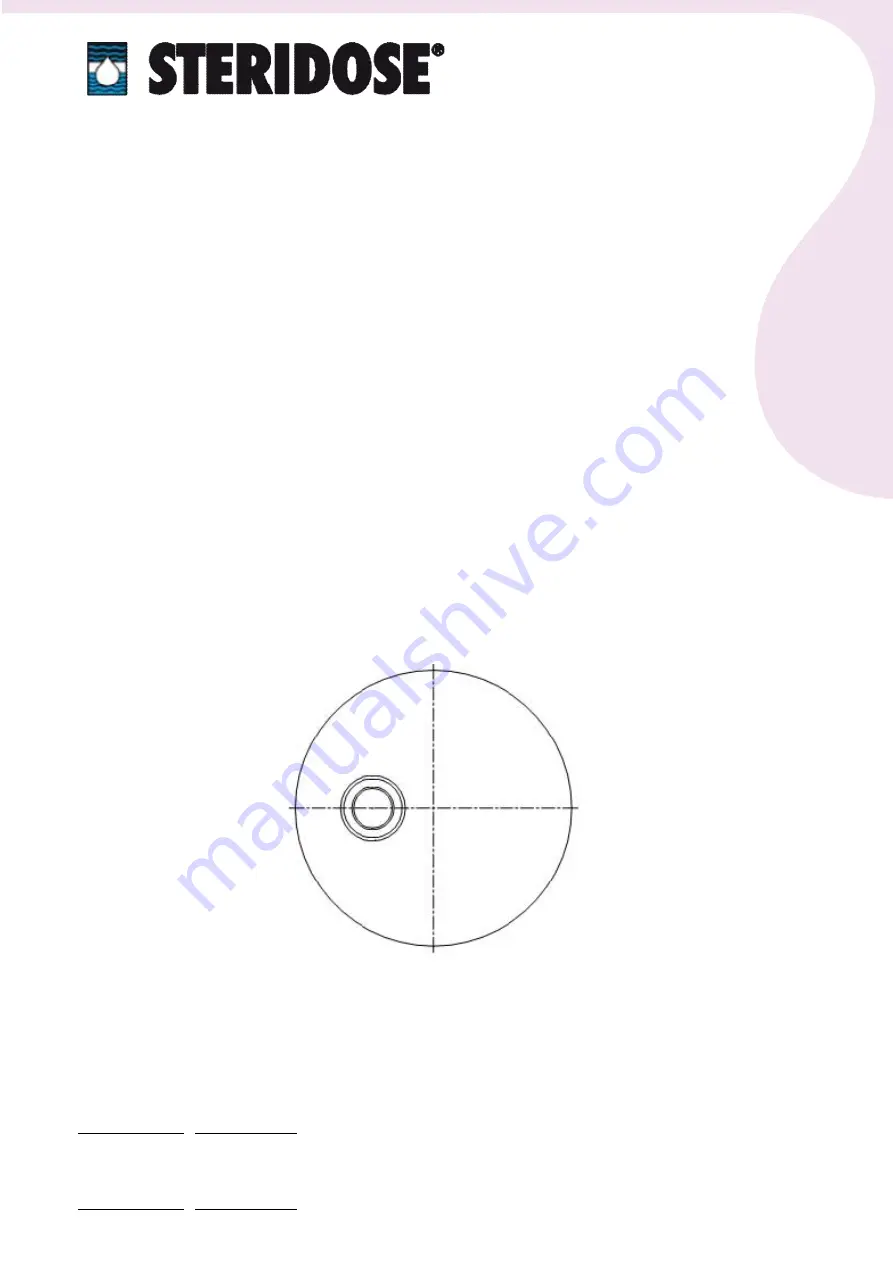
4
STERIDOSE SALES
Head Office
Himmelsbodavägen 7 · P.O.Box 120 · SE-147 22 TUMBA · SWEDEN
Phone: +46-8 449 99 00 · Fax: +46-8 449 99 90
[email protected] · www.steridose.com
Regional Office
5020 World Dairy Drive · Madison, WI 53718 · USA
Phone: +1-608 229 5225 · Fax: +1-608 227 9599
[email protected] · www.steridose.com
2. General
The Steriflange may be welded into the vessel before it’s welded together. It can also be welded in
an already finished vessel.
It is vital that all other welding on the lower gable end is completed before making a hole for the
flange. Examples of such welding that may be required are bottom outlet valves, connection
adapters for sensors and sample ports etc.
3. Positioning and Orientation of Steriflange
3.1 Orientation of Steriflange
In order to connect pipe, etc. into the Steriflange, ensure that no other equipment will be in conflict
with the assembled parts. Also make sure that there's enough space to mount/dismount the locking
ring.