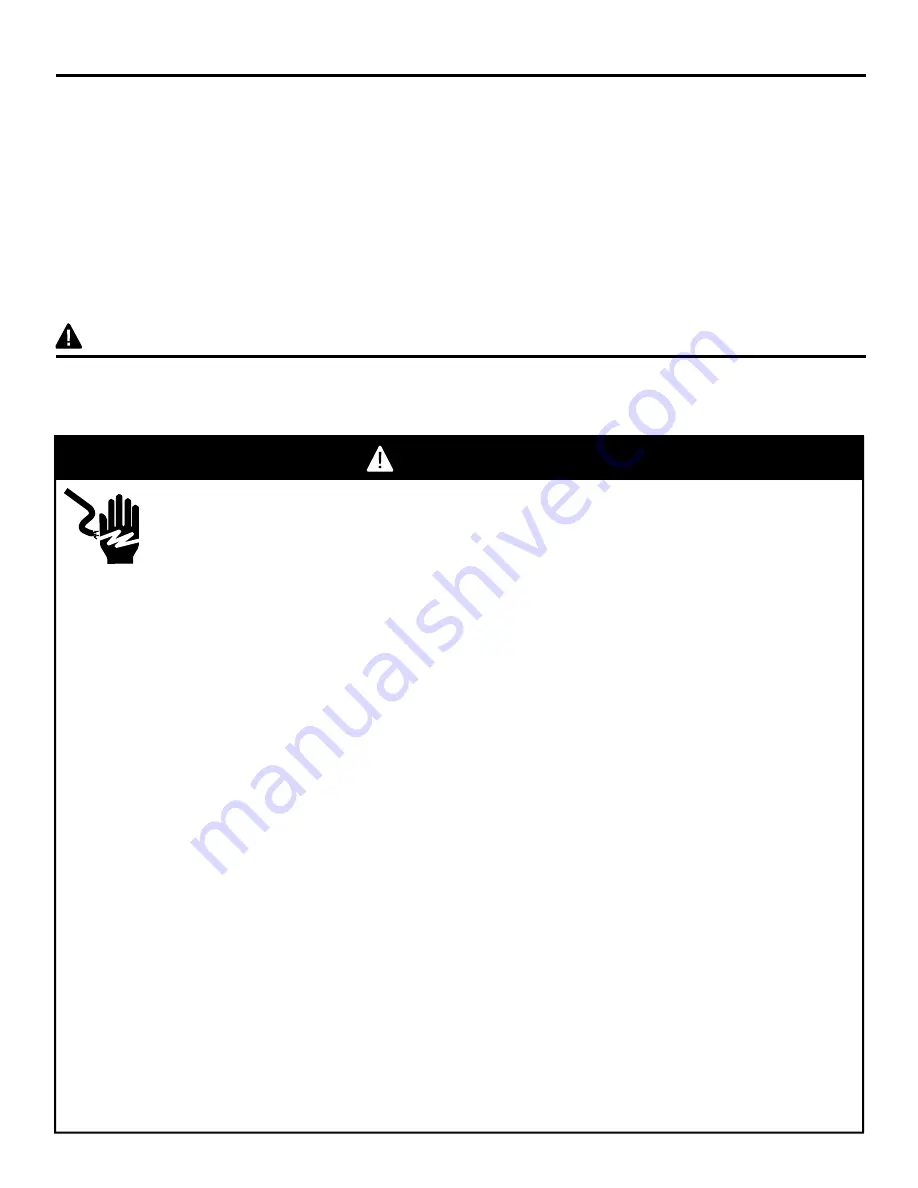
2
SAFETY INFORMATION
TABLE OF CONTENTS
Please read and understand this entire manual before attempting to assemble, operate or install the product.
Inspect all materials before installation. If parts are damaged or missing, call 1-800-742-5044 before returning to
your retailer.
Safety Information ....................................2
Package Contents ....................................4
Specifications
...........................................4
Preparation ...............................................4
General Pump Uses .................................5
Dimensions ...............................................7
Location of Grinder/Tank Unit ...................7
Toilet Assembly .........................................8
Water Supply Hookup ...............................9
Exposed Grinder/Tank Installation ..........11
Hidden Grinder/Tank Installation ............12
Piping......................................................13
Toilet Installation .....................................15
Adding Other Fixtures.............................18
Typical Installation ..................................19
Troubleshooting ......................................20
Warranty .................................................21
Replacement Parts .................................22
ELECTRICAL SHOCK HAZARD.
To help reduce the risk of electrical shock, a properly grounded receptacle or control box of
grounding type must be installed and protected by a ground fault circuit interrupter (GFCI) in
accordance with the National Electrical Code and applicable local codes. Never remove ground
pin from plug.
ELECTRICAL SHOCK HAZARD.
Make certain that the ground fault interrupter protected receptacle is within reach of the pump’s
power supply cord. DO NOT USE AN EXTENSION CORD. Extension cords that are too long
or too light do not deliver sufficient voltage to the pump motor. But more important, they could
present a safety hazard if the insulation were to become damaged or the connection end were to
fall into a damp or wet area.
ELECTRICAL SHOCK HAZARD.
Make sure the pump’s electrical supply circuit is equipped with fuses or circuit breakers of proper
capacity. A separate branch circuit, sized according to the National Electrical Code for the current
shown on the pump name plate is recommended (see Note 3).
ELECTRICAL SHOCK ALERT.
TESTING FOR GROUND. As a safety measure, each electrical outlet should be checked for
ground using an Underwriters Laboratory Listed circuit analyzer which will indicate if the power,
neutral and ground wires are correctly connected to your outlet. If they are not, call a qualified
licensed electrician.
ELECTRICAL SHOCK ALERT.
FOR YOUR PROTECTION ALWAYS DISCONNECT PUMP FROM ITS POWER SOURCE
BEFORE HANDLING. If pump is wired direct, de-energize the circuit at the control box. Grounded
pumps are supplied with a 3-prong grounded plug to help protect you against the possibility of
electrical shock. DO NOT UNDER ANY CIRCUMSTANCES REMOVE THE GROUND PIN. To
reduce the risk of electrical shock, a properly grounded receptacle of grounding type must be
installed and protected by a ground fault circuit interrupter (GFCI) in accordance with National
Electrical Code and applicable local codes.
WARNING