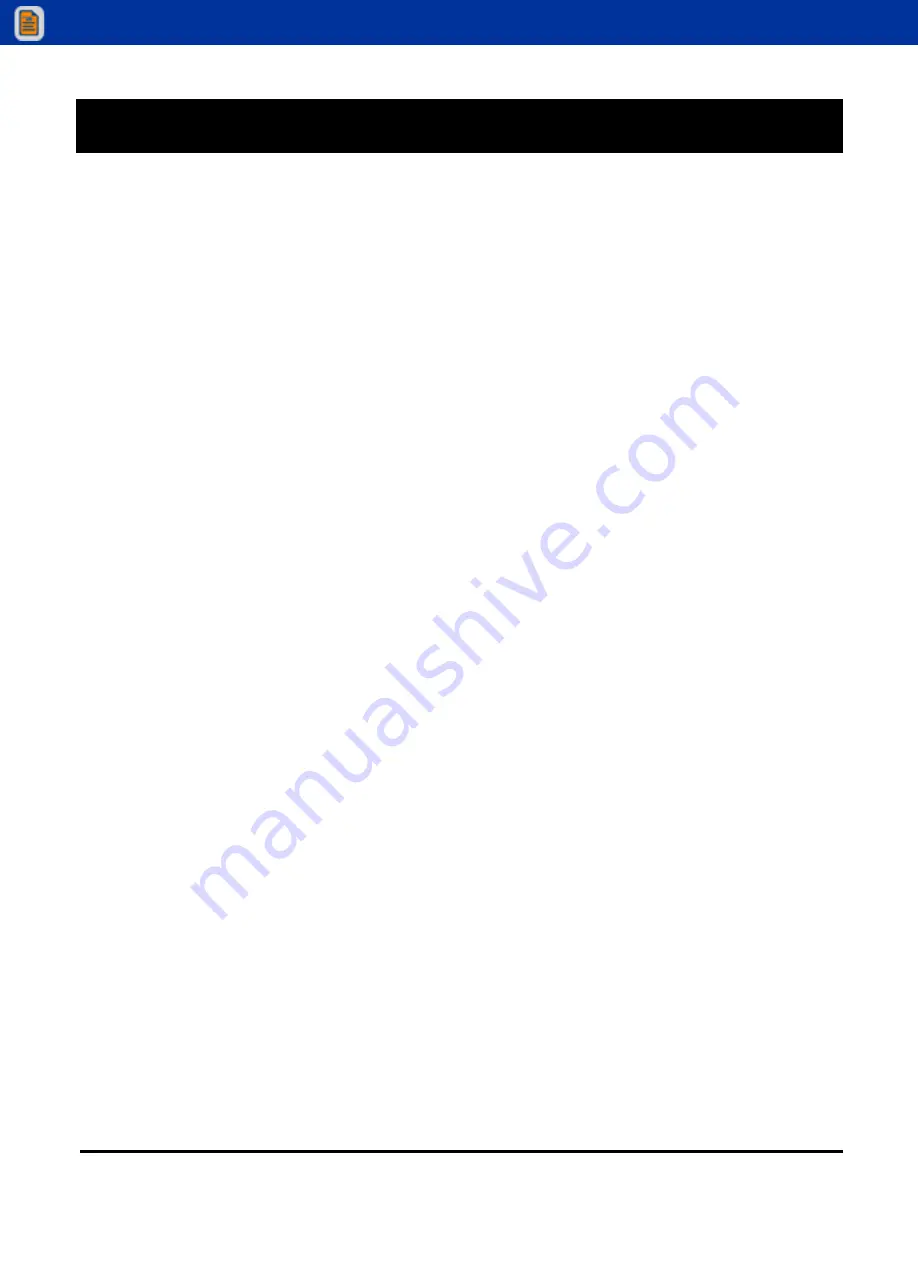
9
s
OPERATION
5000 SERIES OWNER’S MANUAL
TASK PERFORMANCE
TASK PERFORMANCE
TASK PERFORMANCE
TASK PERFORMANCE
1.
Position the 5000 crane as close to the job as possible on a firm, dry, and level surface. Avoid overhead
obstruction on the work side of the unit.
2.
Set the parking brake.
3.
Extend and lower the outriggers until firm ground contact is made. On soft ground, use bearing pads to
prevent sinking or tipping.
4.
Run the winch line out before extending the boom.
5.
Make sure the connection to the load is secure and will not come loose when lifting the load.
OVERLOAD PROTECTION
OVERLOAD PROTECTION
OVERLOAD PROTECTION
OVERLOAD PROTECTION
The 5000 crane is equipped with a counterbalance valve inside the lift cylinder to protect against overloading. In
an overload condition, the boom will not elevate. Attempts to winch the load will cause a downward feathering of
the boom until the overload condition is reduced. The counterbalance valve will also keep the boom from coming
down in the unlikely event of a rupture to the hydraulic hoses that supply oil to the lift cylinder.
A pressure sensitive switch is located in the lifting cylinder. It can sense an overload situation. This causes a
shutdown of the winch up, boom extension out, and boom elevation functions, and automatically resets after the
crane has been moved out of the overload position.
An anti-two block feature is provided on the LRX models.
ROTATION STOP
ROTATION STOP
ROTATION STOP
ROTATION STOP
A stop to prevent the unit from rotating continuously is located on the crane base. The stop is installed so that a
full 360° plus is obtained. A stop lever is attached to the turret and extends so that it will contact the rotation stop
on the base assembly. Do not remove the stop assembly. Continuous rotation will result in damage to the wiring
harness and/or hydraulic hoses.
SPEED CONTROL OPERATION
SPEED CONTROL OPERATION
SPEED CONTROL OPERATION
SPEED CONTROL OPERATION
The boom lift cylinder, extend cylinder, and rotation drive motor are preset at 2 gallons per minute (GPM). This
flow control valve is located in the valve manifold block. The winch function receives the full “required 6 GPM”
flow. An optional proportional flow control valve that controls the crane’s operation speed from 0 to 6 GPM is
available from
s
.
RELIEF VALVES
RELIEF VALVES
RELIEF VALVES
RELIEF VALVES
The 5000 crane requires a relief valve located at the reservoir to maintain crane operating pressure at 2600 PSI.
This relief valve is not supplied unless using a
s
hydraulic reservoir. It is the customer’s responsibility to
provide this relief valve when using a reservoir not supplied by
s
. The main function of this relief valve is
to prevent overloading of the system if the boom is inadvertently rotated against an immovable object, while one
of the other hydraulic functions is also being used. The relief valves would not normally require adjustment, but if
the correct relief valve setting is suspect, refer to the maintenance section of this manual for the proper
adjustment and testing procedure.
View thousands of Crane Specifications on FreeCraneSpecs.com
View thousands of Crane Specifications on FreeCraneSpecs.com