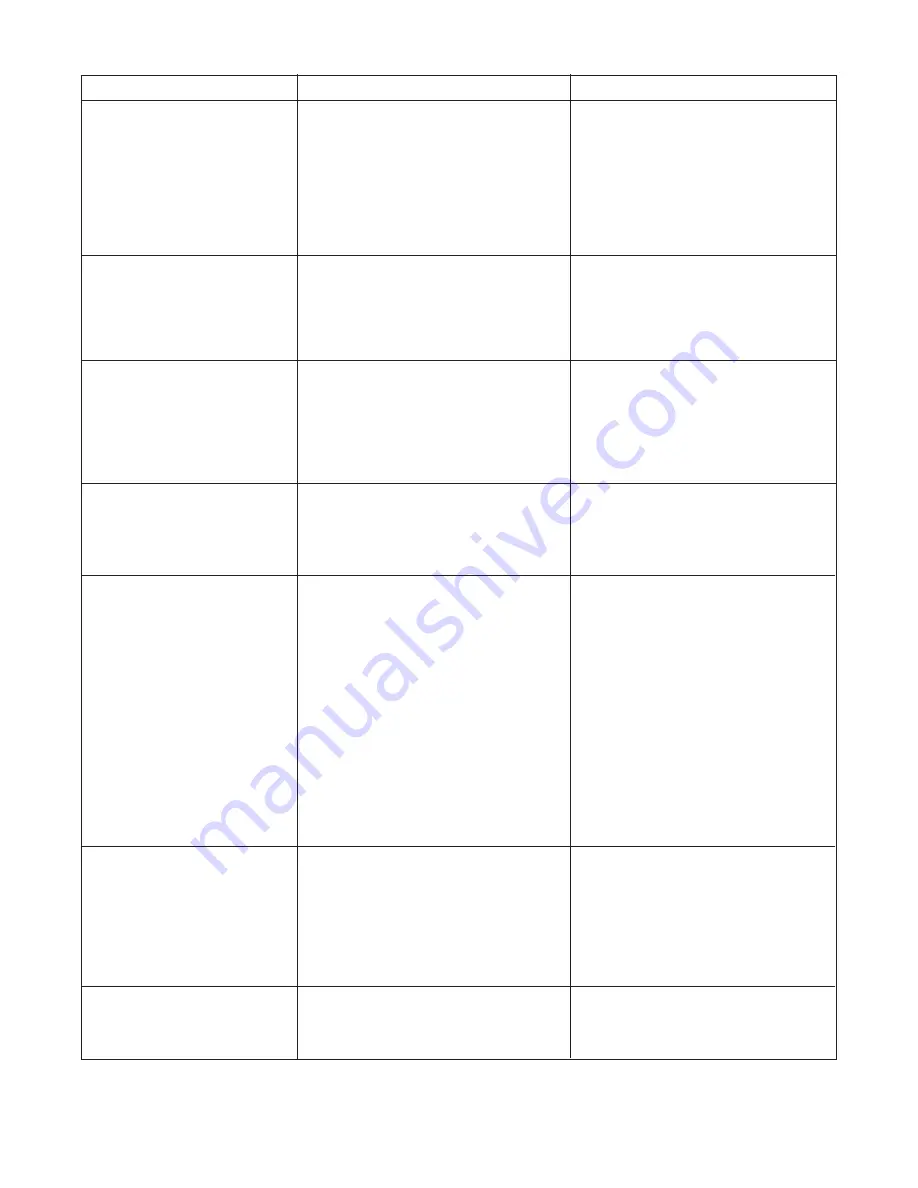
1. Loose S8600 connections.
2. Improper gas pressure.
3. Is spark in pilot gas stream?
4. No pilot gas — do not use match to
test - presence of gas is easily
detected by the odor.
1. Loose S8600 connections.
2. Cracked or broken sensor ceramic.
3. Check sensor/spark lead for continuity.
4. Measure 24 volts from term. MV to
term.
MV/PV.
1. Vertical run of fl ue is too short.
2. Unit is overfi ring.
3. Air fl ow too low
4. Defective
switch.
1. Power venter wheel loose.
2. Power venter wheel dirty.
3. Power venter wheel rubbing housing.
4. Bearings are dry.
1. Loose
wiring.
2. Defective motor overload protector or
defective
motor.
3. Defective power venter relay.
1. Fan relay heater element improperly
wired.
2. Defective venter relay switch.
3. Motor overload protector cycling on
and
off.
4. Motor not properly oiled.
1. Improperly wired venter relay.
2. Main burners not lighting while
thermostat calls for heat.
3. Defective venter relay.
1. Check all connections, term.
PV feeds 24V to pilot valve.
2. Check pressure — pressure that is
either too high or too low may cause
a
problem.
3. Spark should arc from electrode.
4. Check pilot line for kinks. Ensure
there are no drafts.
1. Check connections-term. MV feeds
main
valve.
2. Replace pilot assembly.
3. Replace if needed.
4. If present, replace main valve; if not,
replace S8600 Igniter.
1. Lengthen vertical run of fl ue pipe
(see
venting).
2. Burner orifi ce may be too large:
verify/replace if req'd.
3. Increase air fl ow; check fan size.
Check for proper voltage.
4. Replace.
1. Replace or tighten.
2. Clean power venter wheel.
3. Realign power venter wheel.
4. Oil bearings on power venter motor.
(Refer to label on motor).
1. Check and tighten all wiring connec-
tions per diagrams. Thermostat wires
tagged "W" and "G" must be
connected together (unless special
thermostats are used; if so, see
thermostat wiring diagram). See
electrical
connections.
2. Replace
motor.
3. Check for 24V across 1 and 3
terminals on fan relay. If 24V is
present, jumper terminals numbered
2 and 4. If motor runs, the relay
is defective and must be replaced.If
24V is not present, check wiring per
diagrams.
1. Be sure venter relay heater terminals
are connected per diagrams.
2. Replace venter relay.
3. Check motor amps against motor
name plate rating, check voltage,
replace power venter motor if
defective.
4. Refer to label on motor.
1. Check all wiring.
2. Refer to H & N symptoms.
3. Replace venter relay.
Power Vented Propellers Troubleshooting Guide
SYMPTOMS
POSSIBLE CAUSE(S)
CORRECTIVE ACTION
W. Spark present but pilot does
not
light.
X. Pilot lights — Main valve
does not energize.
Y. Hi-Limit switch tripping.
Z. Noisy power venter.
AA. Power venter will not run.
BB. Power venter motor turns
on and off while burner is
operating.
CC. Power Ventor motor will not
stop.
21
Summary of Contents for QVEF 100 M
Page 12: ...12 Figure 10A VENTING continued Figure 10B...
Page 13: ...13 Figure 10C VENTING continued Figure 10D...
Page 26: ...NOTES 26...
Page 28: ......