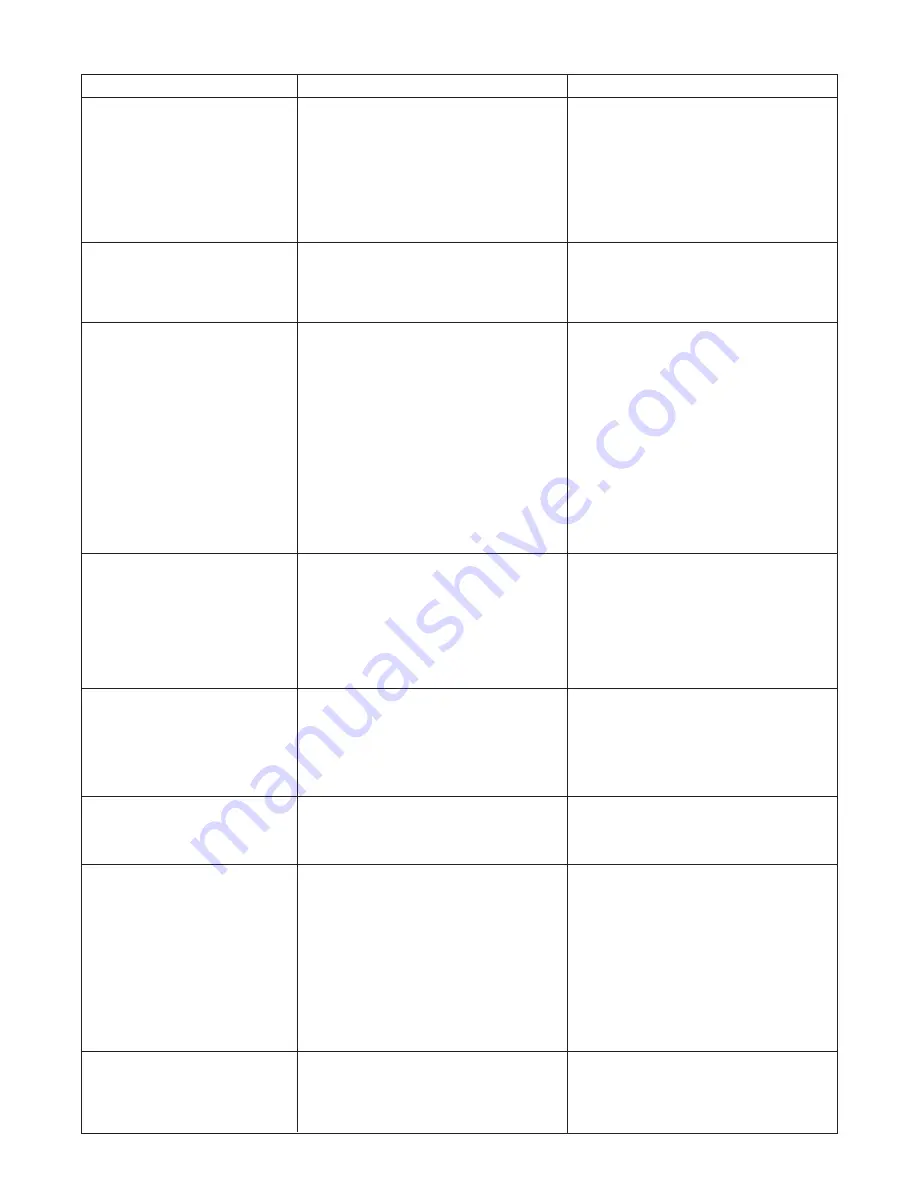
22
1. Loose wire connections at gas valve or
thermostat.
2. Excessive thermostat heat anticipation.
3. Unit cycling on high limit.
4. Poor thermostat location.
5. Draft on Pilot.
6. Defective ignitor control.
1. Power ventor wheel loose.
2. Power ventor wheel dirty.
3. Power ventor wheel rubbing housing.
4. Bearings are dry.
1. Main gas valve off.
2. Pilot adjustment screw turned too low on
combination main gas valve.
3. Air in gas line.
4. Incorrect lighting procedure.
5. Dirt in pilot orifice.
6. Extremely high or low gas pressure.
7. Defective spark cable.
8. Drafts around unit.
9. Pilot valve not opening (faulty wiring).
10. Pilot element not glowing or no spark
(faulty wiring).
11. Defective gas valve.
1. Loose wiring.
2. Defective motor overload protector or
defective motor.
3. Defective fan switch.
1. Fan switch heater element improperly
wired.
2. Defective fan switch.
3. Motor protector cycling ON and OFF.
4. Motor not properly oiled.
1. Improperly wired fan control.
2. Main burners not lighting while
thermostat calls for heat.
3. Defective fan switch.
1. Incorrect gas input.
2. Heater undersized.
3. Thermostat malfunction.
4. Heater cycling on high limit .
1. Thermostat malfunction.
2. Heater runs continuously.
Table 6 - Tubular Propeller Trouble Shooting Guide (continued)
1. Tighten all electrical connections.
2. Adjust thermostat heat anticipator for
longer cycles. Refer to “Operation”.
3. Check for proper air supply across heat
exchanger.
4. Relocate thermostat. (Do not mount
thermostat on unit).
5. Eliminate drafts. Refer to “Installation”.
6. Replace ignitor.
1. Replace or tighten.
2. Clean power ventor wheel.
3. Realign power ventor wheel.
4. Oil bearings on power ventor motor.
(Refer to label on motor).
1. Open all manual gas valves.
2. Increase size of pilot flame. Refer to
“Operation”.
3. Purge air from gas line.
4. Follow lighting instruction label adjacent to
gas valve.
5. Remove pilot orifice. Clean with compressed
air or solvent. (Do not ream).
6. Refer to “Operation”.
7. Check thermocouple connection, and
replace if defective.
8. Eliminate drafts. Refer to “Installation”.
9. Inspect and correct wiring.
10. Inspect and correct ignition system wiring.
See symptoms W, X, & Y.
11. Replace gas valve.
1. Check and tighten all wiring connections per
diagrams. See “Electrical Connections”.
2. Replace motor.
3. Check for 24V across H terminals on fan time
delay switch. If 24V is present, jumper terminals
numbered 1 and 3. If motor runs, the fan switch
is defective and must be replaced. If 24V is not
present, check wiring per diagrams.
1. Be sure fan switch heater terminals
are connected per diagrams.
2. Replace fan switch.
3. Check motor amps against motor name
plate rating, check voltage, replace fan
motor if defective.
4. Refer to label on motor.
1. Check all wiring.
2. Refer to H or N symptoms.
3. Replace fan switch.
1. Refer to “Operation”.
2. This is especially true when the heated
space is enlarged. Have the heat loss
calculated and compare to heater output
(80% of input). Your gas supplier or installer
can furnish this information. If heater is
undersized, add additional heaters.
3. Replace thermostat.
4. There should be NO ducts attached to the
front of this heater. Check air movement
through heat exchanger. Check voltage to
fan motor. Clean fan blade and heat
exchanger and oil fan motor.
1. Replace thermostat.
2. Check wiring per diagrams; Check operation
at valve. Look for short (such as staples
piercing thermostat wiring) and correct:
Replace gas valve, Refer to “Operation”.
SYMPTOMS
POSSIBLE CAUSE(S)
CORRECTIVE ACTION
L. Rapid burner cycling.
M. Noisy power ventor.
N. Pilot will not light or will not
stay lit.
O. Fan will not run.
P. Fan motor turns on and off while
burner is operating.
Q. Fan motor will not stop.
R. Not enough heat.
S. Too much heat.