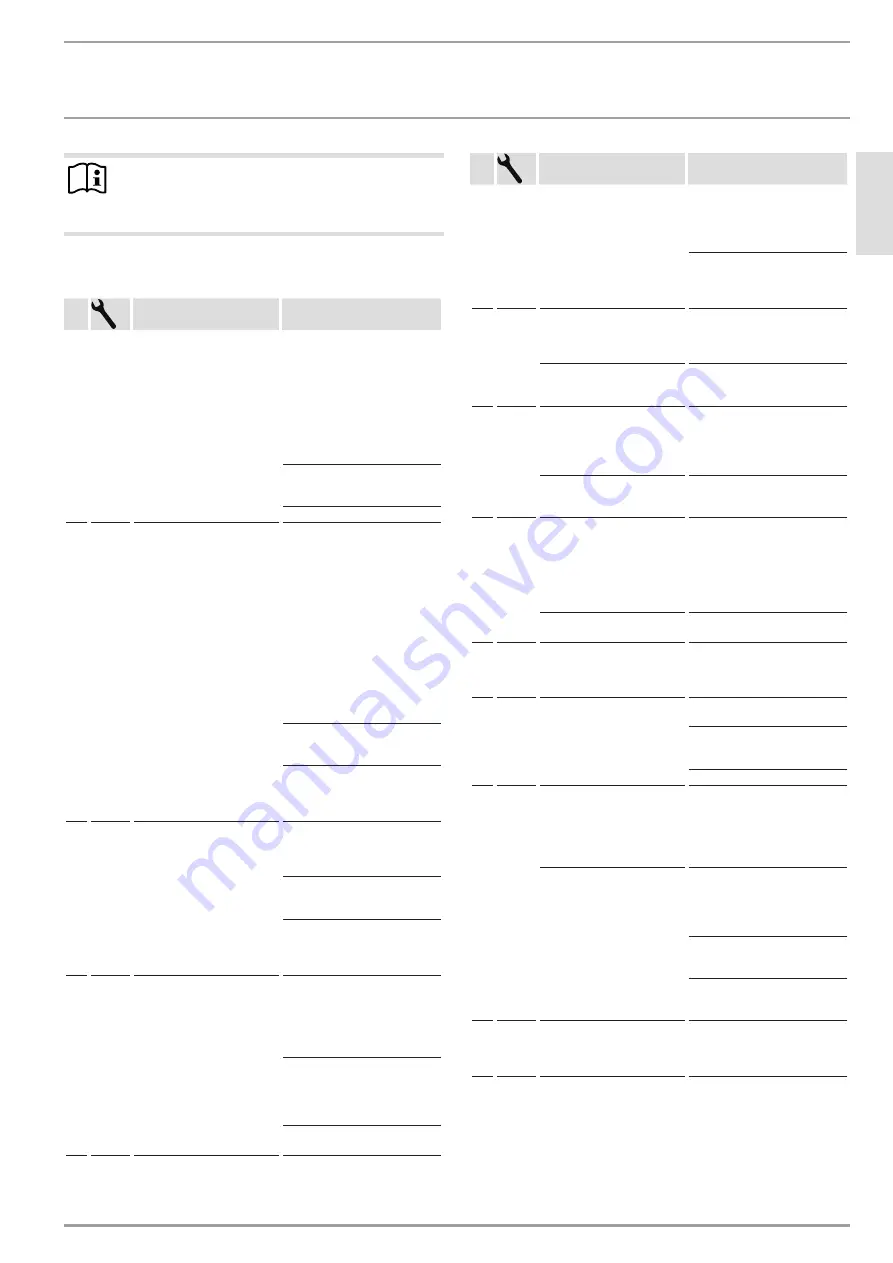
iNSTAllATiON
Troubleshooting
www.stiebel-eltron.com
SHP-A 220-300 Plus |
23
EN
GL
ISH
Note
Refit the appliance cover after completing your work. See
chapter "Maintenance and cleaning / Fitting the appliance
cover").
14.1 Fault codes
fault description
remedy
2
perma-
nently
on
The sensor at the cylinder top
is faulty. The actual temper-
ature display switches from
the cylinder top sensor to the
integral sensor. The appliance
continues to heat without any
loss of comfort. The mixed
water volume cannot be
calculated and is displayed
as "- -".
Check that the plug is seated
correctly.
Measure the resistance of the
sensor and compare it with the
resistance table.
Install the replacement sensor.
4
perma-
nently
on
The integral sensor is faulty.
In the event of a faulty in-
tegral sensor, the integral
sensor is set to the value of
the sensor at the cylinder top,
and amount of mixed water
is calculated using this value.
The appliance continues to
heat with a reduced start
hysteresis.
A mixed water volume is
still calculated, based on the
assumption that the cylinder
top temperature is reached
throughout the DHW cylinder.
Check that the plug is seated
correctly.
Measure the resistance of the
sensor and compare it with the
resistance table.
Install the replacement sensor.
In the service menu, use param-
eter "IE" to switch to standby
mode.
6
flashing The sensor at the cylinder
top and the integral sensor
are faulty. The appliance no
longer delivers heat.
Check that the plug is seated
correctly.
Measure the resistances of the
sensor and compare them with
the resistance table.
Install the replacement sensor.
In the service menu, use param-
eter "IE" to switch to standby
mode.
8
flashing
The appliance has ascer-
tained that the DHW cylinder
has not been heated within
the maximum temperature
increase time, despite there
being a demand.
Check if a DHW circulation line
is installed and whether it is
insulated. The total power loss is
greater than the heating output
of the appliance.
Check if a DHW circulation pump
is installed and whether it is
controlled according to temper-
ature or time. If required, install
a corresponding control unit.
Check the refrigerant circuit for
leaks.
fault description
remedy
16
perma-
nently
on
A short circuit of the im-
pressed current anode has
occurred or the protective
anode is faulty.
Check the cables and relevant
plug-in connections of the im-
pressed current anode according
to the connection diagram and
replace faulty cables.
Check the impressed current
anode in the heating element/
anode assembly and replace if
required.
32
flashing
The appliance is being op-
erated with a partially filled
DHW cylinder. The appliance
does not heat up.
Fill the appliance's DHW cylin-
der. The fault code disappears
and the appliance starts.
The anode current is inter-
rupted. The appliance does
not heat up.
Check the contacts of the im-
pressed current anode.
64
perma-
nently
on
The defrost temperature has
not yet been reached after
the maximum defrost time
has lapsed. The compressor
is faulty.
Check the position of the evapo-
rator sensor in the evaporator.
The temperature of the intake
air is below the lower appli-
cation limit.
Wait for higher ambient temper-
atures. Ensure that values do not
fall below the application limit.
128
perma-
nently
on
There is no communication
between the controller and
the programming unit. The
most recently selected set
values are active. The ap-
pliance continues to deliver
heat.
Check that the plug is seated
correctly, and if required, re-
place the connecting cable.
Replace the programming unit
PCB.
256
flashing
Manually activated emer-
gency mode (only electric
emergency/booster heater
enabled)
See chapter "Appliance descrip-
tion / Emergency mode".
E 2 flashing The temperature sensor on
the evaporator is faulty.
Check that the plug is seated
correctly.
Measure the resistance of the
sensor and compare it with the
resistance table.
Replace the sensor.
E 16
perma-
nently
on
The high pressure limiter
has responded. Compressor
heating mode is temporarily
blocked. Compressor heating
mode will continue as soon as
the pressure has normalised.
No action required.
After consultation with the cus-
tomer, reduce the set temper-
ature if required. Increase the
charge level with the program-
ming unit.
Check the offset of the integral
sensor to the cylinder top sensor
and adjust if required.
Check the high pressure switch-
ing point and replace the high
pressure switch if required.
E 32
perma-
nently
on
An electrical fault has oc-
curred.
A1/X2 : Check whether the power
supply has been interrupted.
Then reset the fault with the
corresponding menu option.