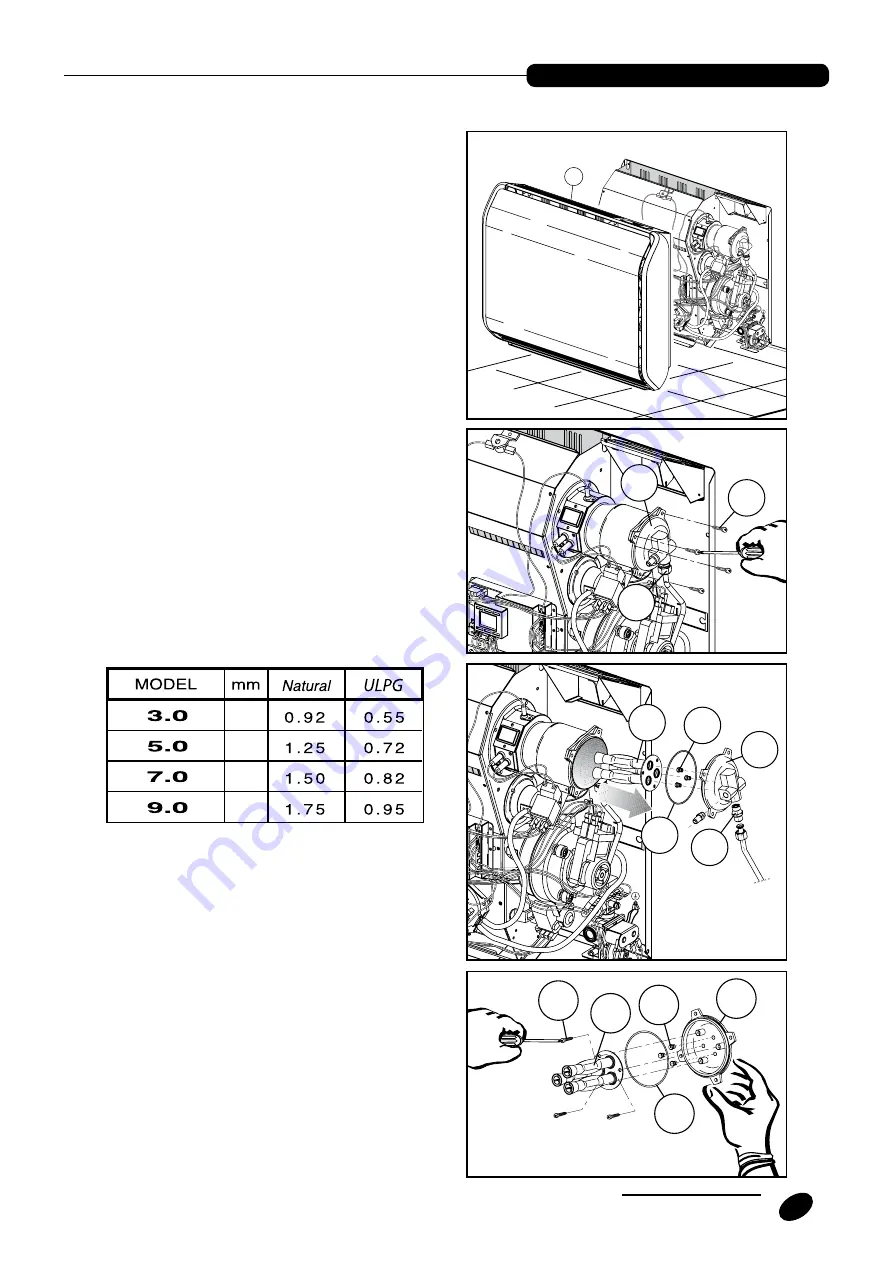
The appliance is preset for the methane gas fol-
lowing the technical label, but you can change at
with the supplied conversion kit.
The conversion has to be done only by Technical Service
person, the manufacturer, or by authorized persons
even if appliance has been already installed.
Shut down the appliance with the main button, and
then disconnect the electrical plug.
Proceed to the disassembling of the cover (1) like explai-
ned in the chapter assembling & disassembling the
cover.
-To make the conversion you have to disconnect the gas
from the nipples R3/8 (1) that is on the cap.
- Take off the screws M5 (2) then slip off the cap and the
burner group (3).
- Unscrew the screws (4) and the burner (5).
- Unscrew the 3 injectors (6) change them with the new
ones. Be real careful when you fasten the injector, check
on the injector that it has the right values as in the table.
-The injectors seal and the nipples 3/8”, are sealed
mechanically so you don’t need a gasket.
-Verifying that the values on the nozzles or as in the
table below.
-Reassemble the cap with the burner, in the same way
that you dissembled don’t forget the O-ring (7) that
goes around the cap.
-Proceed to the regulation as indicated in the Cap.
Regulation; verified the tubes gas connections capacity
that goes from the gas valve to the burner.
-Change the gas labels; seal the parts that you made the
regulation, after the conversion. Don’t forget the old
labels on the apparatus because it may cause problems.
GAS CONVERSION
1
2
3
1
3
5 6
7 1
3
6
5
4
7
23
CUSTOMER SERVICE
Summary of Contents for Stratos Brahma 3.0
Page 1: ...Gas Room Heater Stratos Brahma...
Page 7: ...7 GENERAL STRUCTURE...
Page 9: ...9 GENERAL ELECTRICAL SCHEME...
Page 31: ...31 CUSTOMER SERVICE...
Page 32: ...USEFUL INFORMATION 32 CUSTOMER SERVICE...
Page 33: ...33 NOTE NOTE...
Page 36: ...35200145 Rev 10...