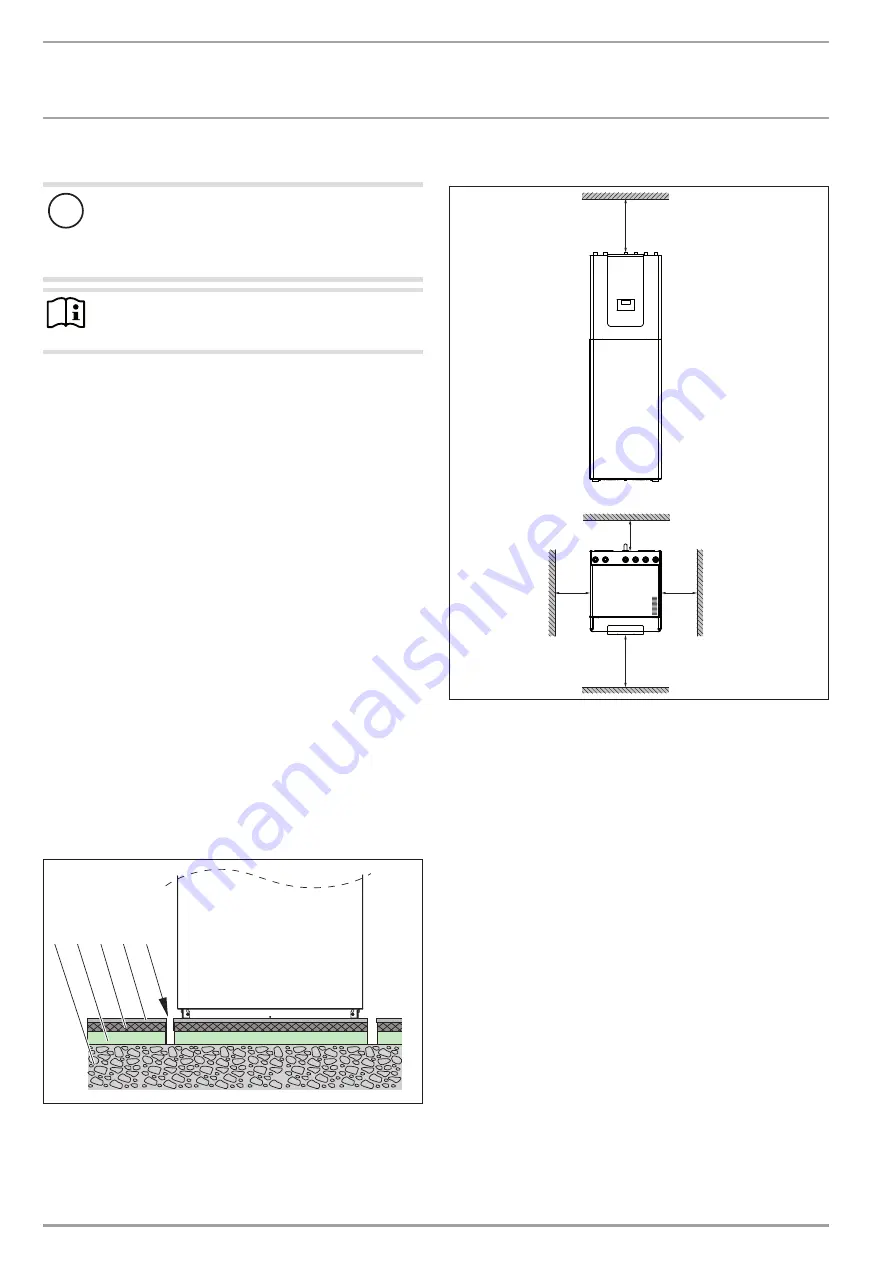
INSTallaTION
Preparation
8
| WPE-I HW 230 GB Premium
www.stiebel-eltron.com
8.2 Installation site
!
Material losses
f
Install the appliance only in rooms without a con-
stant ignition source (e.g. open flames, a live gas
appliance or an electric heater) or without open flue
boilers.
Note
The appliance is designed for indoor installation, except
in damp areas.
f
Never install the appliance directly below or next to bed-
rooms.
f
Implement pipe outlets through walls and ceilings with an-
ti-vibration insulation.
The room in which the appliance is to be installed must meet the
following conditions:
- No risk from frost
- The room must not be subject to a risk of explosions arising
from dust, gases or vapours.
- When installing the appliance in a boiler room together with
other heating equipment, ensure that the operation of other
heating equipment will not be impaired.
- The minimum volume of the installation room must be ob-
served (see chapter "Preparation / Safety concept").
- Load bearing floor (for the weight of the appliance, see chap-
ter "Specification / Data table").
f
Ensure that the safety valve for the brine circuit is installed
in the installation room. Alternatively, outdoor installation is
also possible.
f
Ensure that the substrate is level, even, solid and permanent.
f
For installation on floating screeds, make provisions for quiet
heat pump operation.
f
Isolate the installation surface around the heat pump by
means of a recess. After completing the installation, seal the
recess with a waterproof, sound insulating material, such as
silicone.
1 2 3
5
4
26
0
3
01
1
46
6
1 Concrete base
2 Impact sound insulation
3 Floating screed
4 Floor covering
5 Recess
8.3 Minimum clearances
≥500
≥200
≥1000
≥50
≥500
D
00000
33
99
2
f
Maintain the minimum clearances to ensure trouble-free op-
eration of the appliance and facilitate maintenance work.
Summary of Contents for WPE-I 04 HW 230 GB Premium
Page 31: ...Installation Specification www stiebel eltron com WPE I HW 230 GB Premium 31 ...
Page 45: ...www stiebel eltron com WPE I HW 230 GB Premium 45 NOTES ...
Page 46: ...46 WPE I HW 230 GB Premium www stiebel eltron com NOTES ...
Page 47: ...www stiebel eltron com WPE I HW 230 GB Premium 47 NOTES ...