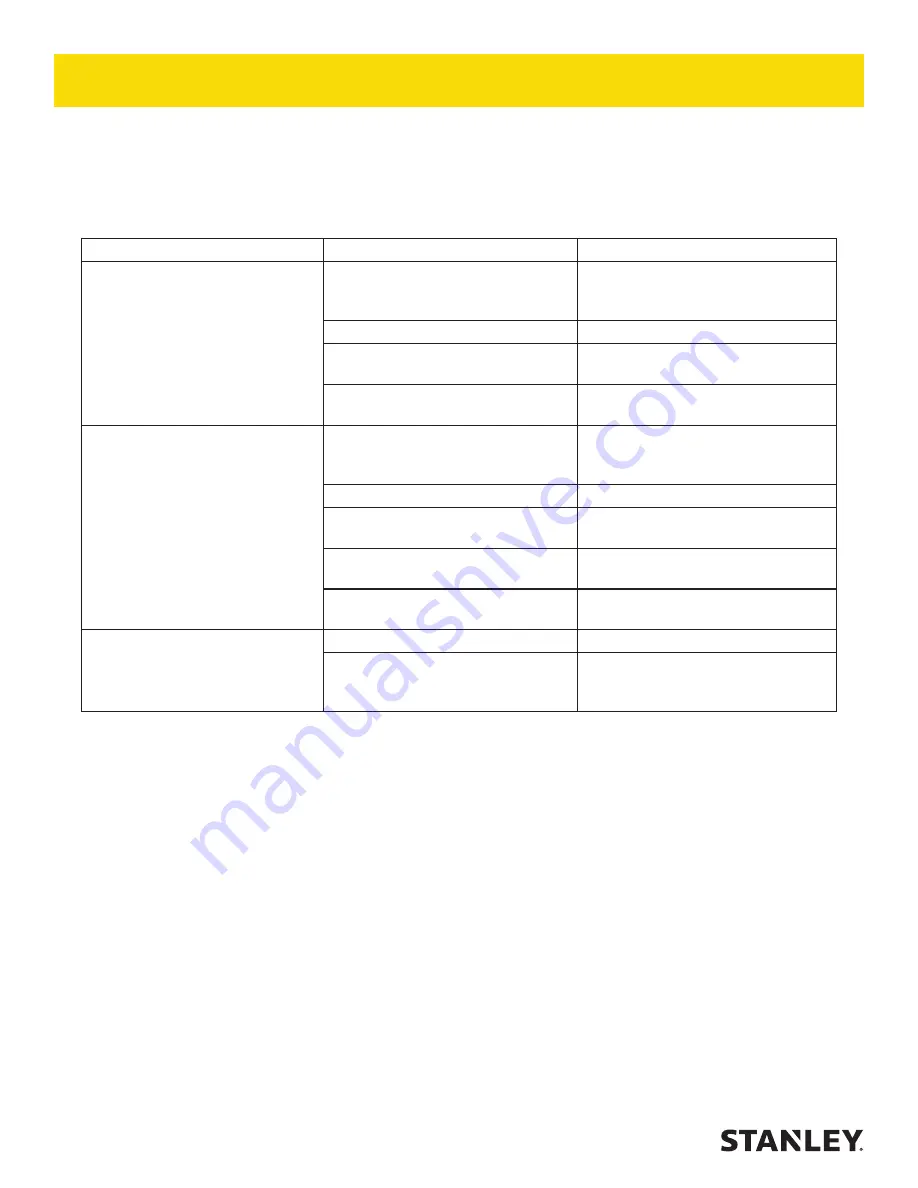
14 ► GD50
User Manual
If symptoms of poor performance develop, the following chart can be used as a guide to correct the problem.
When diagnosing faults in operation of the spike driver, always check that the hydraulic power source is supplying
the correct hydraulic flow and pressure to the spike driver as listed in the table. Use a flow meter known to be
accurate. Check the flow with the hydraulic oil temperature at least 80 °F/27 °C.
PROBLEM
CAUSE
SOLUTION
Rod driver does not run.
Power unit not functioning.
Check power unit for proper flow and
pressure (7–9 gpm
/
26–34 lpm at
2000 psi
/
140 bar).
Couplers or hoses blocked.
Remove restriction.
Pressure and return line hoses
reversed at ports.
Be sure hoses are connected to their
proper ports.
Mechanical failure of piston or
automatic valve.
Have inspected and repaired by an
authorized dealer.
Rod driver does not hit effectively. Power unit not functioning.
Check power unit for proper flow and
pressure (7–9 gpm
/
26–34 lpm at
2000 psi
/
140 bar).
Couplers or hoses blocked.
Remove restriction.
Low accumulator charge (pressure
hose will pulse more than normal).
Have recharged by an authorized
dealer.
Fluid too hot (above 140 °F
/
60 °C).
Provide cooler to maintain proper
fluid temperature.
Rod anvil is not sliding freely in the
anvil guide.
Remove, clean and replace as
necessary.
Rod driver operates slow.
Low oil flow from power unit.
Check power source for proper flow.
High back pressure.
Check hydraulic system for
excessive back pressure and correct
as required.
TROUBLESHOOTING