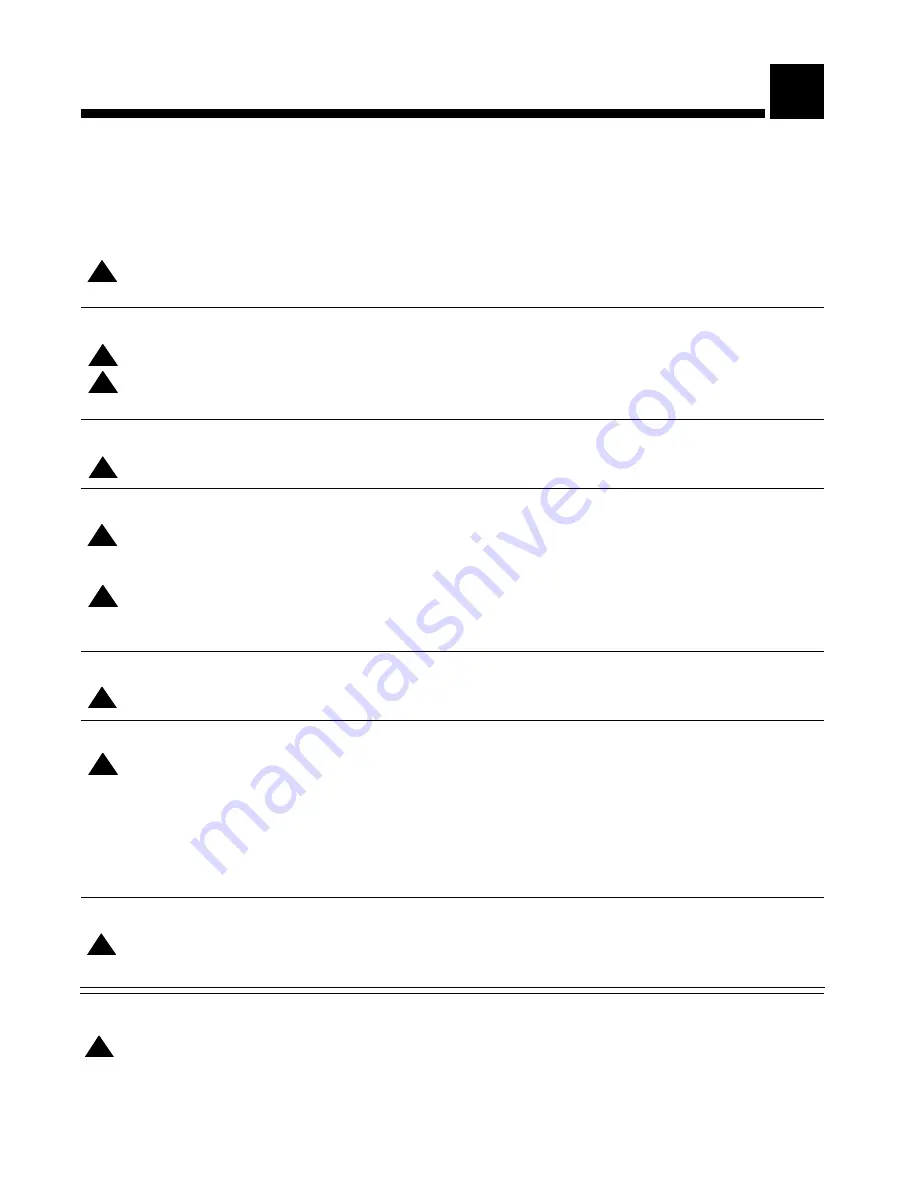
1-1
122990-172
Summary of Warnings and Cautions
Uncrating/Installation Instructions
The following is a listing of safety precautions which must be observed when uncrating, installing, and checking this
equipment. WARNINGS indicate the potential for danger to personnel and CAUTIONS indicate the potential for
damage to equipment. These precautions are repeated (in whole or in part), where applicable, throughout the
instructions.
WARNING - LACERATION/EYE INJURY HAZARD:
WHEN REMOVING BANDS, wear eye protection and always use a tool specifically designed to cut the bands.
The bands used to secure this container can cause personal injury when cut and tension is released.
WARNING - PERSONAL INJURY AND/OR EQUIPMENT DAMAGE HAZARD:
WHEN MOVING WASHER/DISINFECTOR,
use a forklift. Do not use the doors or door handles for lifting.
TO TILT THE WASHER/DISINFECTOR,
more than one person is required. Washer/disinfector weighs
approximately 1000 lbs (454 kg).
WARNING - LACERATION HAZARD:
WHEN REMOVING BOLTS, wear gloves to protect your hands.
WARNING - BURN HAZARD:
WHEN CHECKING AUTOMATIC STOP FEATURE,
open chamber door slowly
and wear gloves and
face protection. Hot water/steam may be sprayed through door opening if door is opened while
washer is operating.
EXCEPT FOR AN EMERGENCY, do not open door when cycle is in progress. In an emergency, first stop cycle
by pressing the STOP touch pad and wait for water flow to stop. Wear protective gloves and face shield
whenever reaching into the chamber.
WARNING - FALL HAZARD:
TO PREVENT FALLS, keep floor dry. Promptly clean up any spills or drippage.
WARNING - CHEMICAL BURN HAZARD:
WASHER/DISINFECTOR DETERGENTS ARE CAUSTIC and can cause adverse effects to exposed tissues.
Do not get in eyes, on skin or attempt to ingest by mouth.
•
Read and follow the precautions and instructions on the detergent label and in the Material Safety Data
Sheet (MSDS) prior to handling the detergent, refilling the detergent container or servicing the detergent
injection pump and lines.
•
Wear protective gloves, face shield and clothing whenever handling the detergent or servicing the
detergent injection pump and lines.
WARNING - ELECTRICAL SHOCK HAZARD:
FASTENERS AND STAR WASHERS ARE USED to ensure protective bonding continuity. Always re-
install any star washers which may have been removed during installation or servicing.
CAUTION - POSSIBLE EQUIPMENT DAMAGE:
Leave door closed to prevent counterweight from dropping to bottom of guiding box.
!
!
!
!
!
!
!
!
!
LISTING OF WARNINGS, CAUTIONS AND
SYMBOLS
1
!