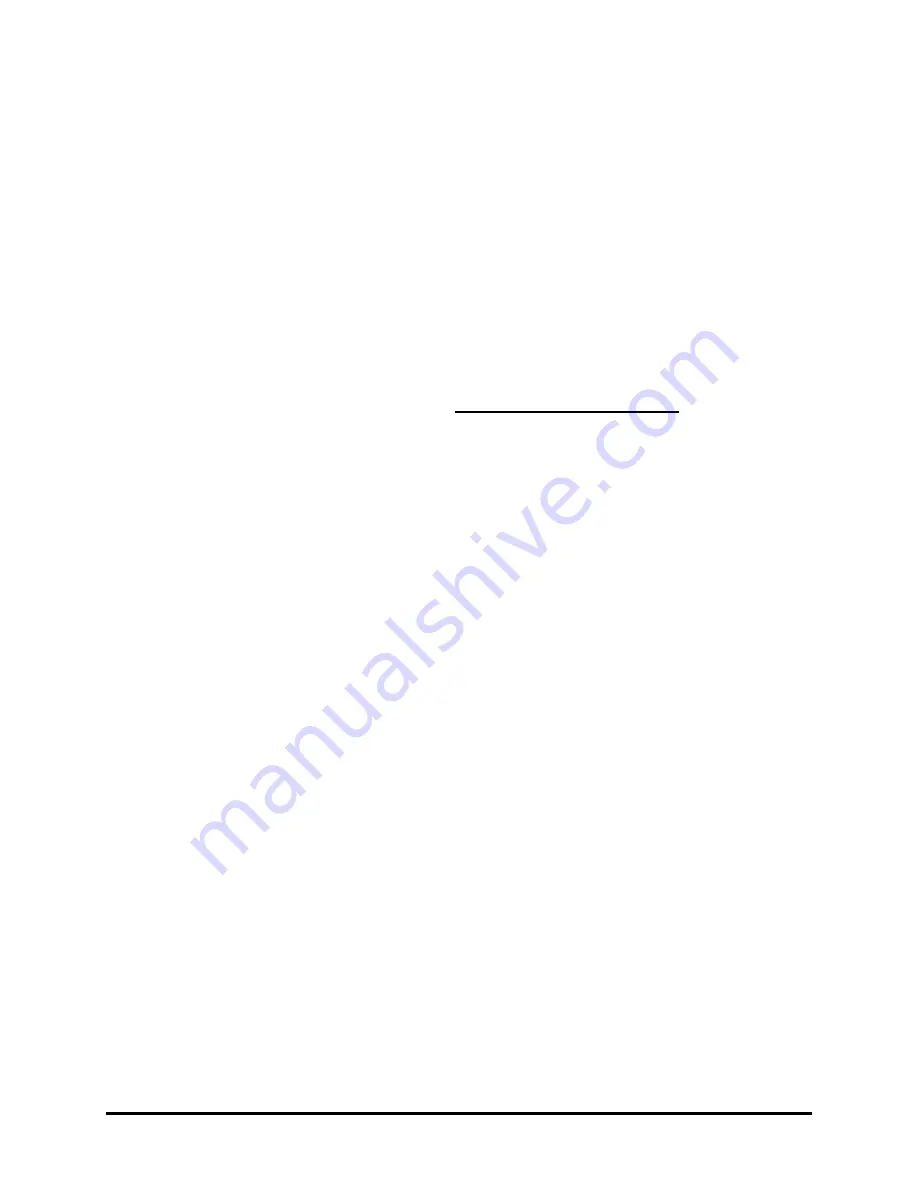
For further information on granulator safety, installation, and
operation, see the
American National Standard for Plastics
Machinery
⎯
Granulators, Pelletizers, and Dicers Used for Size
Reduction of Plastics
⎯
Construction, Care, and Use
. ANSI
B151.11-1982.
Cumberland has long recognized the importance of safety and has
designed and manufactured its equipment with operator safety as a
prime consideration. We expect you, as a user, to abide by the
foregoing recommendations in order to make operator safety a
reality.
SAFETY IS NO ACCIDENT
1-2 Safety
Procedures
1-2-1 Guidelines for Moving the Granulator
To lift and move the granulator safely and correctly, cover any
sharp corners or edges, and use the type of equipment that has the
most appropriate features and capacity.
Before lifting, check that there are no items that could fall during
lifting.
Before positioning the granulator, check that the floor is level and
is strong enough to support the load, that there is adequate space in
the installation area to allow the movement of equipment necessary
to the task and to enable any necessary maintenance work to be
carried out unhindered.
1-2-2 Clearing a Jammed Cutting Chamber
1.
Disconnect and lockout power.
2.
Be certain that the rotor is motionless.
3.
Open the front panel and remove the bin.
4.
Unscrew the screw knob, which keeps the hopper and screen
cradle in place.
5.
Remove the screen.
Page 11 of 54
Summary of Contents for BP810
Page 1: ......
Page 2: ......
Page 3: ......
Page 4: ......
Page 5: ......
Page 7: ......
Page 18: ......
Page 20: ......
Page 40: ......
Page 44: ......
Page 45: ...Figure 16 Cutting Chamber Vertical Cross Section DRAWING CA039060S2 Page 45 of 54...
Page 46: ...Figure 17 Cutting Chamber Longitudal Cross Section DRAWING CA039060S1 Page 46 of 54...
Page 47: ...Figure 18 Cutting Chamber Front View DRAWING CA039060S3 Page 47 of 54...
Page 48: ...Figure 19 Cutting Chamber Rear View DRAWING CA039060S4 Page 48 of 54...
Page 49: ...9 Typical Wiring Diagram Page 49 of 54...
Page 50: ...DRAWING D05991100000 Page 50 of 54...
Page 51: ......
Page 53: ......
Page 54: ......