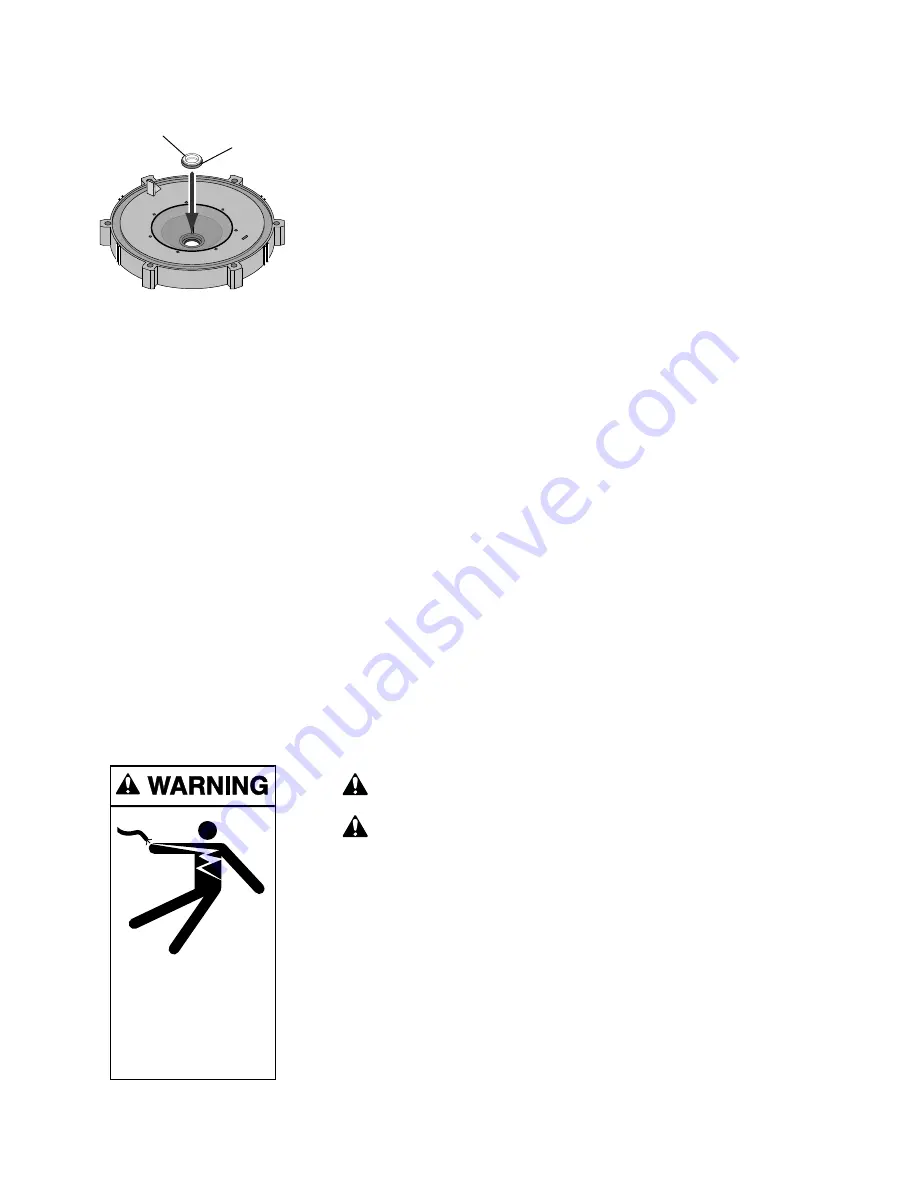
12
Pump Reassembly/Installing New Seal
1. Ceramic seat must be clean and free of dirt, grease, dust, etc. Wet outer
edge with small amount of liquid detergent; press ceramic seat into seal
plate cavity firmly and squarely with finger pressure (Fig. 8).
2. If ceramic seat will not locate properly, remove it, place
face up
on bench
and reclean cavity. Ceramic seat should now locate.
3. If seat still will not locate properly, place a cardboard washer over the
polished face and use a piece of 3/4" (19mm) standard pipe for pressing
purposes.
NOTICE: Be sure
not to scratch or mar polished surface or seal
will leak.
4. Replace slinger on end of motor shaft so that impeller sleeve will push it
into position. If slinger shows signs of wear or damage, replace it.
5. Remount seal plate on motor. Tighten bolts to 60-80 inch-lbs. (69-92
kg/cm) torque.
6. Apply a
small
amount of liquid detergent to inside diameter of rotating
half of seal.
7. Slide rotating seal member, polished carbon face out, over impeller sleeve
until rubber drive ring hits back of impeller.
NOTICE: Be sure
not to nick or scratch polished seal face; seal will leak if
face is damaged.
8. Screw impeller onto shaft (clockwise); this will automatically locate seal in
seal plate.
NOTICE:
On 2 and 2-1/2 HP models; install impeller gasket and lock
screw (left-hand thread - turn counterclockwise). Torque lock screw to
50-55 inch-lbs. (57.6-63 kg/cm).
9. Mount diffuser on seal plate; tighten screws to 10-14 inch-lbs. (11.2-16.1
kg/cm) torque.
10. Assemble motor and seal plate to pump body with nuts, flat washers and
lock washers. Torque nuts to 120-130 in-lbs. (138-150 kg/cm).
11. Prime pump according to instructions on Page 9.
TROUBLESHOOTING GUIDE
Read and understand safety and operating instructions in this manual
before doing any work on pump!
Only qualified personnel should electrically test pump motor!
FAILURE TO PUMP; REDUCED CAPACITY OR DISCHARGE PRESSURE
Suction leaks/lost prime:
1. Pump must be primed; make sure that pump volute and trap are full of
water. See priming instructions, Page 9.
2. Make sure there are no leaks in suction piping.
3. Make sure suction pipe inlet is well below the water level to prevent
pump from sucking air.
4. If suction trap gasket is defective, replace it.
5. Make sure pump is not trying to lift water more than 10'(3m).
6. Make sure suction pipe is at least 2" (51mm) in diameter.
Polished
surface
Rubber
surface
Hazardous voltage.
Can shock, burn,
or cause death.
Disconnect power
before working
on pump or motor.
Figure 8