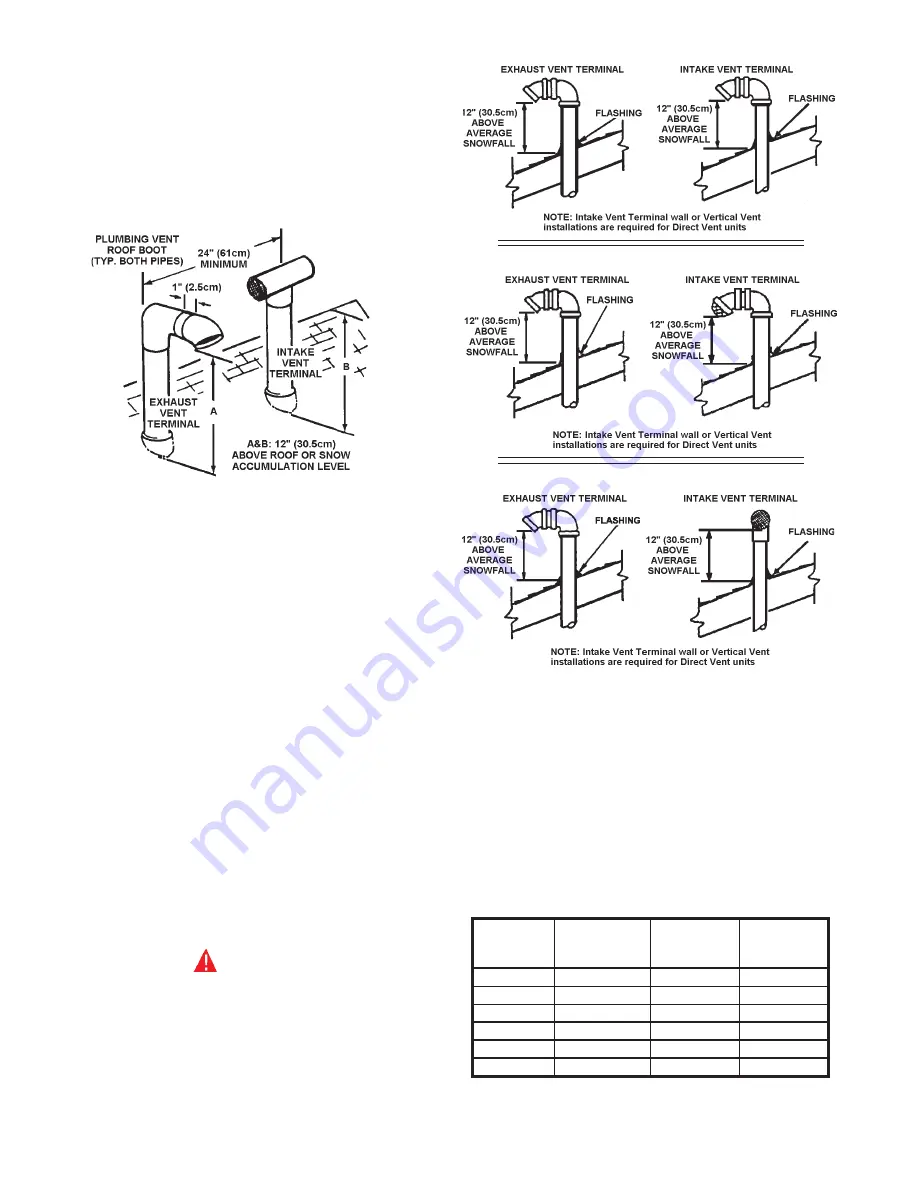
10
FIGURE 12
1. Plan the route of the vent system from the vent termination to the planned
location of the appliance. Layout the total vent system to use the minimum
of vent pipe and elbows possible.
2. The installer may add up to a MAXIMUM OF FIFTY (50) EQUIVALENT
FEET (15.2 m) of pipe to the exhaust venting arrangement. This addition
of FIFTY (50) EQUIVALENT FEET (15.2 m) of pipe on both the intake
venting arrangement and exhaust venting arrangement must include
any 3" PVC elbows which equals (5) EQUIVALENT FEET (1.5 m) of
pipe.
Table 2. VENT LENGTH TABLE
3. The intake vent termination and the exhaust vent termination must
penetrate the same side of roof.
4. The center line of the intake vent termination and the center line of the
exhaust vent termination must be no closer than 24" (61cm).
5. The intake vent terminal and the exhaust vent terminal must be oriented
facing downward and the same direction.
The specifications are displayed in Figure 11 & 12.
NOTE: Exhaust vent terminal is installed using the same procedure.
FIGURE 11
INSTALLATION SEQUENCE
NOTE: BEFORE BEGINNING INSTALLATION OF ANY VENT PIPE, READ
“VENT PIPE PREPARATION” SECTION ON PAGE 11.
1. After the points of termination have been determined, use the cover
plates as templates to mark the holes for the vent pipes to be inserted
through the roof.
2. Drill a pilot hole approximately 1/4" (6 mm) outside of the marked circle.
This pilot hole is used as a starting point for a saws-all or sabre saw
blade. Cut around the marked circle staying approximately one quarter
inch outside the line. (This will allow the vent pipe to easily slide through
the opening). The resulting gap will be covered by the roof
boot/flashing.
3. Suspend the pipe through the center of the hole using proper support.
4. Slide roof boot or equivalent flashing over pipe and secure roof boot
equivalent flashing to roof.
5. Seal around flashing.
6. Terminate intake terminal and exhaust vent terminal facing down as
shown in Figure 12.
INSTALLATION OF VENT SYSTEM
WARNING
THE OPTIONAL INTAKE VENTING ARRANGEMENT AND THE EXHAUST
VENTING ARRANGEMENT MUST BE INSTALLED TO RUN DIRECTLY TO THE
OUTDOORS AND NOT IN ANY WAY BE CONNECTED TO ANOTHER VENTING
SYSTEM (I.E. FURNACE, DRYERS OR SPACE HEATERS). IT IS CRUCIAL
THAT THE VENTING ARRANGEMENT BE KEPT SEPARATE FROM OTHER
VENTING SYSTEMS. IF THIS WARNING IS IGNORED, AND THE SYSTEM IS
VENTED INCORRECTLY, IT MAY CAUSE IMPROPER OPERATION, FIRE,
EXPLOSION, OR ASPHYXIATION.
SUF 100 150/199
SUF 100 240 ONLY
SUF 60 120 ONLY
VERTICAL VENT TERMINATION
SUF 100 240 MODELS ONLY
Number
3"
3"
4"
of 90°
Minimum
Maximum
Minimum
Elbows
Pipe (Ft./M.)
Pipe (Ft./M.)
Pipe (Ft./M.)
ONE (1)
7/2
45/13.7
115/35
TWO (2)
7/2
40/12.2
110/33.5
THREE (3)
7/2
35/10.7
105/32
FOUR (4)
7/2
30/9.1
100/30.5
FIVE (5)
7/2
---
95/29
SIX (6)
7/2
---
90/27.4
Summary of Contents for SUF 100 150NE
Page 31: ...31...