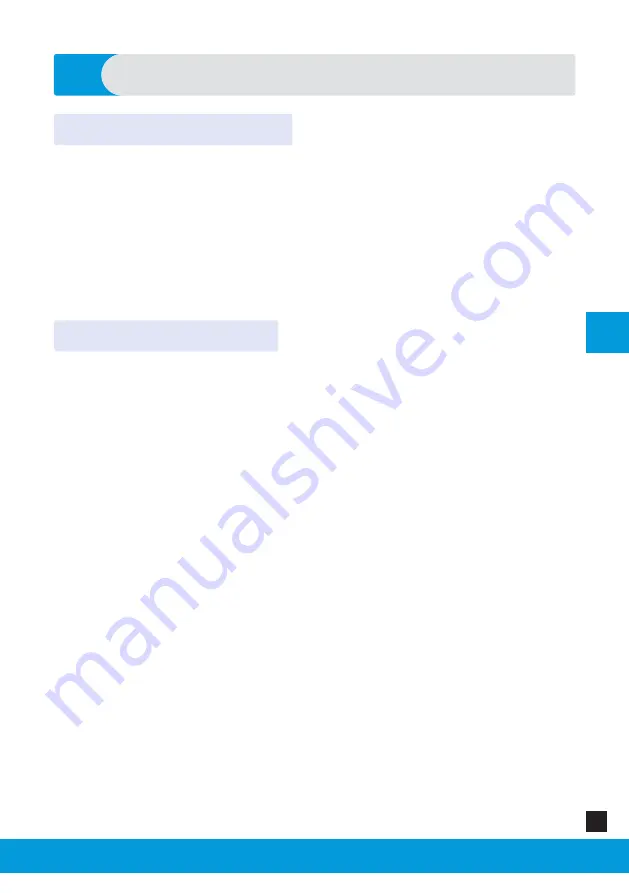
EN
Myo Kinisi van Steeper, distributeur Loth Fabenim B.V.
Myo Kinisi Technical Manual
25
Myo Kinisi Mode Overview
17
Single Site: Auto Close
A signal rising above the ‘ON Level’ threshold will open the hand. When the signal
drops below the ‘ON Level’ the hand will close, regardless of the speed at which it
is removed.
There is an option to invert the functions in this mode, so that a signal rising above
the ‘ON Level’ threshold will close the hand and when the signal drops below the ‘ON
Level’ the hand will open.
Dual Site: Open/Close Signal - Default Mode
This mode uses 2 inputs to provide proportional or threshold control over opening
and closing the terminal device.
Default settings are:
Proportional Control
Maximum Opening/Closing Speeds
Highest Electrode Mode
Auto-Grip enabled
Maximum Pulses Count of 3
An input signal must pass the ‘ON Level’ threshold to elicit movement in a respective
direction. The method for changing direction of movement is ‘Highest’ by default,
meaning that the largest signal will take priority to determine the direction of the
hand. When the ‘First Signal’ option is selected, the first electrode to increase above
its ‘ON Level’ threshold will determine the direction of travel. If the ‘Close Priority’
option is selected, a valid close signal will take priority even if the hand is opening.
This can be altered by ‘Electrode Mode’ selection. If the signals from both inputs
drop below their independent ‘ON Level’ thresholds the device will stop moving. The
grip force achieved is determined by the strength and duration of the close signal.
The grip can be incrementally increased by maintaining, or pulsing, the close signal
above the ‘ON Level’ threshold to the ‘maximum pulse count’. This is set to 3 pulses
by default.
17.1 Mode 0: ‘AUTO CLOSE’
17.2 Mode 1: ‘DUAL ELEC’