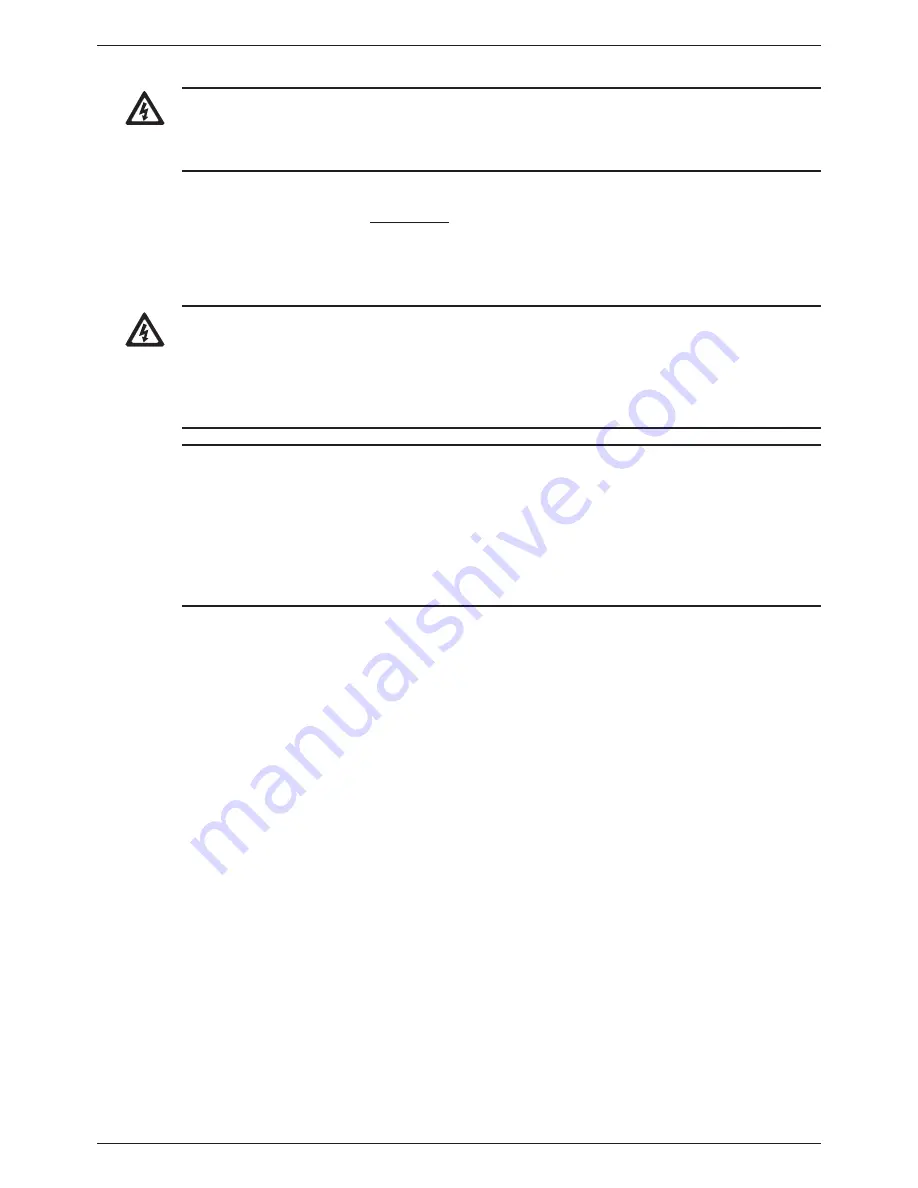
18
745.089 | 11.30
EN
7
Deinstallation and disposal
Danger
Risk of death by electrocution!
• Disconnect the device from the power supply before opening the casing.
• All work on an open device must be performed by professional personnel.
1. Deinstall the controller in the reverse sequence to installation; more information on
this is provided in the
Installation
section.
2. Dispose of the device in accordance with the local regulations.
8 Troubleshooting
Danger
Risk of death by electrocution!
• Immediately disconnect the device from the mains supply when it can no longer be
operated safely, e.g. in the case of visible damage.
• Disconnect the device from the mains power before opening the case.
• All work on an open device must be performed by professional personnel.
Notes
The controller is a quality product, conceived for years of continuous trouble-free opera-
tion. Observe the following points:
• Faults are often caused by connected components and not by the controller.
• The following notes on fault identification indicate the most common causes of
faults.
• Only return the controller when you are absolutely sure that none of the problems
listed below is responsible for the fault.
Summary of Contents for TF B001
Page 23: ...23 745 089 11 30 EN Notes...
Page 24: ...24 745 089 11 30 EN 745089...