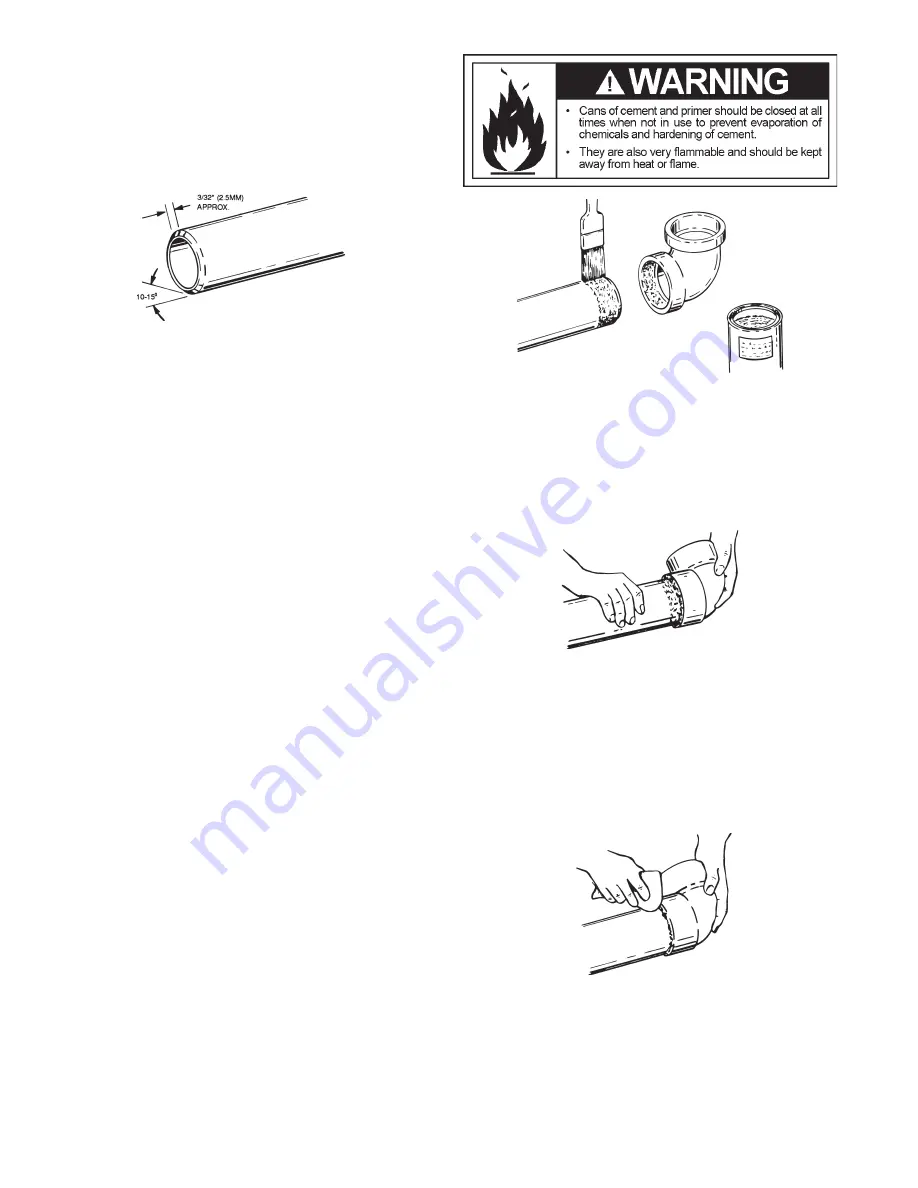
32
b. deburring
Use a knife, plastic pipe deburring tool, or file to remove burrs from
the end of small diameter pipe. Be sure to remove all burrs from
around the inside as well as the outside of the pipe. A slight chamfer
(bevel) of about 10°-15° should be added to the end to permit easier
insertion of the pipe into the end of the fitting. Failure to chamfer the
edge of the pipe may remove cement from the fitting socket, causing
the joint to leak.
step b
C. Test dry fit of the joint
Tapered fitting sockets are designed so that an interfaced fit should
occur when the pipe is inserted about 1/3 to 2/3 of the way into the
socket. Occasionally, when pipe fitting dimensions are at the tolerance
extremes, it will be possible to fully insert dry pipe to the bottom of
the fitting socket. When this happens, a sufficient quantity of cement
must be applied to the joint to fill the gap between the pipe and fitting.
The gap must be filled to obtain a strong, leak-free joint.
d. Inspection, cleaning, priming
Visually inspect the inside of the pipe and fitting sockets and
remove all dirt, grease or moisture with a clean dry rag. If wiping
fails to clean the surfaces, a chemical cleaner must be used.
Check for possible damage such as splits or cracks and replace
if necessary.
depth-of-entry
Marking the depth of entry is a way to check if the pipe has
reached the bottom of the fitting socket in Step F. Measure
the fitting depth and mark this distance on the pipe O.D. You
may want to add several inches to the distance and make a
second mark as the primer and cement will most likely destroy
your first one.
Apply primer to the surface of the pipe and fitting socket with
a natural bristle brush. This process softens and prepares the
PVC or CPVC for the solvent cementing step. Move quickly and
without hesitation to the cementing procedure while the surfaces
are still wet with primer.
e. application of solvent cement
• Apply the solvent cement evenly and quickly around the
outside of the pipe at a width a little greater than the depth
of the fitting socket.
• Apply a light coat of cement evenly around the inside of the
fitting socket. Avoid puddling.
• Apply a second coat of cement to the pipe end.
step e
f. joint assembly
Working quickly, insert the pipe into the fitting socket bottom and
give the pipe or fitting a 1/4 turn to evenly distribute the cement.
Do not continue to rotate the pipe after it has hit the bottom of the
fitting socket. A good joint will have sufficient cement to make a
bead all the way around the outside of the fitting hub. The fitting
will have a tendency to slide back while the cement is still wet
so hold the joint together for about 15 seconds.
step f
G. cleanup and joint movement
Remove all excess cement from around the pipe and fitting with a
dry cotton rag. This must be done while the cement is still soft.
The joint should not be disturbed immediately after the cementing
procedure, and sufficient time should be allowed for proper curing
of the joint. Exact drying time is difficult to predict because it
depends on variables such as temperature, humidity and cement
integrity. For more specific information, you should contact your
solvent cement manufacturer.
step G
Summary of Contents for she100
Page 5: ...5 General safety information...
Page 56: ...56 Notes...
Page 57: ...57 Notes...
Page 58: ...58 Notes...