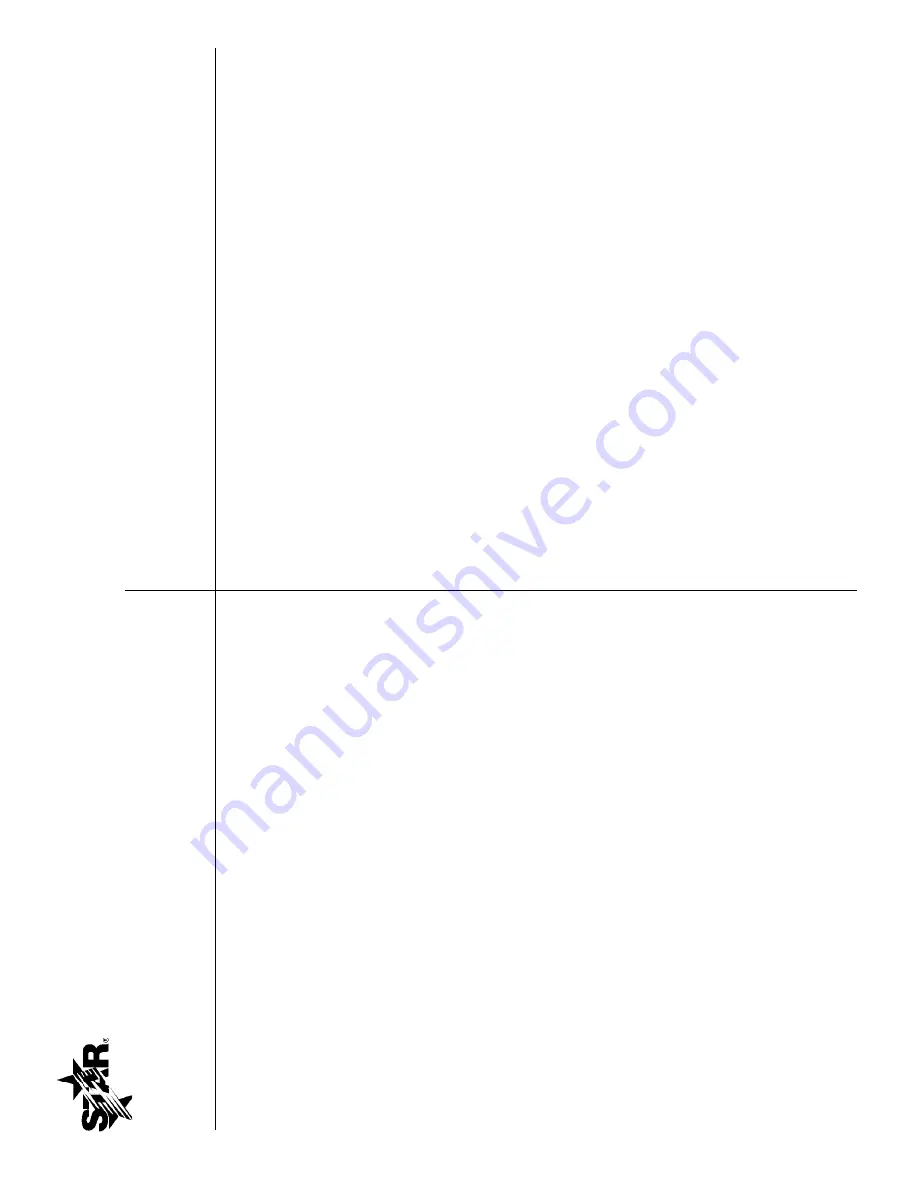
Fig
No.
Part
Number
Description
Quantity
Per
1
B5-Z9016
1
CONTROL
BOX
T
OP
LID
2
2C-H8670
4
W
ASHER #8 INT
STL
NP
3
2C-1494
4
SCREW 8-32X1/2 RHP
STL
NP
4
2C-Z3447
2
HEX NUT
W/W
ASHER 8-32, FREQ. INVER
TER
5
2E-200468
3
CLAMP
, NYLON WIRE 7/8
6
2E-Z9007
1
FREQUENCY
INVER
TER
7
2T
-Z5177
1
THERMOST
A
T
HIGH LIMIT
8
2C-Z0215
2
SCREW M4X5 ST
NP
P
AN PH
9
2E-Z5206
2
BREAKER,
CIRCUIT
-10A
10
2C-Z8652
1
CLAMP
, BLOWER 3”
11 2F-Z8616-1
1
COMBUSTION
BLOWER
12
B5-Z9028-1
1
PRESSURE HOSE, SWITCH
T
O BLOWER
13
B5-Z9008
1
CONTROL
BOX REAR COVER
14
2K-Y3240
1
BUSHING HEYCO SR 17-2
2E-Z3034
1
IEC CORD INLET
HOT
10
AMP
230 VOL
T
CE
15
2E-Z9858
1
CORD SET
, 14/3 6-15P
10'
208/240V
2E-Z7278
1
CORDSET
, UK 10A
90° BOTH ENDS 2.5METERS
UK
2E-Z0512
1
CORD SET
, CONT
. EUR 10A
CE
16
B5-Z8668
1
POWER INLET
PLA
TE
17
2C-Y2344
1
TERMINAL
GROUND
CE
UM3240, UM3255 Series Control Box
Assembly
Rev
. D 6/26/2007
18
B5-Z10050
1
CORD HOLDER - IEC INLET
CE
19
2C-200201
2
6-32 HEX NUT
,W/ST
AR W
ASHER
CE
20
2C-200004
2
SCREW
, 6-32X38PHITRU SS410N
CE
21
2C-1810
1
W
ASHER 3/16 BURR STL
NP
22
2C-08-07-0207
2
NUT
10-24 HEX STL
NP
W/LOCKW
ASH
23
2C-1515
4
SCREW 10-24X.75 ST
RH NP
24
2E-Z5163
1
IGNITION CONTROL, 24V
AC
25
2C-1496
2
SCREW 8-32 X 3/4 ST
RH NP
26
2C-Z6925
6
SCREW #8 X .5
TEK HW SS
27
2E-Z5683
2
SWITCH-DIFFERENTIAL
PRESSURE
28
2C-H1027
4
NUT
WELD 1/4-20,
ANTI ROT
A
TION, MOT
OR
29
2U-Z8629
1
GEAR
MOT
OR
W/CAP
ACIT
OR
30
B5-Z8661
1
GEAR MOT
OR COVER PLA
TE
31
2C-Z5556
4
W
ASHER, FLA
T
1/4 SS
32
2C-Z5557
4
W
ASHER, LOCK 1/4 SPLIT
SS
33
2C-Z5555
4
SCREW
,1/4-20 X 3/4 HEX SS
34
2A-Z8633
1
DRIVE
COG
35
2T
-Z5175
1
THERMOST
A
T,
COOLDOWN
TIMER
36
B5-Z9028-2
1
SUCTION HOSE, SWITCH
T
O COOKING CHAMBER
37
2E-Z7476
1
RELA
Y,
TIME
DELA
Y
38
2K-Z2895
1
BUSHING
39 1L-14-07-0100
1FT
TUBING-SILICONE 1/4 OD 1/16 W
AL
NI = NOT
ILLUSTRA
TED
Fig
No.
Part
Number
Description
Quantity
Per
Summary of Contents for Ultra-max UM3240
Page 27: ......